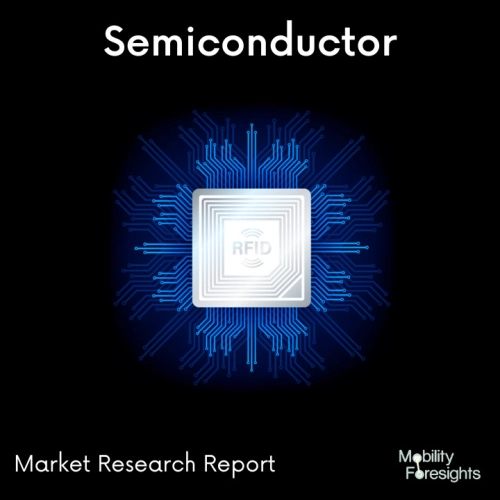
- Get in Touch with Us
Last Updated: Apr 25, 2025 | Study Period:
A transducer that measures changes in magnetic reluctance is known as a variable reluctance sensor (also known as a VR sensor). The sensor detects changes in the presence or proximity of ferrous objects when used in conjunction with fundamental electronic circuitry.
A VR sensor can additionally offer measurements of linear velocity, angular velocity, position, and torque using more sophisticated electronics, software, and specialised mechanical hardware.
A VR sensor can be used to locate a mechanical link in a piece of industrial machinery by acting as a straightforward proximity sensor.
The Global Variable reluctance sensor market accounted for $XX Billion in 2022 and is anticipated to reach $XX Billion by 2030, registering a CAGR of XX% from 2024 to 2030.
Variable reluctance sensors were developed by Harco Laboratories as magnetic and electrical models, and these models have demonstrated high agreement with data gathered from experimental sensors.
The electrical model can be used to alter the output to ensure noiseless and seamless interaction with zero-cross detection and accompanying signal conditioning circuitry, while the magnetic model can be utilised primarily to represent the transient electromagnetic response of the sensor.
The ferromagnetic material used in this model is a toothed gear made of stainless steel that is 430F solenoid grade.
A finite element analytical model that was created specifically for this sensor's magnetic simulation allowed us to mimic the magnetic fields that were present around the sensor while rotating the test gear in discrete angular rotational increments.
The ferromagnetic pole piece and permanent magnet that make up the variable reluctance sensor are encased in a wire coil.
In response to the passage of a ferromagnetic material by the pole piece's tip, the sensor outputs an analog voltage signal.
An effective analytical design tool would make it possible to anticipate output voltages and transient waveform shapes as a function of physical characteristics such as, but not limited to, sensor component sizes and materials, gear geometry, tooth spacing, and gear material.
The performance and cost of current products might be optimised, and new products and systems could be designed with help from the ability to precisely simulate dynamic sensor performance.
Sl no | Topic |
1 | Market Segmentation |
2 | Scope of the report |
3 | Abbreviations |
4 | Research Methodology |
5 | Executive Summary |
6 | Introduction |
7 | Insights from Industry stakeholders |
8 | Cost breakdown of Product by sub-components and average profit margin |
9 | Disruptive innovation in the Industry |
10 | Technology trends in the Industry |
11 | Consumer trends in the industry |
12 | Recent Production Milestones |
13 | Component Manufacturing in US, EU and China |
14 | COVID-19 impact on overall market |
15 | COVID-19 impact on Production of components |
16 | COVID-19 impact on Point of sale |
17 | Market Segmentation, Dynamics and Forecast by Geography, 2024-2030 |
18 | Market Segmentation, Dynamics and Forecast by Product Type, 2024-2030 |
19 | Market Segmentation, Dynamics and Forecast by Application, 2024-2030 |
20 | Market Segmentation, Dynamics and Forecast by End use, 2024-2030 |
21 | Product installation rate by OEM, 2023 |
22 | Incline/Decline in Average B-2-B selling price in past 5 years |
23 | Competition from substitute products |
24 | Gross margin and average profitability of suppliers |
25 | New product development in past 12 months |
26 | M&A in past 12 months |
27 | Growth strategy of leading players |
28 | Market share of vendors, 2023 |
29 | Company Profiles |
30 | Unmet needs and opportunity for new suppliers |
31 | Conclusion |
32 | Appendix |