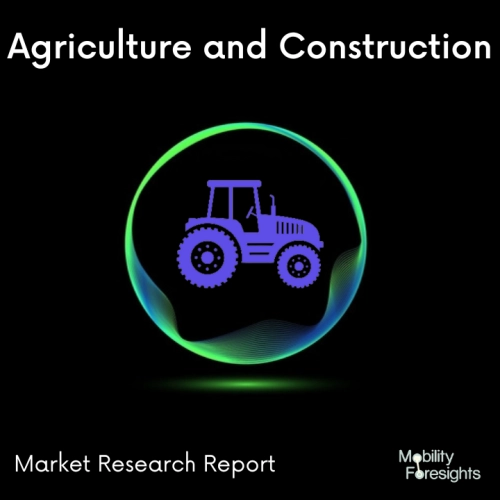
- Get in Touch with Us
Last Updated: Apr 25, 2025 | Study Period: 2023-2030
A vibratory roller is a tool used in construction and road building to crush or compress materials like soil, gravel, or asphalt. It is also known as a vibratory compactor or vibrating soil compactor. The device has a sizable vibrating drum that generates the pressure required to condense the material.
A soil compactor is a device or mechanism used to compact material to reduce its size, such as garbage or biomass. When building an embankment, road, sub-grades, earth dam, etc., compaction is required to enhance the soil's qualities, such as density, water content, or gradation.
The Global Vibratory Soil Compactor market accounted for $XX Billion in 2022 and is anticipated to reach $XX Billion by 2030, registering a CAGR of XX% from 2023 to 2030.
CASE introduces two new vibratory rollers to its E-Series.The single-drum vibratory rollers SV215E and SV217E are offered by CASE Construction Equipment. These new versions are designed to provide efficient and reliable soil compaction for a range of lift heights and material kinds.
The business claims that by designing strong centrifugal forces and conventional dual amplitude and dual frequency capabilities, it was able to attain this speed and consistency.
Both rollers have 154 horsepower and can generate centrifugal forces of up to 73,063 and 74,861 pounds. They weigh 33,420 and 36,500 pounds, respectively. Additionally, each model works with ACEforce intelligent compaction technology, which calculates the absolute value of the material's bearing capacity.
The CASE E-Series compactors have an axle-free design and a low centre of gravity. The axle-free design uses an electronic, self-adjusting torque-control system to deliver steady power to the wheels and drum. Additionally, a HX drive propulsion system with automated traction control adds to the steadiness.
While standard on models with padfoots, this function is an option for smooth drums. Overall, based on CASE, this produces good performance on grades up to 67 percent and outstanding stability.
An oscillating, articulated roller-joint provides continuous drum-to-ground contact, while drum design improvements aid in reducing drift and promoting steady compaction during rotations.
Standard dual-frequency and amplitudes, as well as standard auto vibration control, allow the operator to tailor compaction performance to the kind of material and depth of lift. This allows operators to achieve optimum compaction in fewer passes, increasing output and decreasing machine strain.
Sl no | Topic |
1 | Market Segmentation |
2 | Scope of the report |
3 | Abbreviations |
4 | Research Methodology |
5 | Executive Summary |
6 | Introduction |
7 | Insights from Industry stakeholders |
8 | Cost breakdown of Product by sub-components and average profit margin |
9 | Disruptive innovation in the Industry |
10 | Technology trends in the Industry |
11 | Consumer trends in the industry |
12 | Recent Production Milestones |
13 | Component Manufacturing in US, EU and China |
14 | COVID-19 impact on overall market |
15 | COVID-19 impact on Production of components |
16 | COVID-19 impact on Point of sale |
17 | Market Segmentation, Dynamics and Forecast by Geography, 2022-2030 |
18 | Market Segmentation, Dynamics and Forecast by Product Type, 2022-2030 |
19 | Market Segmentation, Dynamics and Forecast by Application, 2022-2030 |
20 | Market Segmentation, Dynamics and Forecast by End use, 2022-2030 |
21 | Product installation rate by OEM, 2022 |
22 | Incline/Decline in Average B-2-B selling price in past 5 years |
23 | Competition from substitute products |
24 | Gross margin and average profitability of suppliers |
25 | New product development in past 12 months |
26 | M&A in past 12 months |
27 | Growth strategy of leading players |
28 | Market share of vendors, 2022 |
29 | Company Profiles |
30 | Unmet needs and opportunity for new suppliers |
31 | Conclusion |
32 | Appendix |