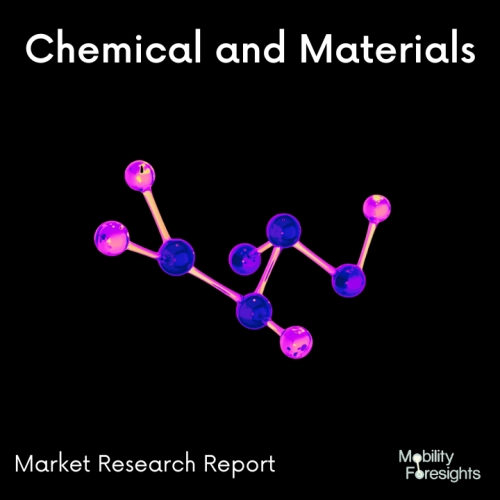
- Get in Touch with Us
Last Updated: Jun 17, 2025 | Study Period: 2024-2030
In the US, aluminum is vital to many areas, including economic expansion, technical development, and environmental initiatives. It is essential in many applications due to its adaptability, durability, and lightweight.
The aircraft sector is among the principal areas where aluminum excels. Its high strength-to-weight ratio improves performance and fuel efficiency, making it the material of choice for building aircraft and spacecraft. Furthermore, aluminum is widely used in the automobile industry to lighten vehicles and increase fuel efficiency, which supports continuous initiatives to lower greenhouse gas emissions and improve environmental sustainability.
Because of its strength and resistance to corrosion, aluminum is also widely used in the construction industry. It is a common material for structural elements in buildings, bridges, and infrastructure projects. Aluminum's malleability and recyclability also serve the packaging sector by lowering waste and environmental effects.
metal is widely used in consumer goods manufacturing, including computers, cell phones, and appliances. This is because metal can effectively disperse heat and offer structural support, all while keeping a lightweight and attractive form. Its application guarantees food preservation and hygienic practices in packaging materials like foil and aluminum cans.
A substantial contributor to the US economy and a source of employment possibilities outside of its industrial uses is the aluminum sector. It also supports recycling and lowers carbon footprint, which are aims of sustainability. Altogether, aluminum is essential to the US economy and propels environmental responsibility, economic expansion, and innovation in a variety of sectors.
The US Aluminum Market is expected to reach USD XX billion by 2035, growing at a compound annual growth rate (CAGR) of XX% from 2025 to 2035. The market is poised for sustained growth, driven by technological advancements, the shift toward sustainable manufacturing, and increasing demand for lightweight materials across various industries. Emerging markets in Asia-Pacific, particularly China and India, are expected to contribute significantly to the market’s growth as urbanization, industrialization, and infrastructure development continue at a rapid pace.
In conclusion, the US Aluminum Market is experiencing robust growth, fueled by demand from industries such as automotive, aerospace, construction, and packaging. However, challenges such as raw material price volatility and environmental concerns regarding production processes remain key issues that companies must address. The continued innovation in aluminum alloys, recycling technologies, and sustainable practices will play a crucial role in shaping the future of the market.
The innovative business Alloy Enterprises, which is changing the metal manufacturing sector, has announced the launching of its aluminum cold plate component. In its third year of operation, the forward-thinking tech startup is expanding its production fab facilities and staff, extending its workforce, and adding thermal management applications to its array of products, which already include cold plates.
Only Alloy can produce aluminum cold plates with this degree of geometric intricacy without the need for extra assembly or equipment. Superior material features, such as a high strength-to-weight ratio, excellent thermal conductivity, channel complexity, integrated cooling, and conformal surfaces, are engineered into Alloy's cold plate components.
Alloy's cold plates, which are already available, offer greater functionality and performance along with durability, lack of porosity, and no need for further assembly, or de-powdering. Reduced assembly, fast turnaround revisions, and personalized design are some advantages. When compared to casting, machining, or 3D printing from a U.S.-based supplier, Alloy's unique Sheet Forging process allows clients to launch products faster, iterate designs to enhance performance, and realize cost savings. Heat sinks, casings, housings, and heat exchangers are further thermal management uses.
The US Aluminum Market can be segmented based on product type, end-user industry, and region:
Other Regional Reports of Aluminum Market:
Sl no | Topic |
1 | Market Segmentation |
2 | Scope of the report |
3 | Abbreviations |
4 | Research Methodology |
5 | Executive Summary |
6 | Introduction |
7 | Insights from Industry stakeholders |
8 | Cost breakdown of Product by sub-components and average profit margin |
9 | Disruptive innovation in the Industry |
10 | Technology trends in the Industry |
11 | Consumer trends in the industry |
12 | Recent Production Milestones |
13 | Component Manufacturing in US, EU and China |
14 | COVID-19 impact on overall market |
15 | COVID-19 impact on Production of components |
16 | COVID-19 impact on Point of sale |
17 | Market Segmentation, Dynamics and Forecast by Geography, 2024-2030 |
18 | Market Segmentation, Dynamics and Forecast by Product Type, 2024-2030 |
19 | Market Segmentation, Dynamics and Forecast by Application, 2024-2030 |
20 | Market Segmentation, Dynamics and Forecast by End use, 2024-2030 |
21 | Product installation rate by OEM, 2023 |
22 | Incline/Decline in Average B-2-B selling price in past 5 years |
23 | Competition from substitute products |
24 | Gross margin and average profitability of suppliers |
25 | New product development in past 12 months |
26 | M&A in past 12 months |
27 | Growth strategy of leading players |
28 | Market share of vendors, 2023 |
29 | Company Profiles |
30 | Unmet needs and opportunity for new suppliers |
31 | Conclusion |
32 | Appendix |