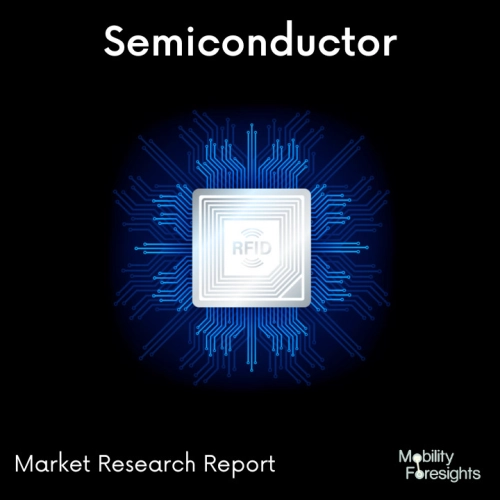
- Get in Touch with Us
Last Updated: Apr 25, 2025 | Study Period: 2024-2030
In order to give an accurate real-time assessment of the oil state, the VISCOSITY SENSOR enables continuous monitoring of the viscosity, relative dielectric number, and temperature of lubricating and hydraulic oils.
The only moving component in sensors is a piston that is electromagnetically propelled through fluid in a tiny measurement chamber. Two coils propel the piston back and forth when fluid is present in the measurement chamber with a constant force. Absolute viscosity is calculated by analysing the two-way travel time using specialised electronics.
SAW-dynamic viscosity, relative dielectric number, and temperature are the pertinent parameters that are measured and shown on the dedicated display device DATALOGGER in real-time mode. Following the completion of the VISCOSITY SENSOR's learning phase, the obtained data and the oil properties at the present temperature are both available at a reference temperature of 40 °C.
Global viscosity sensor market accounted for $XX Billion in 2023 and is anticipated to reach $XX Billion by 2030, registering a CAGR of XX% from 2024 to 2030.
The next generation of process viscosity sensors are proudly offered by Marimex Industries Corp. These new sensor improvements are the result of lessons learned through many years of sensor design and production: The ViscoMeter VP-1000 is made with OEM process applications in mind.
With process pressures up to 10 bar/150 psi and process temperatures up to 130oC, the series VP-1000 can measure low or high viscosities. The ViscoMeter VP-3000 sensor can be customised for use in almost any process application.
It can measure viscosities ranging from low to high, and the sensors can be made to withstand pressures of up to 500 bar (7,250 psi) and temperatures of up to 450oC.The non-active extension can now be made into any length and shape by Marimex Industries Corp. thanks to an inventive architecture. This makes it simple to modify the sensor to fit certain applications and installation needs.
It is possible to utilise the sensor in high process temperatures since the neck can be any length. Making ensuring the sensor itself is maintained at the correct process temperature eliminates the need for air cooling of the sensor enclosure. These new sensors' numerous characteristics provide them more flexibility and make them simpler to use during installation, startup, and operation. Future changes will be simple thanks to their design.
Sl no | Topic |
1 | Market Segmentation |
2 | Scope of the report |
3 | Abbreviations |
4 | Research Methodology |
5 | Executive Summary |
6 | Introduction |
7 | Insights from Industry stakeholders |
8 | Cost breakdown of Product by sub-components and average profit margin |
9 | Disruptive innovation in the Industry |
10 | Technology trends in the Industry |
11 | Consumer trends in the industry |
12 | Recent Production Milestones |
13 | Component Manufacturing in US, EU and China |
14 | COVID-19 impact on overall market |
15 | COVID-19 impact on Production of components |
16 | COVID-19 impact on Point of sale |
17 | Market Segmentation, Dynamics and Forecast by Geography, 2024-2030 |
18 | Market Segmentation, Dynamics and Forecast by Product Type, 2024-2030 |
19 | Market Segmentation, Dynamics and Forecast by Application, 2024-2030 |
20 | Market Segmentation, Dynamics and Forecast by End use, 2024-2030 |
21 | Product installation rate by OEM, 2023 |
22 | Incline/Decline in Average B-2-B selling price in past 5 years |
23 | Competition from substitute products |
24 | Gross margin and average profitability of suppliers |
25 | New product development in past 12 months |
26 | M&A in past 12 months |
27 | Growth strategy of leading players |
28 | Market share of vendors, 2023 |
29 | Company Profiles |
30 | Unmet needs and opportunity for new suppliers |
31 | Conclusion |
32 | Appendix |