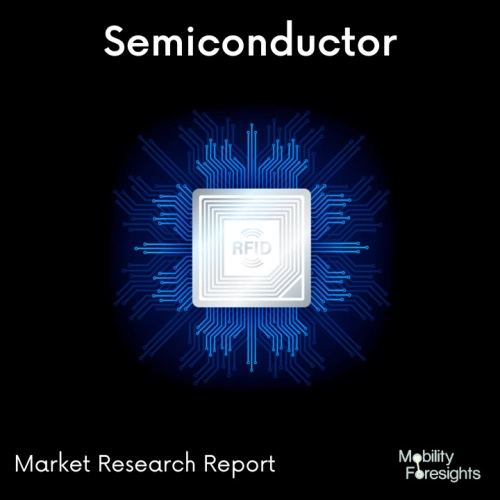
- Get in Touch with Us
Last Updated: Apr 25, 2025 | Study Period: 2023-2030
In order to decrease signal delay and enhance the functionality of integrated circuits, ultra low-k dielectric films are a particular kind of material utilised in microelectronics.
Since it has a low dielectric constant (k value), electrical impulses can travel through it more quickly than through conventional dielectric materials, which have larger k values.
As integrated circuits have shrunk to nanoscale sizes, the utilisation of extremely low-k dielectric films has grown in significance.
This is because the interconnects that transmit electrical signals become more capacitive and resistive as a chip's feature sizes shrink. This may result in signal delay, which could lower the circuit's performance.
Typically, low density, high porosity organic or inorganic materials are used to create ultra low-k dielectric films. The material's pores lessen the density, which also lessens the dielectric constant.
Chemical vapour deposition, spin coating, and plasma-enhanced chemical vapour deposition are just a few of the methods used to deposit these layers.
The low density and large porosity of extremely low-k dielectric films might make them more brittle and prone to breakage during processing, which is one of their problems.
This may result in decreased manufacturing yield and reliability problems. Researchers are striving to create novel materials and deposition methods that can maintain low-k characteristics while also enhancing the mechanical properties of the films in order to overcome these difficulties.
Global Ultra low-K dielectric film market accounted for $XX Billion in 2022 and is anticipated to reach $XX Billion by 2030, registering a CAGR of XX% from 2023 to 2030.
Black Diamond II, a low k solution from Applied Materials, uses NanoCure UV curing technology to produce an ultra-low-k dielectric film and offers a k-value of less than 2.5.
Black Diamond chemical vapour deposition (CVD) low k film from Applied Materials is being used by Taiwan Semiconductor Manufacturing Co. (TSMC) to produce their 0.13-micron copper chips.
Moreover, TSMC and Applied are collaborating to apply the technology in TSMC's next 0.2 performance processors.
Using NanoCure UV curing technology, Applied Materials has introduced Black Diamond II low k solution with a k-value of less than 2.5. For the production of its copper chips, TSMC uses Applied's Black Diamond CVD low k film, and it intends to do the same for its next-generation chips.
Many businesses have decided on their preferred low-k material, including IBM's SiLK dielectric material and Black Diamond dielectric materials from AMD, Motorola, and TSMC.
Sl no | Topic |
1 | Market Segmentation |
2 | Scope of the report |
3 | Abbreviations |
4 | Research Methodology |
5 | Executive Summary |
6 | Introduction |
7 | Insights from Industry stakeholders |
8 | Cost breakdown of Product by sub-components and average profit margin |
9 | Disruptive innovation in the Industry |
10 | Technology trends in the Industry |
11 | Consumer trends in the industry |
12 | Recent Production Milestones |
13 | Component Manufacturing in US, EU and China |
14 | COVID-19 impact on overall market |
15 | COVID-19 impact on Production of components |
16 | COVID-19 impact on Point of sale |
17 | Market Segmentation, Dynamics and Forecast by Geography, 2023-2030 |
18 | Market Segmentation, Dynamics and Forecast by Product Type, 2023-2030 |
19 | Market Segmentation, Dynamics and Forecast by Application, 2023-2030 |
20 | Market Segmentation, Dynamics and Forecast by End use, 2023-2030 |
21 | Product installation rate by OEM, 2023 |
22 | Incline/Decline in Average B-2-B selling price in past 5 years |
23 | Competition from substitute products |
24 | Gross margin and average profitability of suppliers |
25 | New product development in past 12 months |
26 | M&A in past 12 months |
27 | Growth strategy of leading players |
28 | Market share of vendors, 2023 |
29 | Company Profiles |
30 | Unmet needs and opportunity for new suppliers |
31 | Conclusion |
32 | Appendix |