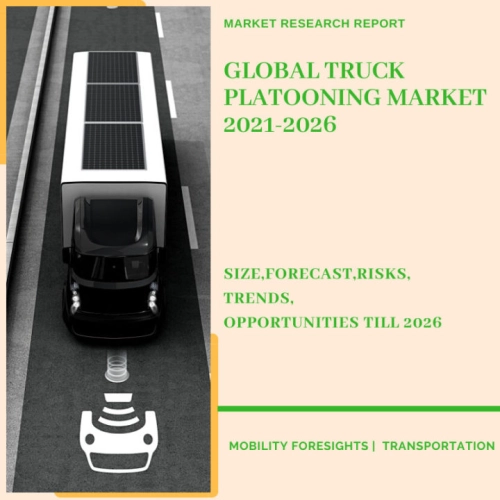
- Get in Touch with Us
Last Updated: Apr 25, 2025 | Study Period:
Truck platooning is the use of connection technologies and automated driving support systems to join two or more vehicles in a convoy. When these cars are connected for specific sections of a journey, such as on highways, they automatically maintain a fixed, tight distance between each other. Vehicle that follows behind The lead vehicle.
The truck in the front of the platoon serves as the platoon's leader, with the vehicles behind reacting and adapting to changes in its movement - requiring little to no effort from drivers. In the first case, drivers will retain control at all times, allowing them to leave the platoon and drive alone.
Truck platooning has the potential to make future road transportation safer, cleaner, and more efficient. As a result, truck manufacturers are keen to bring these platoons to European highways, and the first real-world experiments are already underway.
Truck platooning saves fuel and reduces CO2 emissions. Because trucks may travel closer together, air-drag friction is considerably decreased. Platooning can cut CO2 emissions from following cars by up to 16% and from the lead vehicle by up to 8%.
The advantages of a system in which vehicles may travel on highways with pre-set spacing between them utilizing autonomous technology are simple to grasp. Using modern technology, vehicles may create coordinated, precisely spaced convoys and therefore move closer together over long distances, reducing air drag friction, fuel consumption, and expenses.
Platooning vehicles together is a way of improving road capacity. Platoons use electrical, and potentially mechanical, connection to reduce the distance between automobiles or trucks. This feature allows many vehicles or trucks to accelerate or halt at the same time. Vehicles may follow each other more closely than they could previously.
S No | Overview of Development | Development Detailing | Region of Development | Possible Future Outcomes |
1 | Alberta highways used in national study to test automated truck convoys | Starting in November the Queen Elizabeth II highway to Edmonton and the Trans-Canada highway to Banff will have select long haul trucks travelling nose to tail that will appear far too close together to passing drivers. But it's a more efficient way of hauling goods because that short distance apart will result in a smoother traffic flow, higher traffic safety, fuel savings and a reduction in CO2 emissions. | Canada | This would enhance better Emission Controls |
SI No | Timeline | Company | Developments |
1 | May 2021 | UM-Dearborn | UM-Dearborn have collaborated with Auburn University in order to demonstrate a clear market case for the application of semi-autonomous technology in the trucking industry. |
2 | March 2021 | Volvo | Volvo has partnered with Aurora in order to accelerate the deployment of autonomous transport solutions. |
3 | January 2021 | JRSL | James Richardson & Sons Limited and Wescan Capital have announced that JRSL has acquired 100% of the shares of Bison Transport and its affiliated Companies. |
4 | January 2021 | Paccar | Paccar and Aurora have partnered to develop Autonomous trucks. |
As original equipment manufacturers (OEMs) attempt to restart production by bringing heavy investments to the market, a significant number of factors are being implemented, including an increase in demand for powerful vehicles with higher carrying capacity to handle weights and strong suspension systems, an increase in demand for fuel-efficient trucks, and strict laws and regulations related to carbon dioxide emissions. The Europe Vehicle Control and Safety Administration established new fuel efficiency criteria for heavy-duty vehicle engines powered by diesel, natural gas, and other fuels.
The severe emission regulations imposed by governments would fuel the significant market development in the special vehicles category. Because of the increased demand for more fuel-efficient and safer automobiles, automakers are significantly investing in cutting-edge vehicle technology. Truck platooning is one of the sophisticated technologies used by automakers to make trucks more efficient and safer.
The growth in the frequency of road accidents caused by driver mistake, as well as the increased emphasis on lowering transportation operational costs, are likely to boost demand in the truck platooning industry. Because of the increased need for automated technologies, truck platooning is projected to boost demand in areas such as road construction, transportation, logistics, and information technology.
Truck platooning technology is being significantly invested in by industrialized regions such as Europe and North America to meet a variety of people's demands. The major reasons driving development in European markets are technical improvements such as the integrated use of IoT and the introduction of stringent laws such as ACEA's EU General Safety Regulation requirements for vehicle safety.
The Global Truck Platooning Market can be segmented into following categories for further analysis.
SI no | Timeline | Company | Developments |
1 | November 2021 | ENSEMBLE | The Ensemble project has demonstrated the two versions of platooning viz platooning as support function and platooning as autonomous function. |
2 | October 2021 | Bison Transport | Bison is excited to be involved in the Alberta Motor Transport Associationâs (AMTA) Cooperative Truck platooning system project. |
3 | September 2021 | Bison Transport | The Alberta Motor Transport Association will test a pair of platooning trucks on the Alberta Highways between November and April. |
4 | September 2021 | Locomation | Autonomous trucking startup Locomation is set to go with two Class 8 trucks which ultimately operate without a driver in either cab. |
5 | June 2021 | Locomation | Locomation has announced that the motor carrier PGT Trucking Inc is the latest fleet to sign up for its human-guided autonomous truck convoying technology. |
6 | May 2021 | Daisy | Semi-truck fitted with Artificial Intelligence technology will soon roll on Albertaâs Queen Elizabeth II Highway in a test project by the Government of Canada. |
Truck platooning is the technique of coordinating numerous vehicles into a convoy using connective technologies and automated driving systems. It enables all of the vehicles to move extremely close together, with the lead truck controlling the overall pace of the convoy.
When the truck in front slows down, it immediately sends a signal to the platoon to brake automatically. In theory, the autonomous system's reaction time would be five times faster than that of a human driver, allowing for significantly shorter following distances.
The unique Autonomous Relay Convoying (ARC) system includes an AI-controlled follower truck that follows the human-driven leader truck using its own vision and information transmitted through dedicated short-range inter-vehicle communication (DSRC).
According to Locomation, the following truck is aware of its surroundings and is aware of possible hazards, but it leaves most of the high-level driving choices to the human and is mainly concerned with imitating the moves of the lead truck.
ARC is expected to provide several benefits due to aerodynamic-drag improvements and precise control of the vehicle by the autonomous driving system, including an estimated 30 percent or more reduction in operating cost per mile, an 8 percent reduction in fuel expense, a 2x increase in freight density per lane, and annual CO2 emissions cuts of 41 metric tonnes per tractor.
Human-guided autonomous convoys, according to Locomation, provide a "solid growth path" for higher levels of automation in the future. Nonetheless, vehicle platooning has its own set of risks.
The truck platooning and driver productivity concept of Peloton Technology Inc. is being expanded.
A driverless, completely automated following truck and a driver-controlled lead truck in a platoon are connected through a system called Automated Following that the Mountain View, California-based company is creating.
According to Peloton, the lead truck, which would be operated by a human, would use the V2V wireless signal to connect the safety systems between the trucks with a low latency. The lead truck's steering, acceleration, and radar-based braking would be controlled by the lead truck, which would have SAE Level 4 capabilities for highly autonomous driving.
The driver of the following truck steers and keeps an eye on the situation in Peloton's current Platoon Pro (an SAE Level 1 system), but the system manages the powertrain and brakes to precisely manage the following distance and to provide quick response to any acceleration or breaking the lead truck makes.
Platoon Pro is now used by six customers, and Peloton announced that more client fleet trials are in progress but did not name the fleets.
Wilson Logistics, a trucking and logistics firm based in Springfield, Missouri, and Locomation, a developer of autonomous-trucking technology, have announced a multiyear agreement.
Wilson Logistics' vehicles will be equipped with Locomation's Autonomous Relay Convoy (ARC) technology. This spring, the deal will go into effect.
According to a statement from Locomation, the three-year pilot programme will use "human-guided autonomous convoying," in which two-truck convoys with one driver in the lead truck controlling the second vehicle would be used.
Along 11 predetermined routes where Wilson operates, 62 two-truck convoys will begin the nationwide experiment.
Wilson Logistics, will advance significantly with the help of Locomation. "We'll make big achievements in reducing our energy consumption while boosting our safety," . "Not only will we increase our asset utilisation and network efficiency.
Wilson emphasised that a driver will be in the trailing vehicle at all times throughout the pilot, even though it is being driven autonomously.
SI No | Timeline | Company | Updates |
1 | Q3-2021 | Daimler | The group revenue of Daimler at the end of the third quarter was â¬40.1 billion and in 2020 the revenue was â¬40.3 billion. |
2 | Q3-2021 | Volvo | At the end of the third quarter the net sales of Volvo was SEK 85.25 billion and in the previous year the net sales was SEK 71.54 billion. |
3 | Q3-2021 | Paccar | At the end of the third quarter the net income of Paccar was $377.7 million and the net sales and revenues was $5.15 billion. |
4 | September 2021 | Man truck and bus | In Nuremberg, Manâs new group has started the construction of their production site. |
5 | August 2021 | Volvo | Volvo trucks has acquired the heavy duty truck manufacturing JMC Heavy Duty Vehicle Co. Ltd. in China. |
The safe situation is only possible in platoons with controllers since their response time is faster than that of human drivers. However, safety conditions are still being investigated due to potential hazards regarding communication failures.
These risks also highlight the need to improve the dependability of the systems engaged in this sort of work. With the maturation of vehicle-to-vehicle (V2V) communication systems, cooperative adaptive cruise control (CACC) was introduced and has become the cornerstone of truck platooning.
Volvo Group is part of the most recent developments within the Truck Platooning technologies of implementation within the real time operational space. The Volvoâs CACC technology is an improvement to current Adaptive Cruise Management (ACC) technology that allows for tighter and more precise control of the space between trucks while also increasing safety.
The sophisticated technology that enables platooning is intended to supplement rather than replace trained professional truck drivers. The advantages of platooning using CACC include faster reactions to severe braking while preserving safety, greater longitudinal control when following in a lane, lower emissions, and improved traffic flow.
The US Department of Transportation/Federal Highway Administration Advanced Research Program and Caltrans are funding the CACC technology being developed in collaboration with PATH. Cambridge Systematics, Inc., the Los Angeles County Metropolitan Transportation Authority, and the Gateway Cities Council of Governments are other project partners.
MAN trucks is part of the new development within the global market for truck platooning which is aimed at better efficiency of operations. Convoys that are well-planned and run via a wireless local area network (WLAN) actually reduce traffic congestion. Two trucks require just 50 metres of space instead of 90 metres.
Trucks travelling in a convoy take use of the slipstream of the vehicle ahead. Platoon trucks are currently kept at a spacing of 15 to 21 metres apart. A decrease of 10 to 15 metres may boost fuel savings from four percent to ten percent.
The slipstream impact would be enhanced if the GPS-based cruise control capabilities (MAN Efficient Cruise, MAN Efficient Roll) were employed, which was not feasible during the practical testing owing to limitations imposed by the authority.
Platooning technology is largely based on tried-and-true support technologies that are currently in use in regular MAN trucks. These include the ACC adaptive cruise control, the EBA emergency braking system, a serial radar, and a serial camera.
Sl no | Topic |
1 | Market Segmentation |
2 | Scope of the report |
3 | Abbreviations |
4 | Research Methodology |
5 | Executive Summary |
6 | Introduction |
7 | Insights from Industry stakeholders |
8 | Cost breakdown of Product by sub-components and average profit margin |
9 | Disruptive innovation in the Industry |
10 | Technology trends in the Industry |
11 | Consumer trends in the industry |
12 | Recent Production Milestones |
13 | Component Manufacturing in US, EU and China |
14 | COVID-19 impact on overall market |
15 | COVID-19 impact on Production of components |
16 | COVID-19 impact on Point of sale |
17 | Market Segmentation, Dynamics and Forecast by Geography, 2021-2026 |
18 | Market Segmentation, Dynamics and Forecast by Product Type, 2021-2026 |
19 | Market Segmentation, Dynamics and Forecast by Application, 2021-2026 |
20 | Market Segmentation, Dynamics and Forecast by End use, 2021-2026 |
21 | Product installation rate by OEM, 2021 |
22 | Incline/Decline in Average B-2-B selling price in past 5 years |
23 | Competition from substitute products |
24 | Gross margin and average profitability of suppliers |
25 | New product development in past 12 months |
26 | M&A in past 12 months |
27 | Growth strategy of leading players |
28 | Market share of vendors, 2021 |
29 | Company Profiles |
30 | Unmet needs and opportunity for new suppliers |
31 | Conclusion |
32 | Appendix |