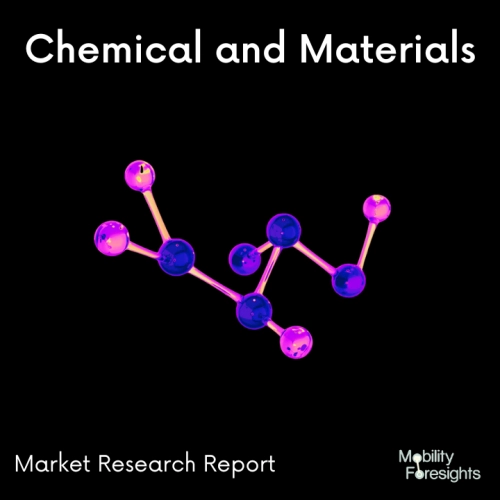
- Get in Touch with Us
Last Updated: Apr 25, 2025 | Study Period: 2024-2030
Steel is a metal alloy mainly made up of iron, with trace amounts of carbon and other elements. Steel normally has a carbon content of 0.2% to 2.1% by weight. Steel is one of the most commonly used materials in manufacturing, infrastructure, transportation, and construction because of its strength, resilience, and adaptability.
It can be easily shaped and welded, which makes it useful for many different applications. Some examples of these include building structures and bridges, machinery, automobile parts, and household appliances.
The manufacturing of steel has a long history in the United Kingdom, and it has been vital to the growth of the national economy. The UK steel sector has had to contend with difficulties like heightened competition from around the world, volatile raw material prices, and problems with energy expenses.
The UK steel industry is under growing pressure to implement more ecologically friendly and sustainable practices, much like many other industries.To improve their competitiveness, a few steel companies in the UK have placed a strong emphasis on innovation and technology adoption.
The UK steel market accounted for $XX Billion in 2023 and is anticipated to reach $XX Billion by 2030, registering a CAGR of XX% from 2024 to 2030.
International trade dynamics impact the steel market in the United Kingdom. The nation is a net exporter of steel products. The UK's steel demand is directly correlated with the performance of important industries like construction and automotive.
The sector has experienced consolidation, and in an effort to become more competitive and efficient, some businesses have made investments in updating their facilities. In an effort to become more competitive and efficient, some businesses have made investments in modernising their facilities.
To become more competitive, a few steel companies in the UK have prioritised innovation and technology adoption. This trend includes investments in R&D as well as the investigation of novel steelmaking techniques.
The UK steel industry, like many others, is under growing pressure to implement more ecologically friendly and sustainable practices. This covers initiatives to lower carbon emissions, boost energy effectiveness, and look into greener production techniques.
Drax and British Steel have an agreement in place to investigate the possibility of using Drax's steel to construct the largest carbon capture project in the world, valued at billions of pounds, at Drax's power plant in the UK.
The significant infrastructure project will require about 13,000 tonnes of steel, including beams made at British Steel's steelworks in Teesside and Scunthorpe.
Drax hopes to protect and create thousands of jobs in the North by sourcing up to 80% of the goods and services required to develop BECCS in the UK from British companies.
They are glad to be collaborating with Drax to investigate the potential that this significant infrastructure project offers, both for the application of its steel products and for the acquisition of skills in the steel supply chain necessary to facilitate the growth of CCUS expertise in the UK.
Ecoke, a new electric steelmaking technique, is introduced by LIBERTY Steel UK to lower CO2 emissions. Through its GREENSTEEL strategy, LIBERTY aims to lead the transformation of the steel manufacturing industry, and the ecoke initiative is a part of that effort.
Compared to conventional coal-based blast furnaces, which produce the great majority of the steel produced in the UK, production at LIBERTY's electric arc furnace in Rotherham produces only 10% of the direct emissions.
Ecoke has a minimum of 30% secondary biomass, which results in a 30% reduction in CO2. Ecoke is charged into the electric arc furnace using the scrap basket, just like anthracite, and the briquettes are delivered to the site in packaging akin to that of anthracite.
This makes ecoke an excellent choice for steelmaking operations.Without negatively affecting the production process, the significant decreases in CO2 emissions that ecoke permits can aid in further decarbonising both their production and the larger steel industry.
LIBERTY Steel UK is the third largest steel manufacturer in the country, with a footprint that covers nine sites across England, Scotland and Wales. It employs over 2,000 people and has an annual steel rolling capacity approaching two million tonnes.It has capabilities ranging from liquid steel production through to high value precision-engineered products, sold around the globe.
Rainham Steel is UKâs foremost independent Steel Stockholder and Distributor. The company employs over 180 members of staff and manages its own fleet of 50 Heavy Goods Vehicles.The flagship 70 acre facility is primarily chosen for its locality to the nearby British Steel mills, as well as offering ease of access to the dock facilities for imports and exports.
CELSA Steel UK is the largest steel recycling company in the United Kingdom. From their facilities in Cardiff, they have capacity to produce 1.2 million tonnes of low emission circular steel, from UK sourced scrap metal. Celsa directly employs over 750 staff and several hundred sub-contractors in South Wales.
Sl no | Topic |
1 | Market Segmentation |
2 | Scope of the report |
3 | Abbreviations |
4 | Research Methodology |
5 | Executive Summary |
6 | Introduction |
7 | Insights from Industry stakeholders |
8 | Cost breakdown of Product by sub-components and average profit margin |
9 | Disruptive innovation in the Industry |
10 | Technology trends in the Industry |
11 | Consumer trends in the industry |
12 | Recent Production Milestones |
13 | Component Manufacturing in US, EU and China |
14 | COVID-19 impact on overall market |
15 | COVID-19 impact on Production of components |
16 | COVID-19 impact on Point of sale |
17 | Market Segmentation, Dynamics and Forecast by Geography, 2024-2030 |
18 | Market Segmentation, Dynamics and Forecast by Product Type, 2024-2030 |
19 | Market Segmentation, Dynamics and Forecast by Application, 2024-2030 |
20 | Market Segmentation, Dynamics and Forecast by End use, 2024-2030 |
21 | Product installation rate by OEM, 2024 |
22 | Incline/Decline in Average B-2-B selling price in past 5 years |
23 | Competition from substitute products |
24 | Gross margin and average profitability of suppliers |
25 | New product development in past 12 months |
26 | M&A in past 12 months |
27 | Growth strategy of leading players |
28 | Market share of vendors, 2024 |
29 | Company Profiles |
30 | Unmet needs and opportunity for new suppliers |
31 | Conclusion |
32 | Appendix |