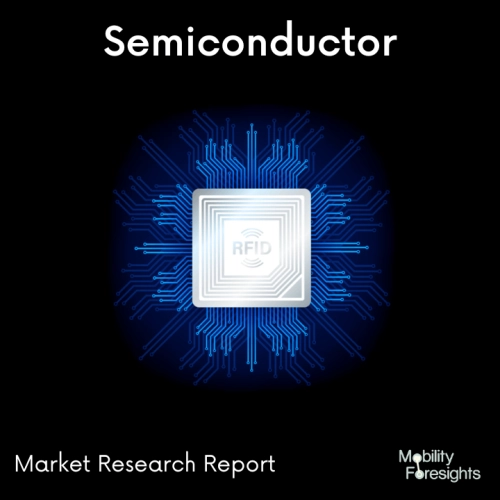
- Get in Touch with Us
Last Updated: Apr 25, 2025 | Study Period: 2024-2030
AC motors are powered by variable frequency drives (VFD), commonly referred to as variable-speed or adjustable-speed drives, in a variety of industrial motion control, commercial flow/pumping, and extrusion applications.
Electric motors receive power from VFDs, which are controllers. They only provide the amount of energy required for the particular application, either more or less. Due to this unpredictability, the electrical environment between the drive and motor is more unstable. VFD cables have a role in this.
The global VFD cable market accounted for $XX Billion in 2023 and is anticipated to reach $XX Billion by 2030, registering a CAGR of XX% from 2024 to 2030.
The new series of flexible Variable Frequency Drive (VFD) cables from Belden Inc. Belden VFD flexible cables come in small, medium, and large gauges to suit the unique accessibility, engine, and transmission requirements of various applications.
However, these flexible VFD cables can be employed in difficult-to-reach spots because of their unique copper conductors, fine wire, and more flexible cable coverings. Along with improved oil resistance and use in cooler temperatures, the new cable cover has other strong qualities.
The high-quality cable line was created with the following goals in mind: Extend the lifespan of the transmission system by tolerating high voltage spikes; and Prevent damage to the cable, motors, bearings, gearboxes, and other equipment.Improved coating can lower excessive noise levels in VFD cabling.
VFD flexible cables offer reliability for industrial applications, whether in hazardous locations on a factory floor or in severe outdoor situations. They safeguard against extreme circumstances in the machine building, automotive, petroleum, food and beverage, and water and wastewater industries.
Visibility is crucial for operators confronting rising demands for data receiving, analysis, and sharing in a world that is heading toward interoperability. The industrial connectivity solutions from Belden provide answers that account for these needs.
A cutting-edge new cabling option for VFDs in deep-well and other water system applications, LUTZE is launching DRIVEFLEX HYDRO VFD cables. LUTZE is dedicated to offering its experience in VFD cabling and installation to the pumping industry to address typical cable and motor issues as pumping applications increasingly turn to VFDs as a way to increase efficiency.
For improved water ingress protection, LUTZE DRIVEFLEX HYDRO cables combine the tried-and-true XLPE insulation with a cutting-edge water-blocking separation film. When put in moist and submerged conditions, the tape lessens the chance of water transmission and wicking through the cable.
Unshielded DRIVEFLEX HYDRO VFD cables are currently offered from 14AWG to 2AWG and have a lower capacitance. Future additions will include larger gauge sizes.
LUTZE Inc. has introduced a brand-new product to its extensive line of VFD and motor supply cables. In comparison to power tray cables with PVC/nylon insulation, the new Silflex M VFD cable has thermoset XLPE insulation type XHHW-2 for increased safety and greater electrical performance in any VFD application.
Shielded LUTZE Silflex M VFD XLPE cable with a flexible, simple-to-strip PVC jacket. According to Oil Res I and II requirements, the cable has successfully passed testing. Both the traditional four conductor design (A106 series) and the shielded control pair servo design (A107 series) are readily accessible.
The Trex-Onics VFD cables are made especially for motor applications, with a composite insulation system made to withstand corona discharge build-up, which is frequent in VFD applications and a specially compounded TPE jacket that offers excellent protection from oil, ozone, abrasion, chemicals, and UV exposure.
It is possible to avoid harming expensive motors and controllers by using a Trex-Onics VFD cable that is correctly grounded.
Sl no | Topic |
1 | Market Segmentation |
2 | Scope of the report |
3 | Abbreviations |
4 | Research Methodology |
5 | Executive Summary |
6 | Introduction |
7 | Insights from Industry stakeholders |
8 | Cost breakdown of Product by sub-components and average profit margin |
9 | Disruptive innovation in the Industry |
10 | Technology trends in the Industry |
11 | Consumer trends in the industry |
12 | Recent Production Milestones |
13 | Component Manufacturing in US, EU and China |
14 | COVID-19 impact on overall market |
15 | COVID-19 impact on Production of components |
16 | COVID-19 impact on Point of sale |
17 | Market Segmentation, Dynamics and Forecast by Geography, 2024-2030 |
18 | Market Segmentation, Dynamics and Forecast by Product Type, 2024-2030 |
19 | Market Segmentation, Dynamics and Forecast by Application, 2024-2030 |
20 | Market Segmentation, Dynamics and Forecast by End use, 2024-2030 |
21 | Product installation rate by OEM, 2023 |
22 | Incline/Decline in Average B-2-B selling price in past 5 years |
23 | Competition from substitute products |
24 | Gross margin and average profitability of suppliers |
25 | New product development in past 12 months |
26 | M&A in past 12 months |
27 | Growth strategy of leading players |
28 | Market share of vendors, 2023 |
29 | Company Profiles |
30 | Unmet needs and opportunity for new suppliers |
31 | Conclusion |
32 | Appendix |