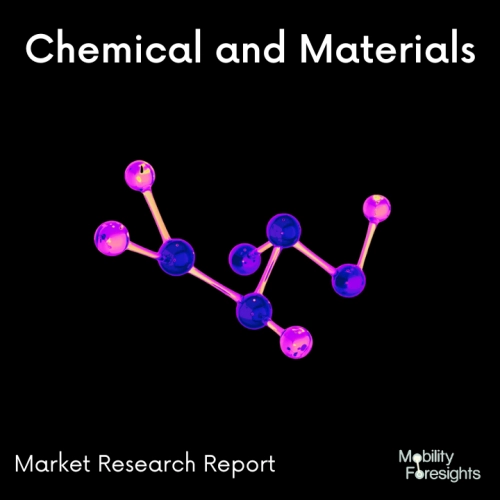
- Get in Touch with Us
Last Updated: Apr 25, 2025 | Study Period: 2024-2030
A thermoplastic sheet material is heated until it becomes malleable and is then sucked onto a core or tool using vacuum pressure. This method is known as vacuum molding.
Pharmaceuticals are dried, degassed, sterilized, cooled, distilled, and crystallized in vacuum chambers in the biopharmaceutical sector. They also help with the development of novel medications and specimen preservation so that they can be studied in a clean environment.
The process of vacuum forming involves heating a plastic sheet until it becomes malleable, stretching it onto a mold, and then applying vacuum pressure to the component to create the required part geometry.
Vacuum forming, the most basic type of plastic thermoforming, uses aluminum tooling that is temperature-controlled together with hardwood templates, epoxy tools, and other materials.
The Global Vacuum Chamber Injection Molding Machine Market accounted for $XX Billion in 2023 and is anticipated to reach $XX Billion by 2030, registering a CAGR of XX% from 2024 to 2030.
The "SE400HS-CI" is a newly released double-shot injection molding machine. All-electric double-shot injection molding machine SE400HS-CI goes on sale from Sumitomo Heavy Industries, Ltd.
There has been an increase in demand for two-material molding in recent years due to labor savings in the manufacturing process, functional improvements such improved design and sealing capabilities, and texture improvement.
Due to the increased functionality and added value of molded parts, particularly in the automotive industry, molds are getting bigger.
Two-material molding with a big rotary table is becoming more and more popular. The CI series of all-electric double-shot injection molding machines, with clamping forces ranging from 290 kN to 2740 kN, will have its product selection expanded to 4000 kN to fulfil these demands.
increasing efficiency High-speed rotary units can reduce cycle times. Moreover, a Direct Drive injection unit allows for highly accurate and quick-response screw control, which significantly enhances molding stability.
Increasing productivity at work It has a special cable Veyo for temperature control pipework that reduces setup time, speeds up cycle time, and increases the adaptability of mold designs. The 90-degree table stop also offers safety and ease of use, which reduces setup time.
Sl no | Topic |
1 | Market Segmentation |
2 | Scope of the report |
3 | Abbreviations |
4 | Research Methodology |
5 | Executive Summary |
6 | Introduction |
7 | Insights from Industry stakeholders |
8 | Cost breakdown of Product by sub-components and average profit margin |
9 | Disruptive innovation in the Industry |
10 | Technology trends in the Industry |
11 | Consumer trends in the industry |
12 | Recent Production Milestones |
13 | Component Manufacturing in US, EU and China |
14 | COVID-19 impact on overall market |
15 | COVID-19 impact on Production of components |
16 | COVID-19 impact on Point of sale |
17 | Market Segmentation, Dynamics and Forecast by Geography, 2024-2030 |
18 | Market Segmentation, Dynamics and Forecast by Product Type, 2024-2030 |
19 | Market Segmentation, Dynamics and Forecast by Application, 2024-2030 |
20 | Market Segmentation, Dynamics and Forecast by End use, 2024-2030 |
21 | Product installation rate by OEM, 2023 |
22 | Incline/Decline in Average B-2-B selling price in past 5 years |
23 | Competition from substitute products |
24 | Gross margin and average profitability of suppliers |
25 | New product development in past 12 months |
26 | M&A in past 12 months |
27 | Growth strategy of leading players |
28 | Market share of vendors, 2023 |
29 | Company Profiles |
30 | Unmet needs and opportunity for new suppliers |
31 | Conclusion |
32 | Appendix |