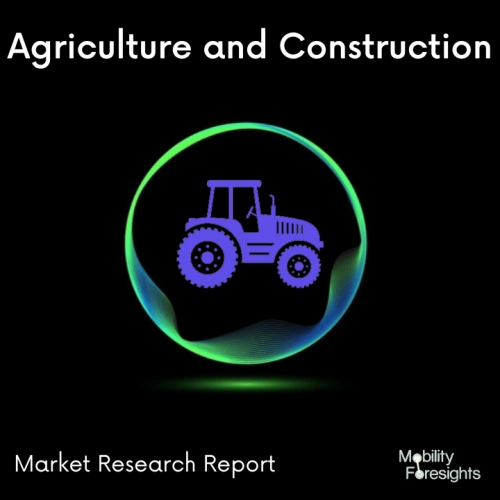
- Get in Touch with Us
Last Updated: Apr 25, 2025 | Study Period: 2024-2030
An exhaust system directs reaction exhaust gases out from a controlled combustion within an engine or stove. The complete system, which includes one or more exhaust pipes, transports burned gases from the engine.
By lowering the back pressure in the exhaust system, aftermarket exhaust items can boost peak power. These components may violate factory warranties in some cases, although the European Union Block Exemption Regulations 1400/2002 prohibit manufacturers from rejecting warranty claims if the aftermarket parts are of comparable quality and specifications to the original parts.
An exhaust pipe must be properly built to transport poisonous and/or noxious gases away from the machine's users. If indoor generators and furnaces are not properly vented to the outside, they may quickly fill an enclosed room with toxic exhaust gases such as hydrocarbons, carbon monoxide, and nitrogen oxides.
Furthermore, the gases produced by most machines are quite hot; the pipe must be heat-resistant and must not travel through or near anything that might burn or be harmed by heat.
The manifold is a component in most commercial engines that collects exhaust gas from two or more cylinders into a single pipe. In standard production automobiles, manifolds are frequently made of cast iron.
Depending on the engine, the exhaust system may have one or two channels. The flow resistance must be chosen so that the exhaust back pressure has as minimal of an impact on engine performance as feasible.
To guarantee that the exhaust system works flawlessly, it must be seen as complete and constructed as such. This implies that the design engineers must coordinate its components in accordance with the specific vehicle and engine.
S No | Overview of Development | Development Detailing | Region of Development | Possible Future Outcomes |
1 | New Holland launches range of new âultimate all-rounder tractors | New Holland has launched its T5 Utility Stage V, and T5 Electro Command Stage V tractor ranges with power upgrades. The new T5 tractors cover the utility multi-purpose tractor segment from 80 hp to 120 hp. They feature a ânew and improvedâ 4-cylinder engine with an increased displacement of 3.6 litres that delivers higher power and torque. Stage V compliance is ensured by the patented Compact HI-eSCR2 solution developed by FPT Industrial. This system integrates a Diesel Oxidation Catalyst (DOC), a particulate filtration system and a Selective Catalyst Reduction (SCR) in a single element. | Global | This would enhance better Emission Controls |
SI.no | Timeline | Developments |
1 | Q4-2021 | The US Environmental Protection Agency released funds to replace vehicles, old engines or equipment to reduce emissions under the Diesel Emissions Reduction Act (DERA) project in the Commonwealth of North Mariana Island (CNMI) regions. |
2 | Q1-2021 | The Indian government announced new rules under The Ministry of Road Transport and Highways to reduce emissions by the TREM Stage-IV emission norm for tractors, which are applicable from October 2021. |
3 | Q3-2021 | Leading manufacturer of innovative exhaust and emission systems Dinex has opened its three new distribution centers in North America for the faster delivery services. |
4 | Q2-2021 | Automotive exhaust manufacturer AP Emissions Technologies invested $400K to expand its business in Goldsboro and also increase its productions. |
Emission standards throughout the world are becoming stricter by the year, and as a result, there is a greater demand for reductions in exhaust gas emission specifics and volumes.
The combination of after-treatment devices allows car OEMs and exhaust system manufacturers to control vehicle emissions while staying under legal limits. SCR and DPF are the most often utilized after-treatment device combinations. This combination eliminates more than 70% of all gaseous and particulate pollution. In the presence of a reductant, the SCR converts NOx to N2 (nitrogen) and water, whilst the DPF filters particulate matter.
The need for vehicle weight reduction is always increasing in order to comply with rigorous pollution and fuel efficiency rules and avoid costly penalties imposed by government authorities.
The reduction in vehicle weight reduces fuel consumption and CO2 emissions considerably since a lightweight automobile requires less fuel to overcome less inertia, thus lowering the power necessary to push the vehicle.
To lessen the impact of emissions from diesel variations in diesel engines, regulatory organizations are requiring the use of gasoline versions. This has resulted in developments in gasoline variations, such as gasoline direct injection (GDI) engines, which deliver improved fuel efficiency while requiring less maintenance.
Countries that have signed on to the Paris Agreement to reduce automobile emissions aim to implement stricter emission restrictions. Countries such as Brazil, Russia, and South Africa intend to implement emission standards such as Euro 5 and Euro 6 beyond 2023. This will result in tighter pollution regulations and a reduction in vehicle weight.
To meet pollution limits, manufacturers are transitioning toward exhaust after-treatment systems using modern components and technology. As a result, the demand for exhaust systems in on-highway vehicles is predicted to rise.
The Global Tractor Exhaust System Market can be segmented into following categories for further analysis.
SI.no | Timeline | Company | Developments |
1 | Q4-2021 | Steyr | Steyr released its tractors with improved features with driver enhancing experience and less emissions. |
2 | Q4-2021 | Finse Ltd | Finse Ltd supplies heavy machinery exhaust systems for agro machineries, has designed thermal insulation for exhaust systems to reduce emissions and for a safer environment. |
3 | Q3-2021 | Dinex | Dinex designed its new OneBox exhaust system for commercial vehicles. |
4 | Q3-2021 | Deutz AG | Deutz AG released its combustion engine without emissions under the carbon neutral drive systems. The engine burns H2 by releasing low emissions for a decentralized power supply. |
5 | Q3-2021 | BASF | Top catalytic converter producer BASF acquired Zodiac Enterprises LLC which recycles metals from scrap. |
5 | Q4-2021 | Finse Ltd | Finse Ltd supplies heavy machinery exhaust systems for agro machineries, has designed thermal insulation for exhaust systems to reduce emissions and for a safer environment. |
Tractors are essential agricultural vehicles. These machines are found all over the world and range in size from simple lawn tractors to massive monsters worth hundreds of thousands of dollars.
The majority of them, however, have one thing in common: their exhaust pipes are pointed straight up in front of the driver's cab. The engine and the rolling noise created by the tyres are the primary sources of sound made by automobiles. When it comes to agricultural tractors, the engine and gearbox are mostly responsible for the primary emissions because they frequently work in the fields at moderate speeds on soft terrain.
Diesel engines in new tractors with outputs greater than 130kW have been required to meet Stage V exhaust pollution restrictions; beginning in January 2020, this will also apply to output classes ranging from 56 to 130kW. In terms of particulate emissions, the stricter weight limit values (g/kWh) have been joined by an additional number restriction (total particles/kWh), necessitating the use of closed-loop particulate filter systems.
In 2019, some tractor manufacturers completed the transition to Stage V exhaust emission engines on current model series, but others combined this with the development and presentation of new models.
Common rail fuel injection, four-valve technology, turbochargers, charge air cooling, viscous fans, and electronic engine management continue to be engine technology stalwarts for balancing power production, consumption, and emissions regulations.
In terms of exhaust emission technology, familiar technologies are also being deployed. Diesel oxidation catalytic converter (DOC), diesel particulate filter (DPF), and selective catalytic reduction (SCR) exhaust gas emissions control systems are always installed in exhaust emission Stage V engines on agricultural tractors; differences in exhaust gas recirculation (EGR) are now only found in internal engine technology.
SI.no | Timeline | Company | Developments |
1 | Q4-2021 | TAFE | Tractors and farm equipment manufacturer TAFE sales decreased 28% in Q3 from the previous year same period. |
2 | Q4-2021 | Mahindra | Leading tractor manufacturer Mahindra sold 10,379 in the third quarter of October which is an 18% decrease in sales compared to previous quarter. Mahindra Swaraj models also decreased 27% sales |
3 | Q4-2021 | Deutz AG | Deutz AG reported increased sales in the small engines segment of three or four cylinder engines of tractors with new orders of â¬485.2 million. |
4 | Q4-2021 | Force Motors | Force Motors is the only company that made positive growth in tractor sales with 5% increase in sales than the previous year quarter. |
The Chinese tractor industry is exploding in terms of growth as agriculture is getting more mechanized in China, and also due to the low-cost manufacturing providing low-cost tractors to all parts of the world. There are many factories that build tractors of the same design, and even brand name, and others that seem to be unique to their own branding and technology. Many of the manufacturers have either established new joint ventures in China or have bought into existing tractor manufacturers.
Complete Tractors has been developing the latest muffler systems under the Tractor exhaust system requirements within the tractors. These mufflers are an excellent substitute for OEM component numbers FO-35 or SBA314102140. Tractor mufflers excel in noise reduction to keep the decibel level bearable.
Our mufflers are designed to operate as well as or better than OEM counterparts. Mufflers are also made to fit certain equipment, making installation quick and simple. We make mufflers with excellent materials and professional craftsmanship that fulfil high endurance criteria for a long service life. Mufflers are also made to fit certain equipment, making installation quick and simple.
We employ high-quality materials and expert craftspeople. The Construction is done such that its primary job is to lessen the noise produced by your tractor, but it also serves additional purposes. A well-maintained muffler also has an impact on engine performance. Mufflers restrict the flow of exhaust and, as a result, produce back pressure, resulting in ideal engine efficiency.
Faurecia has created a game-changing invention that is especially well-suited for use on hybrid cars, which will account for 30% of the powertrain mix by 2025, by allowing them to run in electric mode more frequently, boosting fuel efficiency and lowering CO2 emissions. The tiny EHRS from Faurecia weighs less than 3 kilos and has best-in-class packaging, allowing installation near to the engine for optimal heat recovery.
It is the most competitive solution of its kind on the market, resulting in a 3% to 7% savings in fuel consumption in cold temperatures due to faster engine warmup and higher usage of the electric mode.
The integration of the system possibly into the commercial and agricultural class of vehicles is being progressed through with various trails of compliance being made.
Designed for optimal performance even at low exhaust temperatures, the Heated Doser helps reduce both fuel consumption and NOx emissions. It also helps reduce deposits and increase engine lifetime. Through its ability to operate rapidly even at low temperatures, the Heated Doser converts NOx particles, and is in line with upcoming Ultra Low NOx and Euro VII regulations.
Sl no | Topic |
1 | Market Segmentation |
2 | Scope of the report |
3 | Abbreviations |
4 | Research Methodology |
5 | Executive Summary |
6 | Introduction |
7 | Insights from Industry stakeholders |
8 | Cost breakdown of Product by sub-components and average profit margin |
9 | Disruptive innovation in the Industry |
10 | Technology trends in the Industry |
11 | Consumer trends in the industry |
12 | Recent Production Milestones |
13 | Component Manufacturing in US, EU and China |
14 | COVID-19 impact on overall market |
15 | COVID-19 impact on Production of components |
16 | COVID-19 impact on Point of sale |
17 | Market Segmentation, Dynamics and Forecast by Geography, 2024-2030 |
18 | Market Segmentation, Dynamics and Forecast by Product Type, 2024-2030 |
19 | Market Segmentation, Dynamics and Forecast by Application, 2024-2030 |
20 | Market Segmentation, Dynamics and Forecast by End use, 2024-2030 |
21 | Product installation rate by OEM, 2023 |
22 | Incline/Decline in Average B-2-B selling price in past 5 years |
23 | Competition from substitute products |
24 | Gross margin and average profitability of suppliers |
25 | New product development in past 12 months |
26 | M&A in past 12 months |
27 | Growth strategy of leading players |
28 | Market share of vendors, 2023 |
29 | Company Profiles |
30 | Unmet needs and opportunity for new suppliers |
31 | Conclusion |
32 | Appendix |