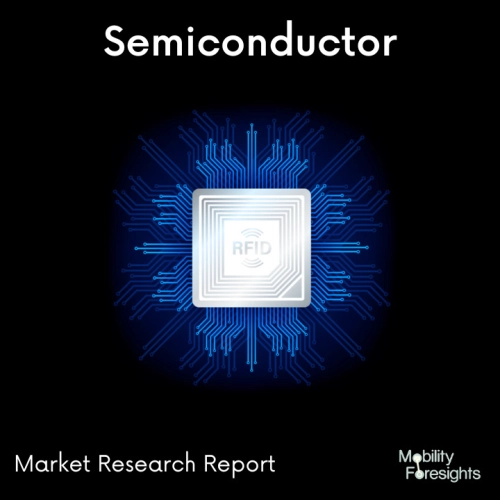
- Get in Touch with Us
Last Updated: Apr 25, 2025 | Study Period: 2023-2030
The wafer edge trimming process,The surface of a wafer is first created with an etch-resistant layer. After that, a wet treatment procedure is used to remove a section of the etch-resistant layer, exposing a section of the surface next to a wafer edge.
The remaining etch-resistant layer is then removed from the remaining wafer by means of an etching procedure.Most wafers typically have a bevel edge as a result of the wafer thinning process.
The presence of the bevel may result in unequal stress being applied to the edge of the wafer when the mechanical tension or thermal stress created by a semiconductor device fabrication process is imposed, which may lead to wafer cracking and delamination.
In order to remove the bevel edge prior to constructing semiconductor devices, a wafer edge trimming process is necessary. Yet, a typical wafer edge trimming procedure that polishes the bevel edge with a grinding wheel may produce particles that contaminate the subsequent procedures.
Furthermore, because of the mechanical force that the grinding wheel places on the wafer, it could be broken or cracked off.
The current invention offers a wafer edge trimming technique in accordance with one aspect, and the wafer edge trimming method includes the following processes.
The surface of a wafer is first created with an etch-resistant layer. After that, a wet treatment procedure is used to remove a section of the etch-resistant layer, exposing a section of the surface next to a wafer edge.
The Global Wafer edge trimming equipmentMarket accountedfor $XX Billion in 2022 and is anticipated to reach $XX Billion by 2030, registering a CAGR of XX% from 2023 to 2030.
Nowadays, thin wafer applications like TSV and ultra-thin applications like BSI use the phrase "Edge Trimming" as a widespread industry term.
Equipment and process engineers have experimented with a variety of machine tools and procedural procedures in an effort to get results that are at least acceptable but not optimal. For the greatest results, TSV and BSI applications typically require precise edge trimming.
In some cases, edge trimming will enable the device wafer to be produced to be ground exceedingly thin. As silicon wafers are crushed to these thin dimensions, they change from their more typical hard and brittle physical features at thicknesses to become highly flexible.
Due to the silicon wafer's large thickness reduction after thinning, the diamond abrasive process known as "edge trimming," which is performed to the silicon wafer edge, is a crucial step in the three-dimensional microelectronics processing technique.
Yet, the wafer edge flaws brought on by edge trimming are frequently disregarded. Although the mechanisms causing the flaws in Si produced by trimming may be comparable to those causing them by grinding, a thorough investigation and risk assessment have not yet been carried out.
On the edge-trimmed Si sidewall, the various stress relief processing techniques can result in varied morphologies and defect elimination behaviours.
Sl no | Topic |
1 | Market Segmentation |
2 | Scope of the report |
3 | Abbreviations |
4 | Research Methodology |
5 | Executive Summary |
6 | Introduction |
7 | Insights from Industry stakeholders |
8 | Cost breakdown of Product by sub-components and average profit margin |
9 | Disruptive innovation in the Industry |
10 | Technology trends in the Industry |
11 | Consumer trends in the industry |
12 | Recent Production Milestones |
13 | Component Manufacturing in US, EU and China |
14 | COVID-19 impact on overall market |
15 | COVID-19 impact on Production of components |
16 | COVID-19 impact on Point of sale |
17 | Market Segmentation, Dynamics and Forecast by Geography, 2023-2030 |
18 | Market Segmentation, Dynamics and Forecast by Product Type, 2023-2030 |
19 | Market Segmentation, Dynamics and Forecast by Application, 2023-2030 |
20 | Market Segmentation, Dynamics and Forecast by End use, 2023-2030 |
21 | Product installation rate by OEM, 2023 |
22 | Incline/Decline in Average B-2-B selling price in past 5 years |
23 | Competition from substitute products |
24 | Gross margin and average profitability of suppliers |
25 | New product development in past 12 months |
26 | M&A in past 12 months |
27 | Growth strategy of leading players |
28 | Market share of vendors, 2023 |
29 | Company Profiles |
30 | Unmet needs and opportunity for new suppliers |
31 | Conclusion |
32 | Appendix |