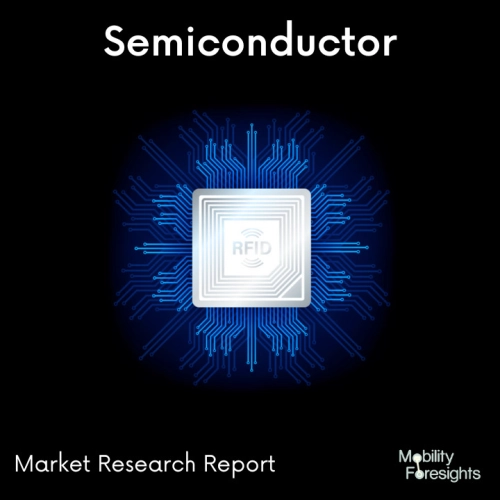
- Get in Touch with Us
Last Updated: Apr 25, 2025 | Study Period: 2023-2030
Factory automation is essential for streamlining production procedures and boosting overall productivity in today's continuously changing industrial landscape. Sensors, which act as the automated systems' eyes and ears, are at the center of the automation revolution.
They deliver up-to-the-minute information on the industrial environment, allowing robots to decide wisely and carry out tasks precisely and accurately.
The purpose of factory automation sensors is to detect and keep track of numerous physical factors in a production environment. Depending on the requirements of the particular application, these sensors can monitor a variety of factors like temperature, pressure, proximity, level, flow, vibration, and many more.
Having the capacity to gather data in real-time is one of the main benefits of employing sensors in industrial automation. Control systems and algorithms use this data to automate procedures, keep track of the condition of the equipment, guarantee the quality of the output, and boost overall operational effectiveness.
Sensors provide rapid changes and interventions by continually monitoring the production environment, minimizing downtime, eliminating waste, and optimizing resource use.
In industrial automation, a variety of sensors are used, each with a distinct function. For instance, proximity sensors allow machines to start or stop operations based on the presence or absence of things in a certain region. Temperature sensors keep an eye on the temperature to avoid overheating or guarantee the right operating temperatures.
While level sensors monitor the amount of material in tanks or containers, pressure sensors measure the pressure levels of fluids or gasses. These are only a handful of the numerous types of sensors that are employed in factory automation.
The rise of Industry 4.0 and the Internet of Things (IoT), as well as sensor technology advancements, have further revolutionized factory automation. The Industrial Internet of Things (IIoT) is a network of interconnected devices created by IoT-enabled sensors that can now communicate with one another and send data wirelessly.
With the use of real-time analytics, predictive maintenance, and remote monitoring made possible by this connection, manufacturers are able to make data-driven choices and increase efficiency.
The UAE Factory Automation Sensor Market accounted for $XX Billion in 2022 and is anticipated to reach $XX Billion by 2030, registering a CAGR of XX% from 2023 to 2030.
The brand-new optical sensor from Omron is designed to find flaws in food goods including cracks, bruising, and foreign objects using a camera. It may be applied to a number of food manufacturing processes, including packaging, distribution, and meat processing.
New wireless sensor from Siemens for machine health monitoring: The health of the machines at a factory is monitored by this sensor using wireless technology. Vibration, temperature, and current are a few examples of early warning indications that it can see and send notifications to operators so they may take remedial action before a machine breaks.
The latest sensor from ABB for gauging material thickness: This sensor measures the thickness of materials including metal, plastic, and glass sheets using ultrasonic technology. Numerous manufacturing processes, including metalworking, plastics processing, and glass manufacture, can all benefit from its utilization.
Sl no | Topic |
1 | Market Segmentation |
2 | Scope of the report |
3 | Abbreviations |
4 | Research Methodology |
5 | Executive Summary |
6 | Introduction |
7 | Insights from Industry stakeholders |
8 | Cost breakdown of Product by sub-components and average profit margin |
9 | Disruptive innovation in the Industry |
10 | Technology trends in the Industry |
11 | Consumer trends in the industry |
12 | Recent Production Milestones |
13 | Component Manufacturing in US, EU and China |
14 | COVID-19 impact on overall market |
15 | COVID-19 impact on Production of components |
16 | COVID-19 impact on Point of sale |
17 | Market Segmentation, Dynamics and Forecast by Geography, 2023-2030 |
18 | Market Segmentation, Dynamics and Forecast by Product Type, 2023-2030 |
19 | Market Segmentation, Dynamics and Forecast by Application, 2023-2030 |
20 | Market Segmentation, Dynamics and Forecast by End use, 2023-2030 |
21 | Product installation rate by OEM, 2023 |
22 | Incline/Decline in Average B-2-B selling price in past 5 years |
23 | Competition from substitute products |
24 | Gross margin and average profitability of suppliers |
25 | New product development in past 12 months |
26 | M&A in past 12 months |
27 | Growth strategy of leading players |
28 | Market share of vendors, 2023 |
29 | Company Profiles |
30 | Unmet needs and opportunity for new suppliers |
31 | Conclusion |
32 | Appendix |