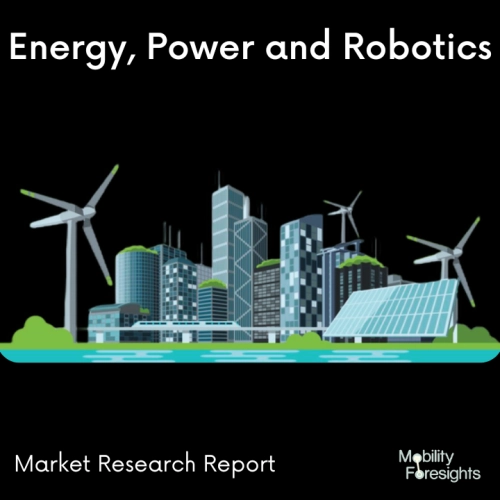
- Get in Touch with Us
Last Updated: Apr 25, 2025 | Study Period: 2023-2030
Electrical shrink tubing, commonly known as heat shrink tubing, is a vital organizational and protective component used in many electrical arrays.In most electrical setups, heat shrink tubing is a standard component that protects electrical components from elements including moisture, dust, abrasion, and sharp objects that could harm cables and other electrical components. Shorts and failures are the end outcome of this kind of damage.
Additionally, it will cinch loose wires, connectors, joints, terminals, and splices into neater, easier-to-manage bundles. Color-coded heat shrink tubing makes it simpler to identify wires and components.
A thermoplastic tube called heat shrink tubing contracts when heated. Heat shrink tubing forms a protective coating around wire arrays and electrical components by collapsing radially to meet the geometry of the apparatus. It can shield against abrasion, low impact, cuts, moisture, dust, and sections of individual wires or full arrays.
Plastic producers first extrude a thermoplastic material tube to create heat shrink tubing. Depending on its intended function, heat shrink tubing can be made of a variety of materials. The material is heated and made to expand once the desired plastic has been extruded, increasing the tube's diameter.
Allowing the expanded tube to cool to ambient temperature before setting.The wires or other needed components are then positioned inside this inflated thermoplastic tube, which has been heated to a precise temperature.
The wires or other components are successfully enclosed in a tight layer of protective plastic when the tube softens and shrinks back to its original extruded size as a result of the heat.
The US Heat shrink tubing market accounted for $XX Billion in 2022 and is anticipated to reach $XX Billion by 2030, registering a CAGR of XX% from 2023 to 2030.
TheUS Heat shrink tubing market is driven by the growing ability of power generation worldwide. But a practical method to boost transmission capacity is to upgrade the transmission lines and substations along the existing corridors.
Transmission capacity can be increased by reconducting existing lines (using components like composite conductors that can carry larger currents). Despite being currently available, these materials are not commonly employed because it is challenging to reconduct fresh materials when lines are in use.
Additionally, all overhead lines may carry current greater than their nominal rating when the weather is good, and a real-time rating that could be regularly modified would boost the capacity that is available.
1 | Market Segmentation |
2 | Scope of the report |
3 | Abbreviations |
4 | Research Methodology |
5 | Executive Summary |
6 | Introduction |
7 | Insights from Industry stakeholders |
8 | Cost breakdown of Product by sub-components and average profit margin |
9 | Disruptive innovation in the Industry |
10 | Technology trends in the Industry |
11 | Consumer trends in the industry |
12 | Recent Production Milestones |
13 | Component Manufacturing in US, EU and China |
14 | COVID-19 impact on overall market |
15 | COVID-19 impact on Production of components |
16 | COVID-19 impact on Point of sale |
17 | Market Segmentation, Dynamics and Forecast by Geography, 2023-2030 |
18 | Market Segmentation, Dynamics and Forecast by Product Type, 2023-2030 |
19 | Market Segmentation, Dynamics and Forecast by Application, 2023-2030 |
20 | Market Segmentation, Dynamics and Forecast by End use, 2023-2030 |
21 | Product installation rate by OEM, 2023 |
22 | Incline/Decline in Average B-2-B selling price in past 5 years |
23 | Competition from substitute products |
24 | Gross margin and average profitability of suppliers |
25 | New product development in past 12 months |
26 | M&A in past 12 months |
27 | Growth strategy of leading players |
28 | Market share of vendors, 2023 |
29 | Company Profiles |
30 | Unmet needs and opportunity for new suppliers |
31 | Conclusion |
32 | Appendix |