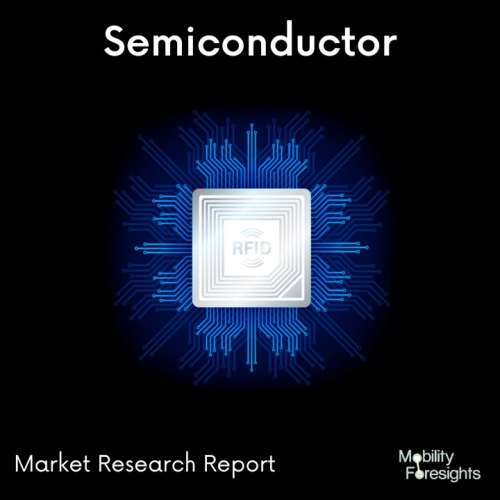
- Get in Touch with Us
Last Updated: Apr 25, 2025 | Study Period: 2024-2030
Visibility sensor sensors provide information on the fog and snow meteorological observable range (MOR). Visibility sensors are frequently employed in applications for the road, sea, air, and wind energy. Visibility is determined by the sensor system, which consists of a transmitter, receiver, and CPU. Twice per second, the transmitter emits a cone of light.
The light then disperses among the airborne particles. The processor uses pre-existing formulae to calculate the visibility once the receiver detects how much light has been scattered. An average visibility for one minute is calculated by the processor.
The maximum distance that the human eye can see under specific atmospheric conditions is represented by the sensor equivalent visibility (SEV) range that visibility sensors produce when they detect atmospheric transparency. When visibility is reduced by fog, cloud cover, snow, smoke, or other factors, they provide a standardised approach for determining.
A conventional visibility range of 30 metres to 16 kilometres is obtained by the visibility sensor, which is designed to measure atmospheric visibility. This is done by estimating the quantity of light that is scattered by airborne particles (dust, smoke, fog, haze, as well as rain and snow).
One of the most noteworthy current trends in sensor technology is the development of visibility sensors.
In the automotive industry, visibility sensors are used to ensure the safety of vehicles and drivers. By monitoring the surrounding environment, visibility sensors can detect the presence of fog, smoke, or dust, and alert the driver to take appropriate action. This could include slowing down, turning on headlights, or pulling over until conditions improve. Visibility sensors can also be used to monitor roads and highways for hazards that are not visible to the naked eye, such as icy patches or potholes.
Other applications for visibility sensors include industrial settings, where they can be used to monitor hazardous areas or alert workers to the presence of dangerous gases or particles. In medical settings, visibility sensors can be used to monitor air quality in rooms and help maintain safe levels for patients and staff.
In the home, visibility sensors are becoming increasingly popular, with a number of products now available that can detect the presence of smoke, carbon monoxide, and other potential hazards. These sensors can be used to alert homeowners to the presence of these hazards and take appropriate action.
S.NO | Overview of Development | Details of Development |
1. | Vaisala Introduces Innovative New Visibility and Present Weather Sensors | The seventh generation of visibility and current weather sensors was launched by Vaisala, a global pioneer in environmental and industrial measurements. Vaisala Forward Scatter FD70 Series uses cutting-edge technology to raise the bar for the precision of visibility determination and quantification of precipitation. |
2. | Biral launches new visibility sensor for roadside weather monitoring systems | The new instrument from UK-based Biral (Bristol Industrial & Research Associates Ltd), which produces high-quality meteorological sensors for professional markets and has been developed for use in road applications to deliver accurate visibility measurement data, is intended for use in these applications. |
The FD71 visibility sensor and the FD71P present weather sensor are the two product models that make up the Vaisala Forward Scatter FD70 Series. The FD70 Series can run independently, interact as a vital component of Vaisala systems, and also cooperate with various third-party systems.
The new products' primary clients are airports and meteorological organizations. Deliveries are anticipated to begin.The forward scatter and optical disdrometer technologies are creatively combined in the FD70 Series, making it possible to reliably detect even the smallest droplet.
The FD70 Series improves measurements of precipitation intensity and accumulation while having a superior ability to identify the kind of precipitation. The new products offer precise visibility measurement, calibration traceability that has been established, and reporting ranges up to 100 kilometers.
Biral visibility sensors to be used at Dutch offshore wind farm. One of the world's largest offshore wind farms, Hollandse Kust Zuid, in the Netherlands, will deploy 140 of Biral's SWS-050 visibility sensors. Biral is a specialist in meteorological equipment.
The sensor was designed to be simple to integrate with any RWIS (Road Weather Information System). The RWS-20 is based on the tried-and-true SWS line of visibility sensors, sharing many of its cutting-edge technical capabilities, and was created specifically for the challenging roadside environment.
In order to ensure that local light sources, such as headlights or flashing signs, do not affect its operation or dependability, the new design is a tiny unit that uses the forward scatter measuring concept and stays accurate in all weather circumstances.
The RWS-20 is designed for use in road applications where hazardous driving conditions can be caused by fog, rain, spray, and snow. Its measuring range is 33 feet (10 meters) to 4.6 miles (7.5 kilometers). Heating is built into the optical windows and sensor hoods for usage all year long in inclement weather.
Systems for lens contamination monitoring are present in both optical windows, guaranteeing that the output of visibility is continuously corrected to maintain accuracy and minimizing the need for routine maintenance.
For the purpose of identifying technology developer Orga, the sensors will be utilized to regulate the aviation obstacle lights on top of the turbines.
As part of the project, Siemens Gamesa will attach a SWS-050 sensor to each of the chosen wind turbines, which will have a minimum capacity of 6MW and a maximum height of 251m above sea level. Total wind turbine capacity for the Hollandse Kust Zuid project is 252.
Global visibility sensor market accounted for $XX Billion in 2023 and is anticipated to reach $XX Billion by 2030, registering a CAGR of XX% from 2024 to 2030.
Starting in the middle of May, the VS20-UMB optical sensor will be replaced by the new VS2k-UMB visibility sensor. The first in a long line of products in this category is the Lufft-UMB VS2k. The MARWIS mobile road sensor, a prize-winning Lufft sensor, is receiving a helpful update.
From this point forward, the sensor's second generation will take the place of the first.The new VS2k-UMB visibility sensor is best adapted to its surroundings.
Another optical sensor being sold right now is Lufft's visibility sensor VS2k-UMB. It is used as equipment for road weather stations and traffic control systems in the transportation industry. In a range of up to 2,000 metres, the sensor records precise visibility readings.
The VS20-UMB model, which has been in use globally for ten years, is replaced by the VS2k-UMB model. The VS2k-UMB visibility sensor has improved product attributes as a result of extensive development work, including a highly optimised housing alloy that is seawater resistant and thus appropriate for offshore application.
The sensor demonstrated steady longevity even in the most harsh situations during a number of saltwater tests.
The new VS2k-UMB visibility sensor is the first of a whole series that the sensor firm is now launching. By the middle of the year, a different device version with a 25-kilometer maximum range will be accessible.
Sl no | Topic |
1 | Market Segmentation |
2 | Scope of the report |
3 | Abbreviations |
4 | Research Methodology |
5 | Executive Summary |
6 | Introduction |
7 | Insights from Industry stakeholders |
8 | Cost breakdown of Product by sub-components and average profit margin |
9 | Disruptive innovation in the Industry |
10 | Technology trends in the Industry |
11 | Consumer trends in the industry |
12 | Recent Production Milestones |
13 | Component Manufacturing in US, EU and China |
14 | COVID-19 impact on overall market |
15 | COVID-19 impact on Production of components |
16 | COVID-19 impact on Point of sale |
17 | Market Segmentation, Dynamics and Forecast by Geography, 2024-2030 |
18 | Market Segmentation, Dynamics and Forecast by Product Type, 2024-2030 |
19 | Market Segmentation, Dynamics and Forecast by Application, 2024-2030 |
20 | Market Segmentation, Dynamics and Forecast by End use, 2024-2030 |
21 | Product installation rate by OEM, 2023 |
22 | Incline/Decline in Average B-2-B selling price in past 5 years |
23 | Competition from substitute products |
24 | Gross margin and average profitability of suppliers |
25 | New product development in past 12 months |
26 | M&A in past 12 months |
27 | Growth strategy of leading players |
28 | Market share of vendors, 2023 |
29 | Company Profiles |
30 | Unmet needs and opportunity for new suppliers |
31 | Conclusion |
32 | Appendix |