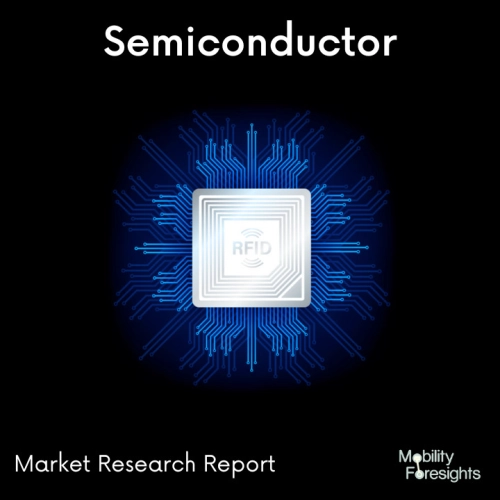
- Get in Touch with Us
Last Updated: Apr 25, 2025 | Study Period:
Metallurgical microscope systems called wafer inspection microscopes have longer clearance or extra reach to suit different wafer sizes.
Motorized lens changers and modules with laser-based autofocus are examples of semiconductor OEM modular systems.
The wafer defect detection system finds physical defects (also known as foreign materials or particles) and pattern defects on wafers while also determining their position coordinates (X, Y).
Systematic and random defects are two categories of flaws. Random defects are mostly created by particles that adhere to a wafer surface; hence, it is impossible to forecast where these particles will be. A wafer defect inspection system's primary function is to locate and identify faults on wafers.
The conditions of the mask and exposure process, on the other hand, are what produce systematic flaws, which always appear in the same place on the projected circuit pattern of all the dies. They occur in places with extremely challenging exposure circumstances that call for precise adjusting.
The Global Wafer inspection microscopeMarket accountedfor $XX Billion in 2023 and is anticipated to reach $XX Billion by 2030, registering a CAGR of XX% from 2024 to 2030.
For wafer foundries, integrated device manufacturing (IDM), fabless, and outsourced semiconductor assembly and test, wafer inspection is always a crucial stage (OSAT).
The requirements for wafer inspection have tightened to account for the ongoing reduction in size and increase in complexity of semiconductor devices.
However, if flaws on the wafer are not eradicated or filtered out, they may be ignored and may proceed to the final stages of production and assembly, which might be an expensive error for the manufacturers. As a result, there will be a rise in the demand for high-quality wafer production.
By comparing the circuit pattern images of the adjacent dies, the wafer defect detection system finds faults. As a result, systematic flaws can go undetected by a wafer defect inspection system.
A bare wafer or a patterned process wafer can both be subjected to inspection. These all have various system configurations.
Sl no | Topic |
1 | Market Segmentation |
2 | Scope of the report |
3 | Abbreviations |
4 | Research Methodology |
5 | Executive Summary |
6 | Introduction |
7 | Insights from Industry stakeholders |
8 | Cost breakdown of Product by sub-components and average profit margin |
9 | Disruptive innovation in the Industry |
10 | Technology trends in the Industry |
11 | Consumer trends in the industry |
12 | Recent Production Milestones |
13 | Component Manufacturing in US, EU and China |
14 | COVID-19 impact on overall market |
15 | COVID-19 impact on Production of components |
16 | COVID-19 impact on Point of sale |
17 | Market Segmentation, Dynamics and Forecast by Geography, 2024-2030 |
18 | Market Segmentation, Dynamics and Forecast by Product Type, 2024-2030 |
19 | Market Segmentation, Dynamics and Forecast by Application, 2024-2030 |
20 | Market Segmentation, Dynamics and Forecast by End use, 2024-2030 |
21 | Product installation rate by OEM, 2023 |
22 | Incline/Decline in Average B-2-B selling price in past 5 years |
23 | Competition from substitute products |
24 | Gross margin and average profitability of suppliers |
25 | New product development in past 12 months |
26 | M&A in past 12 months |
27 | Growth strategy of leading players |
28 | Market share of vendors, 2023 |
29 | Company Profiles |
30 | Unmet needs and opportunity for new suppliers |
31 | Conclusion |
32 | Appendix |