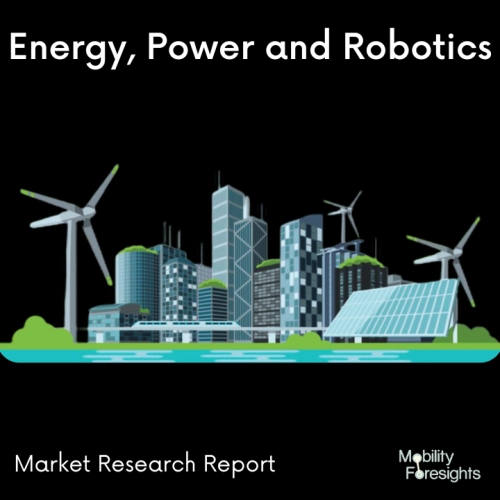
- Get in Touch with Us
Last Updated: Apr 25, 2025 | Study Period: 2023-2030
A factory robot system is referred to as an industrial robot. Industrial robots have three or more axes of motion, are automated, and may be programmed. Robots are typically used for tasks including welding, painting, assembling, disassembly, pick-and-place operations for printed circuit boards, packaging and labelling, palletizing, product inspection, and testing.
All of these tasks are completed by robots with high levels of endurance, speed, and accuracy. They can help with handling materials. An industrial robot is one that has been created to automate labour-intensive manufacturing operations, as those needed by an assembly line that is continually in motion.
They are positioned in fixed locations across an industrial facility as massive, heavy robots, and all other worker duties and operations revolve around them.The International Federations of Robots lists SCARA, Articulated, Cartesian, Delta, and Polar as the top five categories of industrial robots.
An autonomous system of sensors, controllers, and actuators mounted on an articulated frame, known as an industrial robot, performs particular tasks and operations in a production or processing line. They run continually, following a set of directives known as a programme, which directs them to perform cycles of repetitive movement.
Any invention that may be manufactured or employed in any industry, including agriculture, is deemed to be capable of industrial application. A patent is only valid for an innovation if it has industrial application, among other requirements.
The US Industrial robots market accounted for $XX Billion in 2022 and is anticipated to reach $XX Billion by 2030, registering a CAGR of XX% from 2023 to 2030.
The new M-1000iA robot from FANUC US, a market leader in CNCs, robotics and ROBOT MACHINES, can handle highly heavy objects like automobile components, building supplies and battery packs for electric vehicles.
The serial-link design of the M-1000iA allows the robot a greater range of mobility in every direction. For typical heavy-payload robots with a parallel-link system, it is not possible to extend the arm upright or rotate it backwards.
The M-1000iA is equipped with a 1000 kg payload, a 3,253 mm horizontal reach, and a 4,297 mm vertical reach, making it ready to work for enterprises looking to boost productivity and maximise the efficiency of their production lines. According to FANUC General Industries and Automotive Segment, "The new M-1000iA is FANUC's largest serial-link robot to date.
This robot is a great solution for a variety of applications such as drilling and handling large automotive components, processing and handling battery packs for electric vehicles, fabrication and handling of construction materials, and much more. Customers who process very heavy parts need more versatility in the workspace.
Sl no | Topic |
1 | Market Segmentation |
2 | Scope of the report |
3 | Abbreviations |
4 | Research Methodology |
5 | Executive Summary |
6 | Introduction |
7 | Insights from Industry stakeholders |
8 | Cost breakdown of Product by sub-components and average profit margin |
9 | Disruptive innovation in the Industry |
10 | Technology trends in the Industry |
11 | Consumer trends in the industry |
12 | Recent Production Milestones |
13 | Component Manufacturing in US, EU and China |
14 | COVID-19 impact on overall market |
15 | COVID-19 impact on Production of components |
16 | COVID-19 impact on Point of sale |
17 | Market Segmentation, Dynamics and Forecast by Geography, 2023-2030 |
18 | Market Segmentation, Dynamics and Forecast by Product Type, 2023-2030 |
19 | Market Segmentation, Dynamics and Forecast by Application, 2023-2030 |
20 | Market Segmentation, Dynamics and Forecast by End use, 2023-2030 |
21 | Product installation rate by OEM, 2023 |
22 | Incline/Decline in Average B-2-B selling price in past 5 years |
23 | Competition from substitute products |
24 | Gross margin and average profitability of suppliers |
25 | New product development in past 12 months |
26 | M&A in past 12 months |
27 | Growth strategy of leading players |
28 | Market share of vendors, 2023 |
29 | Company Profiles |
30 | Unmet needs and opportunity for new suppliers |
31 | Conclusion |
32 | Appendix |