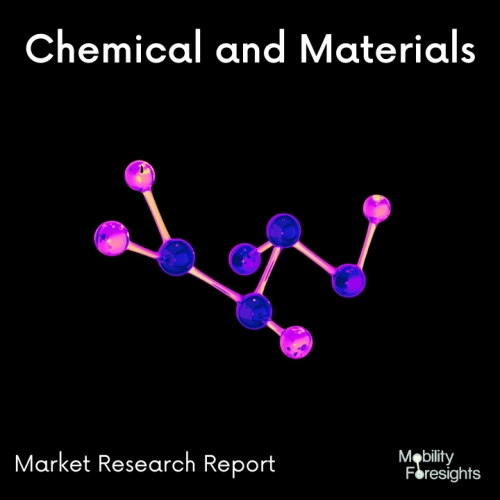
- Get in Touch with Us
Last Updated: Apr 25, 2025 | Study Period: 2024-2030
Wafer cleaning chemicals are substances used in the production of semiconductors to clean the wafer's surface of contaminants. The contaminants may include dust, oils, and other contaminants, as well as leftovers from the production process.
Wafer cleaning agents come in a variety of forms, including: Acids: To eliminate organic and inorganic impurities from the wafer's surface, acids like nitric acid (HNO3), sulfuric acid (H2SO4), and hydrochloric acid (HCl) are frequently utilised.
Bases: To clean the wafer surface of organic impurities and residues, bases like potassium hydroxide (KOH) and ammonium hydroxide (NH4OH) are utilised. Solvents: To clean the wafer surface of organic impurities and residues, solvents like isopropyl alcohol (IPA), acetone, and ethyl alcohol are utilised.
Surfactants: By lowering the surface tension of the cleaning solution and making the removal of pollutants easier, surfactants are used to improve the cleaning process.
To prevent harming the wafer or impairing the semiconductor device's performance, it is crucial to employ the proper wafer cleaning solution for a certain application. Chemicals used to clean wafers must be handled and disposed of carefully to protect the environment and those working in the manufacturing process.
Global Wafer Cleaning Chemicals market accounted for $XX Billion in 2022 and is anticipated to reach $XX Billion by 2030, registering a CAGR of XX% from 2024 to 2030.
The SU-3400 single wafer cleaning system from SCREEN Semiconductor Solutions offers a record-breaking throughput of up to 1,200 wafers per hour.
The Ultra C VI single wafer tool, developed by ACM Research, is intended for high-throughput cleaning of sophisticated 3D NAND devices and dynamic random-access memory (DRAM) devices with 128 stacked layers and above.
For advanced DRAM devices of 1 nm and beyond, as well as for sophisticated 3D NAND devices with 128 stacked layers and higher, the Ultra C VI performs single-wafer cleaning. Depending on the application, it can be used for a range of front-end-of-line (FEOL) and back-end-of-line (BEOL) processes.
When compared to batch cleaning methods, the SU-3400 Single Wafer Cleaning System performs better. Moreover, it has a novel wafer transfer method that significantly raises productivity per unit area.
The new system offers a variety of special cleaning technologies to achieve productivity that leads the world and excellent processing performance. There isn't a clear comparison to other systems on the market, though.
A new single-wafer spin cleaning method that alternately cycles between ozonated and deionized water is mentioned in another source. This method has demonstrated superior results to others.
Sl no | Topic |
1 | Market Segmentation |
2 | Scope of the report |
3 | Abbreviations |
4 | Research Methodology |
5 | Executive Summary |
6 | Introduction |
7 | Insights from Industry stakeholders |
8 | Cost breakdown of Product by sub-components and average profit margin |
9 | Disruptive innovation in the Industry |
10 | Technology trends in the Industry |
11 | Consumer trends in the industry |
12 | Recent Production Milestones |
13 | Component Manufacturing in US, EU and China |
14 | COVID-19 impact on overall market |
15 | COVID-19 impact on Production of components |
16 | COVID-19 impact on Point of sale |
17 | Market Segmentation, Dynamics and Forecast by Geography, 2024-2030 |
18 | Market Segmentation, Dynamics and Forecast by Product Type, 2024-2030 |
19 | Market Segmentation, Dynamics and Forecast by Application, 2024-2030 |
20 | Market Segmentation, Dynamics and Forecast by End use, 2024-2030 |
21 | Product installation rate by OEM, 2023 |
22 | Incline/Decline in Average B-2-B selling price in past 5 years |
23 | Competition from substitute products |
24 | Gross margin and average profitability of suppliers |
25 | New product development in past 12 months |
26 | M&A in past 12 months |
27 | Growth strategy of leading players |
28 | Market share of vendors, 2023 |
29 | Company Profiles |
30 | Unmet needs and opportunity for new suppliers |
31 | Conclusion |
32 | Appendix |