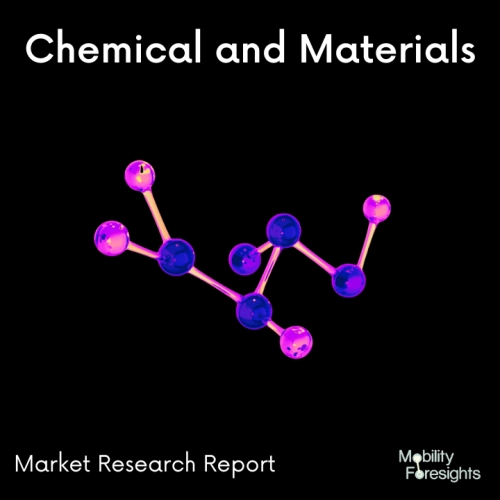
- Get in Touch with Us
Last Updated: Apr 26, 2025 | Study Period: 2024-2030
Applications include missile, satellite, and airplane fuselage and part utilization. The creation of satellites and projectiles requires the use of ultra-high-tensile carbon fiber. It has superior elasticity and tensile strength, is significantly lighter than aluminum, and reduces projectile. Carbon fibers, also known as carbon fibers or CF, graphite fiber, or graphite fiber, are fibers with a diameter of between 5 and 10 micrometer's and are primarily made of carbon atoms.
High stiffness, high tensile strength, high strength to weight ratio, good chemical resistance, high temperature tolerance, and minimal thermal expansion are only a few benefits of carbon fibers. Because of these qualities, carbon fiber is widely used in the military, motorsports, aerospace, civil engineering, and other competitive sports.
Nonetheless, they are relatively pricey when compared to fibers that are similar, like glass, basalt, or plastic. The carbon atoms are linked together in crystals that are roughly parallel to the fiber's long axis to create carbon fiber because this crystal alignment gives the fiber a high strength-to-volume ratio (in other words, it is strong for its size).
The tow, which may be used on its own or woven into a fabric, is made up of thousands of carbon fibers. To create a composite, carbon fibers are typically mixed with other materials. For instance, when infused with a plastic resin and baked, it creates carbon-fiber-reinforced polymer, also known as carbon fiber, which has a very high strength-to-weight ratio and is incredibly hard but slightly fragile.
The Global Ultra-High-Tensile Carbon Fiber market accountedfor $XX Billion in 2023 and is anticipated to reach $XX Billion by 2030, registering a CAGR of XX% from 2024 to 2030.
Today, Toray Industries, Inc. announced the development of thermoplastic pellets and a high tensile modulus carbon fiber that are perfect for using in injection molding. The pellets will make it possible to produce intricate, stiff, and light parts quickly and efficiently, reducing the impact on the environment.
These developments might significantly improve cost performance. Toray overcame this difficulty in the development project revealed today by pursuing more advancements with its TORAYCA MX series control technology to produce 7-micron fibers with homogenous internal structures.
The end result was a fiber that delivered significantly improved cost performance and had a tensile modulus of elasticity of 390 GPA, which is around 70% greater than the standard level of the TORAYCA series offered for industrial applications.
An ultra-high-tensile carbon fiber with the designation H3065 (T-1000 class) has been disclosed by Hyosung Advanced Materials. It possesses tensile strength and elasticity of at least 6.4 GPA and 295 GPA, respectively. The technique is applicable to a variety of industries, such as aerospace and defense.
Investigations have been made into the tensile characteristics and fracture behavior of carbon fibers with ultrahigh tensile strength PAN-based (T1000GB), ultrahigh modulus pitch-based (K13D), and high ductility pitch-based (XN-05).
Tensile strength statistical distributions were characterized. According to calculations, the Weibull moduli of the T1000GB, K13D, and XN-05 fibers are 5.9, 4.2, and 7.9, respectively. The findings unambiguously demonstrate that for carbon fires based on pitch and PAN, the Weibull modulus drops as the tensile modulus and mean tensile strength rise.
Sl no | Topic |
1 | Market Segmentation |
2 | Scope of the report |
3 | Abbreviations |
4 | Research Methodology |
5 | Executive Summary |
6 | Introduction |
7 | Insights from Industry stakeholders |
8 | Cost breakdown of Product by sub-components and average profit margin |
9 | Disruptive innovation in the Industry |
10 | Technology trends in the Industry |
11 | Consumer trends in the industry |
12 | Recent Production Milestones |
13 | Component Manufacturing in US, EU and China |
14 | COVID-19 impact on overall market |
15 | COVID-19 impact on Production of components |
16 | COVID-19 impact on Point of sale |
17 | Market Segmentation, Dynamics and Forecast by Geography, 2024-2030 |
18 | Market Segmentation, Dynamics and Forecast by Product Type, 2024-2030 |
19 | Market Segmentation, Dynamics and Forecast by Application, 2024-2030 |
20 | Market Segmentation, Dynamics and Forecast by End use, 2024-2030 |
21 | Product installation rate by OEM, 2023 |
22 | Incline/Decline in Average B-2-B selling price in past 5 years |
23 | Competition from substitute products |
24 | Gross margin and average profitability of suppliers |
25 | New product development in past 12 months |
26 | M&A in past 12 months |
27 | Growth strategy of leading players |
28 | Market share of vendors, 2023 |
29 | Company Profiles |
30 | Unmet needs and opportunity for new suppliers |
31 | Conclusion |
32 | Appendix |