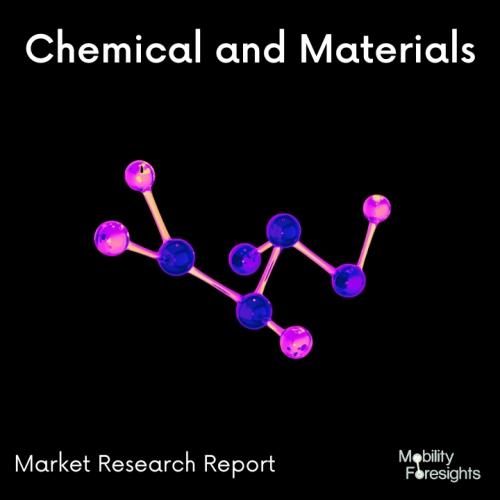
- Get in Touch with Us
Last Updated: Apr 25, 2025 | Study Period: 2024-2030
Tungsten Rhenium is one of many metal alloys available from American Elements under the brand name AE Alloys. AE Alloys are generally available in most amounts as bar, ingot, ribbon, wire, shot, sheet and foil.
Metal powder, submicron powder, and nanoscale, targets for thin film deposition, and pellets for chemical vapor deposition (CVD) and physical vapor deposition (PVD) applications are also available in ultra high purity and high purity forms.
When applicable, American Elements produces to many standard grades, including Mil Spec (military grade); ACS, Reagent, and Technical Grade; Food, Agricultural, and Pharmaceutical Grade; Optical Grade, USP, and EP/BP (European Pharmacopoeia/British Pharmacopoeia).
There is standard and bespoke packaging available. Bearing assembly, ballast, casting, step soldering, and radiation are some of the primary uses.
Other rhenium alloys containing tungsten and molybdenum are used in photoflash bulbs for filaments, grid heaters, cathode cups, and ignitor wires.Rhenium alloys are utilized in nuclear reactors, semiconductors, thermocouples, electronic tube components, gyroscopes, rocket parts, electrical contacts, thermionic converters, and a variety of high-temperature aerospace components.
Recent advancements in the creation of net forms using powder metallurgy and rhenium manufacturing processes have resulted in considerable time and money savings.
Both rhenium and tungsten are refractory metals with high ductility and strength. The addition of rhenium to tungsten can improve the ductility, specific resistance, and vibration strength qualities of the W-Re alloy. These values are substantially within the range of superplastic materials. W-Re alloy is suitable for elements of electric vacuum devices such as cathodes, heaters, radio tube grids and so on.
They can also be used with thermocouples and electrical connections.Wrought's characteristics are improved with rhenium. Tungsten-rhenium alloys are more ductile at low temperatures, making them easier to manufacture. High-temperature stability has also been enhanced. Because the effect rises with rhenium content, tungsten alloys are made with Re, which is the solubility limit.
Tungsten-rhenium wire was initially developed in an attempt to make a wire that was more ductile following recrystallization. This enables the wire to satisfy certain performance goals such as enhanced vibration resistance, increased ductility, and higher resistivity. X-ray sources are one use for tungsten-rhenium alloys.
Both elements high melting points, along with their high atomic masses, render them resistant to long-term electron impact.Rhenium tungsten alloys are also used to detect temperatures as thermocouples.
Rhenium's excellent temperature stability, low vapor pressure, superior wear resistance, and resistance to arc corrosion make it helpful in self-cleaning electrical connections. The discharge that happens during electrical switching, in particular, oxidizes the contacts. However, because rhenium oxide Re2O7 is volatile, it is eliminated during the discharge.
Rhenium, like tantalum and tungsten, has a high melting point and a low vapor pressure. As a result, rhenium filaments are more stable when operated in an oxygen-containing environment rather than a vacuum.These filaments are commonly used in mass spectrometers, ion gauges, and photographic photoflash lights.
The Global Tungsten Rhenium Alloy Market accounted for $XX Billion in 2023 and is anticipated to reach $XX Billion by 2030, registering a CAGR of XX% from 2024 to 2030.
SAM offers the finest Tungsten-Rhenium Alloy on the market. They may even create unique forms based on specifications or drawings. The products have found applications in the furnace, electronics, and aircraft industries.Stanford Advanced Materials (SAM) has decades of expertise in providing high-quality Tungsten-Rhenium Alloy at reasonable pricing.
DARPA has awarded Elementum 3D a Direct to Phase II SBIR contract to create a durable, cost-effective additive manufacturing (AM) technology for fabricating complex-shaped components from the refractory metal rhenium (Re).
Rhenium, as a refractory metal, can resist high temperatures and has the second highest melting point of all metal elements, behind only tungsten. As a result, rhenium is in high demand as a component material capable of improving the performance and prolonging the life of rocket and missile propulsion systems.
While rhenium is widely used as an alloying ingredient in nickel-based superalloys, its application as a base alloy is restricted due to difficulties in conventional manufacturing. It is currently expensive to shape rhenium into the intricate geometries required for these applications.
Furthermore, certain geometries are just unattainable with current machining and forming technologies. The granted SBIR includes a substantial endeavor to investigate and develop an AM fabrication approach to print components with geometrical characteristics that cannot be manufactured using standard manufacturing techniques such as powder metallurgy (PM) and electrical discharge machining (EDM).
Elementum 3D has a proven track record in developing high quality, repeatable print processes for other refractory metals such as tantalum, tungsten, tungsten heavy alloy, and tungsten-rhenium alloy as a recognised industry leader in developing new materials and processes for printing complex components using laser powder bed fusion (LBPF).
This knowledge will enable Elementum 3D to build a rhenium feedstock supply chain and print process appropriate for critical applications in a timely and effective manner.
Sl no | Topic |
1 | Market Segmentation |
2 | Scope of the report |
3 | Abbreviations |
4 | Research Methodology |
5 | Executive Summary |
6 | Introduction |
7 | Insights from Industry stakeholders |
8 | Cost breakdown of Product by sub-components and average profit margin |
9 | Disruptive innovation in the Industry |
10 | Technology trends in the Industry |
11 | Consumer trends in the industry |
12 | Recent Production Milestones |
13 | Component Manufacturing in US, EU and China |
14 | COVID-19 impact on overall market |
15 | COVID-19 impact on Production of components |
16 | COVID-19 impact on Point of sale |
17 | Market Segmentation, Dynamics and Forecast by Geography, 2024-2030 |
18 | Market Segmentation, Dynamics and Forecast by Product Type, 2024-2030 |
19 | Market Segmentation, Dynamics and Forecast by Application, 2024-2030 |
20 | Market Segmentation, Dynamics and Forecast by End use, 2024-2030 |
21 | Product installation rate by OEM, 2023 |
22 | Incline/Decline in Average B-2-B selling price in past 5 years |
23 | Competition from substitute products |
24 | Gross margin and average profitability of suppliers |
25 | New product development in past 12 months |
26 | M&A in past 12 months |
27 | Growth strategy of leading players |
28 | Market share of vendors, 2023 |
29 | Company Profiles |
30 | Unmet needs and opportunity for new suppliers |
31 | Conclusion |
32 | Appendix |