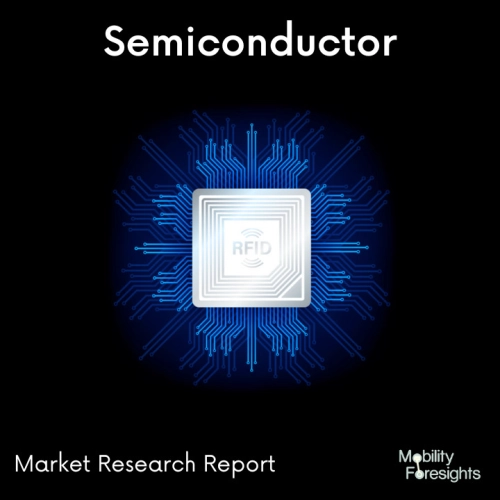
- Get in Touch with Us
Last Updated: Apr 25, 2025 | Study Period: 2024-2030
In the semiconductor industry, a vertical furnaceâalso called a vertical thermal reactor or vertical diffusion furnaceâis a common piece of machinery used for a variety of thermal operations. It is crucial for the creation of silicon-based products like solar cells and integrated circuits (ICs).
The substrates or wafers are inserted vertically into the reaction chamber, giving rise to the moniker "vertical furnace" due to this structure. It comprises of a cylindric quartz or graphite tube surrounded by graphite or molybdenum-based heating components. The chamber is heated consistently throughout by the heating components.
A vertical furnace's main use is to conduct high-temperature operations including chemical vapour deposition (CVD), thermal oxidation, diffusion, and annealing.
Controlling the qualities and features of the thin films and layers that are deposited on semiconductor wafers is essential thanks to these techniques.A thin coating of silicon dioxide (SiO2) is generated on the surface of the silicon wafer during the conventional process of thermal oxidation, which is carried out in a vertical furnace. For the next manufacturing procedures, this layer acts as an insulator or shield.
Another crucial step in the production of semiconductors is diffusion, which involves adding dopant atoms to the silicon wafer to change its electrical characteristics. The dopant source material is heated at a high temperature in a vertical furnace, where the dopant atoms diffuse into the silicon wafer.
TheGlobal Vertical Furnace Marketaccounted for $XX Billion in 2023 and is anticipated to reach $XX Billion by 2030, registering a CAGR of XX% from 2024 to 2030.
Launch of the Sonora vertical boiler system by ASM International N.V. Because the new SONORA® and the old A412TM are completely interoperable, it is simple to transfer current process recipes, expediting system validation and scale up.
Multiple clients worldwide have started receiving systems, including industry leaders in the production of power devices and sophisticated logic.In comparison to its predecessor, productivity has increased because to the bigger process wafer load sizes, upgraded control system, new robots, quicker wafer cooling, and faster boat interchange modules.
Lower energy and chemical use per wafer is another benefit of higher production. A special focus on serviceability in the design resulted in a roomy access for all maintenance tasks.
An elegant graphical user interface, predictive maintenance through enhanced control diagnostics, and other modern features have been added to the new system.
Sl no | Topic |
1 | Market Segmentation |
2 | Scope of the report |
3 | Abbreviations |
4 | Research Methodology |
5 | Executive Summary |
6 | Introduction |
7 | Insights from Industry stakeholders |
8 | Cost breakdown of Product by sub-components and average profit margin |
9 | Disruptive innovation in the Industry |
10 | Technology trends in the Industry |
11 | Consumer trends in the industry |
12 | Recent Production Milestones |
13 | Component Manufacturing in US, EU and China |
14 | COVID-19 impact on overall market |
15 | COVID-19 impact on Production of components |
16 | COVID-19 impact on Point of sale |
17 | Market Segmentation, Dynamics and Forecast by Geography, 2024-2030 |
18 | Market Segmentation, Dynamics and Forecast by Product Type, 2024-2030 |
19 | Market Segmentation, Dynamics and Forecast by Application, 2024-2030 |
20 | Market Segmentation, Dynamics and Forecast by End use, 2024-2030 |
21 | Product installation rate by OEM, 2023 |
22 | Incline/Decline in Average B-2-B selling price in past 5 years |
23 | Competition from substitute products |
24 | Gross margin and average profitability of suppliers |
25 | New product development in past 12 months |
26 | M&A in past 12 months |
27 | Growth strategy of leading players |
28 | Market share of vendors, 2023 |
29 | Company Profiles |
30 | Unmet needs and opportunity for new suppliers |
31 | Conclusion |
32 | Appendix |