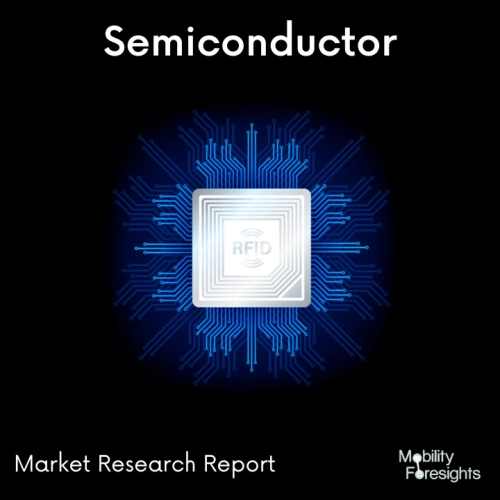
- Get in Touch with Us
Last Updated: Apr 25, 2025 | Study Period: 2023-2030
In a processing chamber, a silicon wafer or another type of wafer is processed during the creation of a semiconductor device. Layers of diverse materials can be deposited, patterned, and etched across the silicon wafer during various production processes.
Processing, however, may introduce pollutants into the processing environment, which may have a negative impact on the device that results or the quality of the deposited layer(s).
For instance, dust or etched material may come into contact with the surface of the wafer, which could interfere with the photolithography or etching processes as well as the deposition of a layer by generating flaws in the layer.
a wafer support is surrounded by an electrically conductive ring that is roughly in the same plane as the wafer, and the ring divides the chamber into an upper and a lower section.
The ring includes an outer ring portion that is thicker than the inner ledge and is outside the inner ledge as well as the outer circumference of the wafer to allow a pressure balance between the upper and lower portions, as well as a recessed inner ledge that is on the same plane as the wafer and extends underneath the wafer to support the wafer.
The Global Wafer Back-side Cleaning System market accounted for $XX Billion in 2022 and is anticipated to reach $XX Billion by 2030, registering a CAGR of XX% from 2023 to 2030.
The CELLESTA SCD single wafer Back-side cleaning system was launched by Tokyo Electron (TEL). TEL's CELLESTA range of devices are frequently used for cleaning silicon wafers throughout the semiconductor production process.
The soon-to-be-available CELLESTA SCD incorporates a special supercritical drying chamber on the CELLESTA platform, which has been successfully used in mass production. Low surface tension alcohol solutions are typically used in the drying step of wafer cleaning.
However, pattern collapse during the drying process has emerged as one of the main problems as a result of continuing semiconductor scaling and the usage of multi-layer architectures in highly advanced devices.
TEL has created a pattern collapse-free drying technique that employs a supercritical fluid in reaction and has introduced the technology to the market as machinery for mass production.
Sl no | Topic |
1 | Market Segmentation |
2 | Scope of the report |
3 | Abbreviations |
4 | Research Methodology |
5 | Executive Summary |
6 | Introdauction |
7 | Insights from Industry stakeholders |
8 | Cost breakdown of Product by sub-components and average profit margin |
9 | Disruptive innovation in theIndustry |
10 | Technology trends in the Industry |
11 | Consumer trends in the industry |
12 | Recent Production Milestones |
13 | Component Manufacturing in US, EU and China |
14 | COVID-19 impact on overall market |
15 | COVID-19 impact on Production of components |
16 | COVID-19 impact on Point of sale |
17 | Market Segmentation, Dynamics and Forecast by Geography, 2023-2030 |
18 | Market Segmentation, Dynamics and Forecast by Product Type, 2023-2030 |
19 | Market Segmentation, Dynamics and Forecast by Application, 2023-2030 |
20 | Market Segmentation, Dynamics and Forecast by End use, 2023-2030 |
21 | Product installation rate by OEM, 2023 |
22 | Incline/Decline in Average B-2-B selling price in past 5 years |
23 | Competition from substitute products |
24 | Gross margin and average profitability of suppliers |
25 | New product development in past 12 months |
26 | M&A in past 12 months |
27 | Growth strategy of leading players |
28 | Market share of vendors, 2023 |
29 | Company Profiles |
30 | Unmet needs and opportunity for new suppliers |
31 | Conclusion |
32 | Appendix |