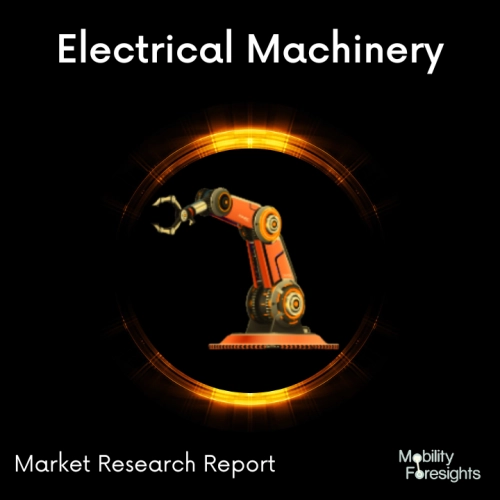
- Get in Touch with Us
Last Updated: Apr 25, 2025 | Study Period: 2023-2030
Turbomachinery inspection systems are designed to provide a comprehensive and thorough assessment of the condition of turbines and other mechanical components used in industrial operations.They are typically used to detect problems such as wear and tear, vibration, and corrosion that can negatively affect the performance and safety of the machinery.
The inspection system typically includes sensors and other monitoring devices that measure the various parameters of the machinery such as temperature, pressure, and vibration. The data is then analyzed to detect any potential problems.
Inspection systems can be used to identify potential issues before they become serious and costly. This proactive approach helps to reduce downtime and costs associated with fixing machinery after it has already broken down.
Inspection systems also help to identify areas where improvements can be made to increase efficiency and reduce energy consumption.Inspection systems are designed to be user-friendly and require minimal training for operators. They typically incorporate features such as automated self-diagnosis and reporting, which can help to simplify the process of collecting and analyzing data.
Furthermore, the systems typically come with a range of tools that can be used to diagnose and repair any problems that are identified.Turbomachinery inspection systems provide a cost-effective and reliable way to ensure that your machinery is working at its optimum level.They provide peace of mind that your equipment is safe and reliable, and can help to reduce the chances of unexpected breakdowns or costly repairs.
The Global Turbomachinery inspection system market accounted for $XX Billion in 2022 and is anticipated to reach $XX Billion by 2030, registering a CAGR of XX% from 2023 to 2030.
For designing, testing, and training turbomachinery in support of the aerospace and energy sectors, SwRI is well-known worldwide. Their services are intended to assist clients in comprehending the significance of vibration, thermal stress, and material selection during the course of turbomachinery life.
To provide people with a comprehensive understanding of the impact that various impellers, rotor blades, compressors, and piping systems can have on the thermodynamics and power cycles of turbomachinery equipment and systems, they integrate multiple disciplines from aerospace engineering, materials science, and mechanical engineering.
Every stage of the turbomachinery development workflow is made possible by NREC's "art to part" software tool chain. Users are given complete creative control over the "art" of designing turbomachinery by using their design software solutions.
Along with integrated analysis tools to confirm durability and performance, these systems offer an agile interface for 1D and 3D conceptual design. In order to increase the design area and make the probable possible, they also provide optimisation solutions that complement their products.
In addition to reducing overall design time, streamlining the manufacturing process, and attaining greater performance, these solutions' vertical integration with the rest of the Agile product suite enables the user to go from digital to physical.
The MAX-PAC CAM software has been updated to include new surface milling features that allow users to create and mill arbitrary surfaces outside of the bladed arrangement.
A Stock Chain Manager has also been added to MAX-PAC, allowing users to quickly determine how much stock is left over after an operation and utilise it for simulations and other activities.
These modifications reduce the amount of time lost creating toolpaths in other systems to integrate with MAX-PAC and enable businesses who depend on it to use it for tasks more than only bladed components.With the latest updates to TurboOpt II, automated optimisation is now simpler than before.
Sl no | Topic |
1 | Market Segmentation |
2 | Scope of the report |
3 | Abbreviations |
4 | Research Methodology |
5 | Executive Summary |
6 | Introduction |
7 | Insights from Industry stakeholders |
8 | Cost breakdown of Product by sub-components and average profit margin |
9 | Disruptive innovation in the Industry |
10 | Technology trends in the Industry |
11 | Consumer trends in the industry |
12 | Recent Production Milestones |
13 | Component Manufacturing in US, EU and China |
14 | COVID-19 impact on overall market |
15 | COVID-19 impact on Production of components |
16 | COVID-19 impact on Point of sale |
17 | Market Segmentation, Dynamics and Forecast by Geography, 2023-2030 |
18 | Market Segmentation, Dynamics and Forecast by Product Type, 2023-2030 |
19 | Market Segmentation, Dynamics and Forecast by Application, 2023-2030 |
20 | Market Segmentation, Dynamics and Forecast by End use, 2023-2030 |
21 | Product installation rate by OEM, 2023 |
22 | Incline/Decline in Average B-2-B selling price in past 5 years |
23 | Competition from substitute products |
24 | Gross margin and average profitability of suppliers |
25 | New product development in past 12 months |
26 | M&A in past 12 months |
27 | Growth strategy of leading players |
28 | Market share of vendors, 2023 |
29 | Company Profiles |
30 | Unmet needs and opportunity for new suppliers |
31 | Conclusion |
32 | Appendix |