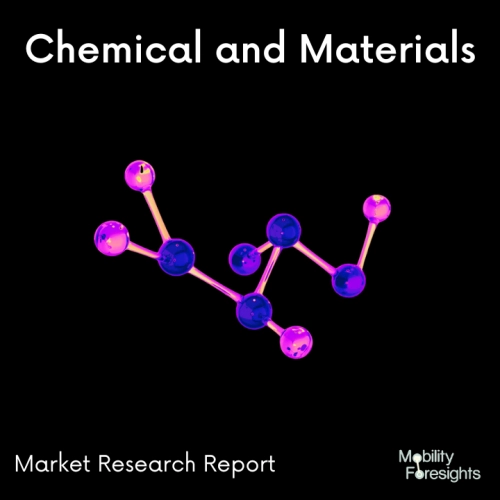
- Get in Touch with Us
Last Updated: Apr 25, 2025 | Study Period: 2024-2030
To incorporate graphene into composites, the graphene must be dispersed/exfoliated as single nano-sheets uniformly into the formulation. The higher the grade of deagglomeration, the better the extraordinary material properties are exploited.
Ultrasonic dispersion enables for a superior particle distribution and dispersion stability â even when formulating at high concentrations and viscosities. Ultrasonic processing of graphene gives outstanding dispersion qualities and excels conventional mixing methods by far.
In order to lend composites the outstanding material characteristics of graphene such as strength, graphene must be dispersed into a matrix or applied as a thin-film coating onto a substrate.
Agglomeration, sedimentation, and the dispersion into a matrix (or particle distribution on the substrate, respectively) are important factors that influence the resulting materialâs properties.
Due to its hydrophobic nature, the preparation of a stable and highly concentrated graphene dispersion without surfactants or dispersants is a challenging task. To overcome the van der Waals forces, strong shear forces generated by ultrasonic cavitation are the most sophisticated method to prepare stable dispersions.
The Global Ultrasonic Graphene Dispersion Equipment market accounted for $XX Billion in 2023 and is anticipated to reach $XX Billion by 2030, registering a CAGR of XX% from 2024 to 2030.
Scientz The Ultrasonic Graphene dispersion Equipment - The graphene ultrasonic automatic processing equipment uses an ultrasonic peeling method. Ultrasonic dispersion has been a very useful tool in the fields of chemistry and materials engineering.
When the speed of ultrasonic waves propagates in a dense phase between liquids, the liquid flows to generate thousands of tiny bubbles which form and grow in the negative pressure region formed by the longitudinal propagation of the ultrasonic waves, and are rapidly closed in the positive pressure region.
In the process called "sound cavitation" effect, the bubble closure can form an instantaneous high pressure of more than 500 atmospheres, the local hot spot temperature can reach 5000 ° C, the heat and cold exchange rate is greater than 109 K / s, and the continuously generated high pressure And the high temperature is like a series of small "explosions" constantly impacting, causing the graphene oxide sheets to peel off quickly.
Sl no | Topic |
1 | Market Segmentation |
2 | Scope of the report |
3 | Abbreviations |
4 | Research Methodology |
5 | Executive Summary |
6 | Introduction |
7 | Insights from Industry stakeholders |
8 | Cost breakdown of Product by sub-components and average profit margin |
9 | Disruptive innovation in the Industry |
10 | Technology trends in the Industry |
11 | Consumer trends in the industry |
12 | Recent Production Milestones |
13 | Component Manufacturing in US, EU and China |
14 | COVID-19 impact on overall market |
15 | COVID-19 impact on Production of components |
16 | COVID-19 impact on Point of sale |
17 | Market Segmentation, Dynamics and Forecast by Geography, 2024-2030 |
18 | Market Segmentation, Dynamics and Forecast by Product Type, 2024-2030 |
19 | Market Segmentation, Dynamics and Forecast by Application, 2024-2030 |
20 | Market Segmentation, Dynamics and Forecast by End use, 2024-2030 |
21 | Product installation rate by OEM, 2023 |
22 | Incline/Decline in Average B-2-B selling price in past 5 years |
23 | Competition from substitute products |
24 | Gross margin and average profitability of suppliers |
25 | New product development in past 12 months |
26 | M&A in past 12 months |
27 | Growth strategy of leading players |
28 | Market share of vendors, 2023 |
29 | Company Profiles |
30 | Unmet needs and opportunity for new suppliers |
31 | Conclusion |
32 | Appendix |