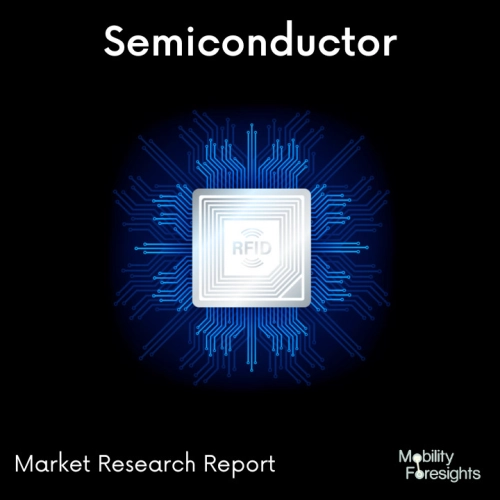
- Get in Touch with Us
Last Updated: Apr 25, 2025 | Study Period: 2023-2030
In the era of smart manufacturing and industrial automation, factory automation sensors have emerged as the critical enablers of efficiency, productivity, and precision. These sensors, often referred to as the "eyes" and "ears" of the production environment, play a pivotal role in capturing real-time data and providing valuable insights for intelligent decision-making and control.
This introduction provides an overview of factory automation sensors, highlighting their essential role, diverse types, and the transformative impact they have on modern industrial processes.
Factory automation sensors are sophisticated devices designed to detect, measure, and monitor a wide range of physical parameters within the manufacturing environment.
They serve as the interface between the physical world and the digital control systems, converting physical quantities such as temperature, pressure, proximity, motion, and more into electrical signals that can be easily processed and utilized for automation and control purposes.
These sensors come in various types, each specifically engineered to fulfill unique monitoring requirements. Proximity sensors, for instance, detect the presence or absence of objects in proximity to the sensor, ensuring precise positioning, object detection, and reliable automation processes. Photoelectric sensors utilize light beams to sense objects, offering versatile and accurate detection capabilities for a wide range of applications.
Pressure sensors are essential for monitoring and controlling the pressure levels of fluids or gasses, ensuring optimal performance and safety of pneumatic and hydraulic systems. Temperature sensors enable the measurement and monitoring of thermal conditions, crucial for maintaining ideal operating temperatures and protecting equipment from overheating or freezing.
Level sensors play a vital role in accurately measuring the levels of liquids or solids in tanks or containers, facilitating efficient inventory management, preventing overflow or depletion, and ensuring consistent production processes.
Flow sensors, on the other hand, provide precise measurement and control of fluid flow rates, enabling accurate dosing, mixing, and distribution of liquids or gasses.
Industrial processes are revolutionized by the integration of factory automation sensors by delivering real-time data and enabling precise control and monitoring. These sensors give companies the ability to increase product quality, decrease waste, improve production efficiency, and employ preventive maintenance techniques to cut down on downtime.
Additionally, by identifying risky situations, maintaining worker safety, and averting accidents, automation sensors help to the overall safety of the production environment.
Finally, factory automation sensors act as the foundation of contemporary industrial automation by supplying vital data and control capabilities that promote productivity, accuracy, and efficiency.
It is possible to customize and adapt them to different industrial applications due to their wide variety of types and features. Factory automation sensors will continue to be crucial in determining the future of industrial automation as manufacturing processes change, enabling wise decision-making and allowing firms to prosper in the era of smart manufacturing.
The US Factory Automation Sensor market accounted for $XX Billion in 2022 and is anticipated to reach $XX Billion by 2030, registering a CAGR of XX% from 2023 to 2030.
Senior executives at Okuma America Corp., a leading manufacturer of computer numeric control (CNC) machine tools, controls, and automation systems, announce the establishment of a new business division to advise, market, and provide support for manufacturing production line systems utilizing Okuma CNC machine tools and integrated automation technologies. The new division is located in Charlotte, North Carolina, at the main office of Okuma America Corp.
In order to solve concerns with labor shortages and boost production capabilities, manufacturers have raised their need for automated machining systems and cells for their operations, prompting Okuma to develop the Factory Automation Division.
Okuma will be in a position to offer customers a wide choice of Okuma machine tool and automation system pairings thanks to the establishment of this new subsidiary.
These will include automated material loading and unloading systems, industrial robotics, automated workpiece pallet changers (APC), flexible manufacturing systems (FMS), smart manufacturing systems, and others. Solutions will also include both proprietary and seamlessly integrated automation systems.
1 | Market Segmentation |
2 | Scope of the report |
3 | Abbreviations |
4 | Research Methodology |
5 | Executive Summary |
6 | Introduction |
7 | Insights from Industry stakeholders |
8 | Cost breakdown of Product by sub-components and average profit margin |
9 | Disruptive innovation in the Industry |
10 | Technology trends in the Industry |
11 | Consumer trends in the industry |
12 | Recent Production Milestones |
13 | Component Manufacturing in US, EU and China |
14 | COVID-19 impact on overall market |
15 | COVID-19 impact on Production of components |
16 | COVID-19 impact on Point of sale |
17 | Market Segmentation, Dynamics and Forecast by Geography, 2023-2030 |
18 | Market Segmentation, Dynamics and Forecast by Product Type, 2023-2030 |
19 | Market Segmentation, Dynamics and Forecast by Application, 2023-2030 |
20 | Market Segmentation, Dynamics and Forecast by End use, 2023-2030 |
21 | Product installation rate by OEM, 2023 |
22 | Incline/Decline in Average B-2-B selling price in past 5 years |
23 | Competition from substitute products |
24 | Gross margin and average profitability of suppliers |
25 | New product development in past 12 months |
26 | M&A in past 12 months |
27 | Growth strategy of leading players |
28 | Market share of vendors, 2023 |
29 | Company Profiles |
30 | Unmet needs and opportunity for new suppliers |
31 | Conclusion |
32 | Appendix |