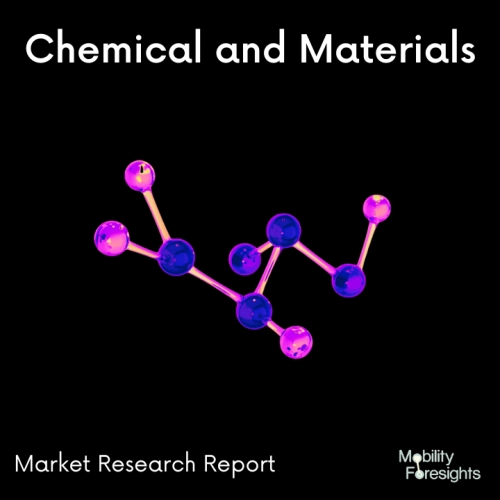
- Get in Touch with Us
Last Updated: Apr 25, 2025 | Study Period: 2024-2030
The usage of TUBULAR FILM as flexible packaging material is very appropriate. One piece of TUBULAR FILM can be quickly turned into a PE-bag by being torn off the roll and then sealed using a film sealing mechanism. TUBULAR FILM accommodates your schedule.
TUBULAR FILM is best suited for wrapping extremely long things like pipes. Because a packaging unit's interior is hermetically sealed when it is heat sealed, there is no need to worry about moisture seeping into or out of the plastic. The box is simply ripped open.
The most cutting-edge manufacturing techniques are used to create the tubular film, which can be delivered flat, bellowed, plain, or printed depending on the need.
The enormous diameter of the reels combined with specific formulations with high sealability and resistance make this packaging both practical and dependable for the packaging of fertilizers, seeds, polymers, aggregates, and industrial items in general.
The Global Tubular Film market accounted for $XX Billion in 2021 and is anticipated to reach $XX Billion by 2030, registering a CAGR of XX% from 2024 to 2030.
FFS multilayer tubular film production is a new production site that Kazanorgsintez has opened. The business appears small; it has only two machines when seen in relation to the size of the enormous enterprise.
In the short term, however, output will allow for meeting the flexible packaging needs of all KOS facilities. Before, the company also produced its own product bags. However, they were forced to partially reject this packaging after re-equipping multiple plants.
The KOS facilities now have new packaging equipment that can pack up to 2,000 bags each hour. Older film production techniques were unable to produce the volumes or quality needed for such quick packing. Production of FFS multilayer tubular films (shaping, filling, tightening).
Ten outdated furnaces with a combined capacity of just 66 tonnes per hour will be replaced by four new pyrolysis units with a capacity of 72 tonnes per hour. As a result, considering prior feedstock volumes, production of marketable ethylene will rise to 19,000 tonnes annually. It is also intended to increase the conversion of ethane and propane as feedstock after the furnaces are launched.
A New Method for Tubular Anodic Aluminum Oxide Film Batch Production for Filtering Applications Three-dimensional tubular anodic aluminum oxide (AAO) films have benefits over two-dimensional AAO films for mass transfer and gas diffusion due to their larger surface areas and nanochannels. In this study, a method for batch manufacture of tubular AAO films employing a 6061 Al tube was devised.
The tubular AAO films include open nano-channels on both sides with pores that are typically 60 nm in size and 108â109 pore/cm2 in density. The porous AAO material with the nano-channel structure was discovered to display dialysis behavior, allowing for liquid/gas exudation through diffusion between the inner and outer surfaces of the tubular AAO films.
Ordered straight channels with a diameter of 10-500 nm, a pore density of 107â1011 pore/cm2, and a thickness of 1-300 m are provided by high-quality AAO (anodic aluminum oxide) sheets. AAO is flexible, has a high mechanical strength, and can be employed in energy or medicinal applications including drug delivery and detection.
Large AAO surfaces can be used to absorb medications or biomarkers, and the releasing behavior can also be managed based on heat sensitivity. AAO has also been used to convert methanol and carbon dioxide (CO2) into energy. These photocatalytic devices can be utilized to recycle carbon dioxide into organic compounds by adding photocatalyst particles to the AAO surface.
The three-dimensional structure of AAO films for medical and energy applications has practical advantages over two-dimensional (2D) AAO films due to the characteristics of greater surface areas and nanochannels for mass distribution and gas diffusion. The inclusions in the porous AAO structure cause AAO to have a lower melting point than pure alumina.
Sulfuric acid was used as the electrolyte for the alumina film formulations that Spooner presented: Al2O3 (78.9% weight percentage), Al2O3 + H2O, Al2 (SO4)3, and H2O AAO has a melting point close to 1200 °C and a stability temperature of 1000 °C, which is lower than the 2017 °C for bulk alumina (Al2O3). The AAO structure, which can withstand temperatures up to 1000 °C, is stable enough to serve as a model for the CaO-CaCO3 reaction at 894 °C.
Sl no | Topic |
1 | Market Segmentation |
2 | Scope of the report |
3 | Abbreviations |
4 | Research Methodology |
5 | Executive Summary |
6 | Introduction |
7 | Insights from Industry stakeholders |
8 | Cost breakdown of Product by sub-components and average profit margin |
9 | Disruptive innovation in the Industry |
10 | Technology trends in the Industry |
11 | Consumer trends in the industry |
12 | Recent Production Milestones |
13 | Component Manufacturing in US, EU and China |
14 | COVID-19 impact on overall market |
15 | COVID-19 impact on Production of components |
16 | COVID-19 impact on Point of sale |
17 | Market Segmentation, Dynamics and Forecast by Geography, 2024-2030 |
18 | Market Segmentation, Dynamics and Forecast by Product Type, 2024-2030 |
19 | Market Segmentation, Dynamics and Forecast by Application, 2024-2030 |
20 | Market Segmentation, Dynamics and Forecast by End use, 2024-2030 |
21 | Product installation rate by OEM, 2023 |
22 | Incline/Decline in Average B-2-B selling price in past 5 years |
23 | Competition from substitute products |
24 | Gross margin and average profitability of suppliers |
25 | New product development in past 12 months |
26 | M&A in past 12 months |
27 | Growth strategy of leading players |
28 | Market share of vendors, 2023 |
29 | Company Profiles |
30 | Unmet needs and opportunity for new suppliers |
31 | Conclusion |
32 | Appendix |