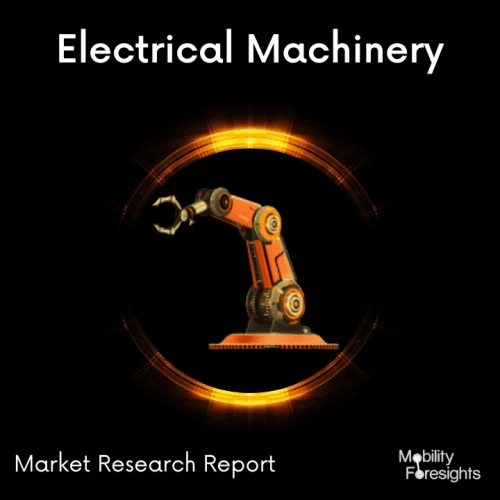
- Get in Touch with Us
Last Updated: Apr 25, 2025 | Study Period:
The US industrial valves market continues to experience steady growth, fueled by a surge in demand from critical industries such as oil & gas, water treatment, and chemical processing. As industries evolve, thereâs an increasing shift toward automation and smart valves, which are becoming pivotal for achieving operational efficiency and regulatory compliance. In particular, environmental regulations and safety standards are pushing companies to adopt advanced valve technologies that ensure reliability and reduce emissions.
Technological innovations, especially the integration of IoT and predictive maintenance, are revolutionizing the industrial valves market. This shift is enabling industries to monitor real-time valve performance, detect failures before they occur, and ultimately reduce downtime. However, the market is also facing certain challenges, including raw material price volatility and supply chain disruptions caused by global uncertainties. These factors have affected production timelines and pricing competitiveness, especially against international competitors from low-cost regions.
The US industrial valves market plays a critical role in controlling the flow and pressure within pipelines across various industries, including oil & gas, chemicals, water management, and energy. Industrial valves are essential components that ensure safe and efficient operations by controlling the flow of gases, liquids, and slurries.
Industrial valves come in a wide range of types, including gate valves, ball valves, butterfly valves, globe valves, and check valves. Each type serves specific functions, such as isolation, regulation, and pressure control, depending on the industry and the application.
The applications of industrial valves span across various sectors such as oil & gas, water & wastewater treatment, chemical processing, power generation, and manufacturing. In oil & gas, for instance, valves play a crucial role in controlling high-pressure flow, while in water treatment, they help manage fluid handling and prevent leaks.
However, there are both benefits and challenges associated with the adoption of industrial valves. Benefits include enhanced operational control, safety, and efficiency. On the downside, challenges such as high installation costs and maintenance complexities can hinder market growth, particularly for smaller operators.
The US industrial valves market is currently valued at approximately $8.5 billion in 2023 and is forecasted to grow to $12.5 billion by 2030, with a CAGR of 4.8%. Growth is driven by increased infrastructure spending, demand from energy industries, and a shift toward smart and automated valves. In particular, environmental and safety regulations are pushing industries to adopt advanced valve technologies that reduce emissions and improve operational safety.
One of the most significant trends is the rise of smart valves that utilize sensors and IoT technology to enable real-time monitoring and predictive maintenance. Companies are investing heavily in this technology to prevent valve failures and reduce downtime, which is particularly important in industries such as oil & gas and water management.
Another emerging trend is the shift toward energy-efficient valves. With sustainability becoming a key focus, manufacturers are developing valves that help industries reduce energy consumption and minimize their environmental footprint.
Additionally, the adoption of electric actuators in industrial valves is growing, as they offer superior control and precision over traditional pneumatic actuators. These actuators are increasingly being deployed in industries requiring high levels of accuracy, such as pharmaceuticals and chemical processing.
By Type:
By Application:
By Actuation Technology:
By Material:
Sr. No. | Title |
1 | Introduction to US Industrial Valves Market |
2 | Market Segmentation |
3 | Scope of the Report |
4 | Research Methodology |
5 | Executive Summary |
6 | Key Findings |
7 | US Industrial Valves Market Production Footprint - 2023 |
8 | Technological Developments in Industrial Valves |
9 | New Product Development in US Industrial Valves Market |
10 | Major Projects Utilizing Industrial Valves |
11 | Market Size, Dynamics, and Forecast, by Geography (2024-2030) |
12 | Market Size, Dynamics, and Forecast, by Product Type (2024-2030) |
13 | Market Size, Dynamics, and Forecast, by Application (2024-2030) |
14 | Market Size, Dynamics, and Forecast, by Distribution Channel (2024-2030) |
15 | Competitive Landscape |
16 | Leading Players |
17 | Unmet Needs and Opportunities in the US Industrial Valves Market |
18 | Supply Chain and Raw Material Analysis |
19 | Impact of Environmental Regulations |
20 | Conclusion |