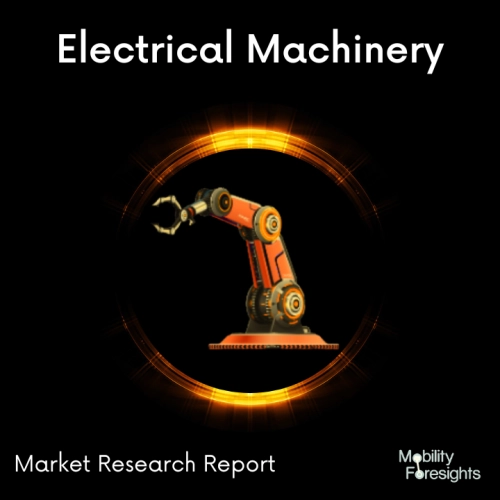
- Get in Touch with Us
Last Updated: Jul 15, 2025 | Study Period: 2025-2031
Ultra-precision machines are high-accuracy systems used in the fabrication of complex components in industries like aerospace, semiconductors, optics, and medical devices.
These machines achieve nanometer to sub-micron level tolerances by minimizing thermal deformation, mechanical vibration, and positioning errors.
Key equipment includes ultra-precision turning machines, grinding machines, micro-milling machines, and diamond turning lathes.
Growth in advanced electronics, quantum optics, photonics, and wafer-level packaging is fueling demand for ultra-precision machining capabilities.
Technologies like air-bearing spindles, hydrostatic slideways, and advanced servo-control systems enable high-stability and high-accuracy operations.
Asia-Pacific dominates in terms of consumption, led by semiconductor and precision optics manufacturing in Japan, South Korea, and China.
Major companies include Moore Nanotechnology, AMETEK Precitech, Kugler GmbH, LT Ultra Precision Technology, and Innolite GmbH.
Integration of computer-aided design (CAD), real-time monitoring, and machine learning-based error compensation is becoming standard in next-gen systems.
The market is experiencing strong demand from defense, aerospace optics, and EUV lithography tooling segments.
Supply chain localization and vertical integration trends are reshaping vendor strategies to reduce reliance on foreign precision components.
Ultra-precision machines are specialized systems designed for machining parts that require exceptionally high dimensional and surface finish accuracy. These machines are capable of producing tolerances in the range of nanometers, making them indispensable in the manufacturing of optical lenses, aerospace gyroscope housings, photonic components, and semiconductor wafers.
Unlike traditional machining, ultra-precision machining leverages temperature-controlled environments, vibration isolation platforms, and high-resolution motion control systems to eliminate even the smallest deviations. The global push for miniaturization, coupled with the increasing complexity of components in defense, photonics, and medical diagnostics, is significantly increasing the adoption of these machines.
The demand for ultraprecise components used in next-generation chips, LIDAR optics, fiber optic connectors, and imaging systems has led to extensive R&D and customization in machine design. OEMs are integrating data-driven optimization systems, tool condition monitoring, and predictive maintenance into ultra-precision platforms, transforming them into intelligent production tools capable of consistent nano-scale repeatability.
The global ultra-precision machine market was valued at USD 2.6 billion in 2024 and is expected to reach USD 6.9 billion by 2031, growing at a CAGR of 15.1% over the forecast period.
Rising investments in semiconductor fabrication, aerospace optics, and ultra-thin medical devices are driving market expansion. Nations are expanding cleanroom manufacturing and vertically integrated production lines that depend heavily on ultra-precision machining. The market is also seeing new entrants developing AI-driven automation modules and adaptive control strategies to simplify operation without compromising precision.
North America and Europe are leaders in machine development and R&D, while the Asia-Pacific region leads in adoption and scale. With increasing geopolitical focus on technological independence, several countries are investing in domestic production capabilities using ultra-precision platforms, particularly in chip packaging, metrology optics, and nanotechnology.
In the coming years, the ultra-precision machine market is expected to become a core pillar of advanced manufacturing. As industries move toward atomic-level control in semiconductor etching and optical alignment, ultra-precision machines will play an essential role in enabling next-gen fabrication.
Expect innovations such as AI-enhanced toolpath correction, closed-loop feedback systems, and real-time surface metrology integration. Multi-axis hybrid machines combining additive manufacturing with ultra-precision finishing are also under development to reduce cycle time and increase design flexibility.
Moreover, the rise of quantum computing, biomedical microinstruments, and space-grade photonics will open niche but high-value verticals for ultra-precision systems. As sustainability becomes critical, energy-efficient drives and zero-lubricant technologies will also shape future product offerings.
Growth of Nanomanufacturing Applications:
The rise of nanomanufacturing for sensors, MEMS, and quantum devices is significantly increasing the need for ultra-precision machines. These systems are capable of maintaining structural integrity and finish at scales below 100 nm, which is vital for emerging fields like atomic layer deposition and nano-imprint lithography.
Demand for Freeform Optics and Complex Geometries:
Defense and aerospace industries are driving the need for ultra-precision diamond turning of freeform optical components. These geometries enhance performance in high-energy laser systems and space-based imaging, requiring machines that support multi-axis tool control and sub-micron stability.
Adoption of Hybrid Machining Platforms:
Manufacturers are adopting hybrid platforms that combine ultra-precision grinding, turning, and even additive processes. These systems offer a single setup solution for complex geometries, enhancing accuracy and reducing part handling errors while increasing throughput in small-batch production.
Digital Twin and Predictive Analytics Integration:
Advanced software tools now allow real-time digital twinning of the machining environment, enabling predictive error correction, tool wear analysis, and condition-based maintenance. These innovations reduce downtime and improve yield consistency across complex, high-value components.
Expansion of Semiconductor and Optoelectronics Industries:
The semiconductor sector's transition to advanced packaging and EUV lithography requires ultraprecise fixtures, stages, and optics—all of which depend on ultra-precision machining. Similarly, growth in fiber optics, imaging sensors, and photonic devices supports consistent demand for nanometer-level surface finishes.
Rising Demand from Aerospace and Defense:
Aerospace applications such as inertial navigation systems, laser targeting optics, and satellite gyroscope housings depend on sub-micron geometrical tolerances. These mission-critical components are increasingly being sourced from ultra-precision machining vendors who can ensure dimensional stability under extreme conditions.
Miniaturization of Medical Devices and Diagnostic Tools:
Micro-catheters, implantable devices, and endoscopic tools require precision at scales unattainable by conventional machining. Ultra-precision machines offer repeatability and biocompatible surface finishing that are vital for ensuring safety and effectiveness in clinical environments.
Shift Toward High-Precision Tooling in Automotive and EVs:
Electric vehicles require compact high-performance components such as high-speed rotor shafts and optical sensors for ADAS systems. These are manufactured with ultra-precision machines to ensure durability and seamless integration into increasingly tight mechanical architectures.
High Capital Investment and Operating Costs:
Ultra-precision machines are expensive to acquire, install, and maintain. They require climate-controlled cleanroom environments and specialized operators, which limit accessibility for small manufacturers despite the growing need for precision components.
Skill Gaps and Talent Shortage:
Operating ultra-precision equipment requires highly trained professionals in nanomechanics, materials science, and CNC control. The global shortage of such skilled labor is hindering the optimal utilization of these machines and slowing down production scalability.
Sensitivity to Environmental Variables:
Temperature fluctuations, vibration, and air quality can significantly impact machining accuracy. Ultra-precision systems must operate in tightly controlled conditions, necessitating infrastructure upgrades that increase total project costs and deployment time.
Supply Chain Dependency for Specialized Components:
Many key components such as air-bearing spindles, hydrostatic stages, and optical sensors are sourced from a limited number of global suppliers. This creates vulnerability in the supply chain, especially during geopolitical disruptions or trade restrictions.
Ultra-Precision Turning Machines
Ultra-Precision Grinding Machines
Micro-Milling Machines
Diamond Turning Machines
Hybrid Ultra-Precision Platforms
Air-Bearing Technology
Hydrostatic Motion Guides
Servo and Linear Motor Systems
CNC Control with Nanoscale Feedback
Toolpath Simulation & Compensation Software
Semiconductor Fabrication
Optics Manufacturing
Aerospace Components
Medical Micromachining
Metrology Equipment
Quantum & Photonic Devices
Electronics and Semiconductors
Aerospace and Defense
Automotive and EVs
Medical and Life Sciences
Research Institutions and Labs
North America
Europe
Asia-Pacific
Latin America
Middle East & Africa
Moore Nanotechnology launched its next-generation Nanotech 450UPL system with upgraded control and improved damping for extreme precision applications.
AMETEK Precitech introduced hybrid turning-grinding platforms aimed at photonics and IR optics production.
LT Ultra unveiled an ultra-fast micro milling machine for high-volume production of medical microtools.
Kugler GmbH collaborated with aerospace firms to develop large-diameter freeform optic machines for space applications.
Innolite GmbH integrated real-time interferometric surface measurement into its latest ultra-precision lathes.
How many Ultra-Precision Machines are manufactured per annum globally? Who are the sub-component suppliers in different regions?
Cost Breakdown of a Global Ultra-Precision Machine and Key Vendor Selection Criteria
Where is the Ultra-Precision Machine manufactured? What is the average margin per unit?
Market share of Global Ultra-Precision Machine market manufacturers and their upcoming products
Cost advantage for OEMs who manufacture Global Ultra-Precision Machine in-house
Key predictions for next 5 years in the Global Ultra-Precision Machine market
Average B2B Ultra-Precision Machine market price in all segments
Latest trends in the Ultra-Precision Machine market, by every market segment
The market size (both volume and value) of the Ultra-Precision Machine market in 2025–2031 and every year in between
Production breakup of the Ultra-Precision Machine market, by suppliers and their OEM relationship
Sl no | Topic |
1 | Market Segmentation |
2 | Scope of the report |
3 | Abbreviations |
4 | Research Methodology |
5 | Executive Summary |
6 | Introduction |
7 | Insights from Industry stakeholders |
8 | Cost breakdown of Product by sub-components and average profit margin |
9 | Disruptive innovation in the Industry |
10 | Technology trends in the Industry |
11 | Consumer trends in the industry |
12 | Recent Production Milestones |
13 | Component Manufacturing in US, EU and China |
14 | COVID-19 impact on overall market |
15 | COVID-19 impact on Production of components |
16 | COVID-19 impact on Point of sale |
17 | Market Segmentation, Dynamics and Forecast by Geography, 2024-2030 |
18 | Market Segmentation, Dynamics and Forecast by Product Type, 2024-2030 |
19 | Market Segmentation, Dynamics and Forecast by Application, 2024-2030 |
20 | Market Segmentation, Dynamics and Forecast by End use, 2024-2030 |
21 | Product installation rate by OEM, 2023 |
22 | Incline/Decline in Average B-2-B selling price in past 5 years |
23 | Competition from substitute products |
24 | Gross margin and average profitability of suppliers |
25 | New product development in past 12 months |
26 | M&A in past 12 months |
27 | Growth strategy of leading players |
28 | Market share of vendors, 2023 |
29 | Company Profiles |
30 | Unmet needs and opportunity for new suppliers |
31 | Conclusion |
32 | Appendix |