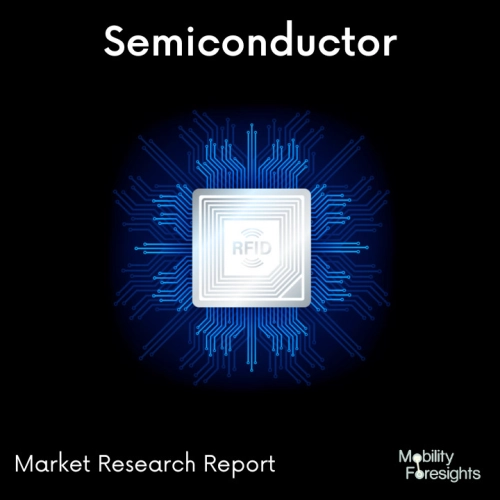
- Get in Touch with Us
Last Updated: Apr 25, 2025 | Study Period: 2024-2030
Mechanical Chemical Wafer semiconductor wafer's surface can be polished to remove material by employing a procedure that combines chemical cleaning with mechanical polishing.
While the mechanical component of CMP eliminates material by physical abrasion, the chemical component of CMP interacts with the surface being polished.
Wafer grinding machines are made to grind complex materials with high levels of flatness and surface quality perfection, frequently decreasing or eliminating the requirement for lapping.
The Global Wafer Polishing Machine market accounted for $XX Billion in 2023 and is anticipated to reach $XX Billion by 2030, registering a CAGR of XX% from 2024 to 2030.
One of the main factors influencing the market expansion at the moment is the extensive use of cutting-edge semiconductor wafer grinding and polishing equipment for wafer thinning and damage mitigation.
Advanced, essential parts are often employed while making semiconductor wafers and are considered as polishing and grinding equipment.
As some of the common techniques used with the use of metallographic instruments, disc finishing machines, and lapping machines, they include deposition, lithography, Ion implant, etching, and cleaning.
In order to thin and refine the product while maintaining a smooth and damage-free surface, semiconductor wafer polishing and grinding equipment is used. For the purpose of creating integrated circuits, foundries and memory producers frequently use them because of their qualities.
In keeping with this, key technological developments, such the use of MOS and CMP technologies to preserve the wafer surface profile during production processes, are functioning as other growth-inducing elements.
The industry is further aided by the widespread adoption of wireless technologies, such as the Internet of Things (IoT) and artificial intelligence (AI), which enable the development of smart gadgets.
The production of system on a chip (SoC) dice in wafer manufacturing facilities also makes extensive use of polishing and grinding equipment, which is boosting the market.
The market is expected to grow thanks to a number of other factors, including the increasing demand for smaller, thinner wafers for electronic devices, ongoing investments in R&D activities, and strategic alliances between leading market players to develop high-performance wafer polishing and grinding tools.
NTS developed machinery for 8-inch semiconductor wafer grinding. Equipment for grinding and polishing LED wafers is produced by the South Korean company NTS.
In addition to global businesses like Osram, HC Semitek, and Saman, they supply equipment to South Korean firms like Samsung Electronics, Seoul Semiconductor, and LG Display.
It aspires to develop into a manufacturer of pre-process and post-process package equipment for semiconductors. This machinery can accurately mould the wafer's outside diameter into any required shape. It may be precisely produced to the size and shape that clients require.
The minimum vibration, or load, that has an impact on wafer processing quality is a major feature of NTS' "Edge Grinder." In order to precisely detect wafer positions and shapes, the Edge Grinder uses precision CCD sensors.
Additionally, they may position the wafer with the work spin and minimise the equipment load with the precision spin, which makes the production efficiency and speed larger than that of our competitors. The 6-inch Edge Grinder was a prior model from NTS.
Zhonghua Semiconductor, China's top manufacturer of semiconductor wafers, has received 6-inch equipment from it since its inception last year. The first half of this year will see the delivery of more than 30 units of equipment to wafer producers worldwide thanks to recent additional orders.
In order to deliver 8-inch equipment, NTS is also pushing for negotiations.
By becoming more productive and competitively priced in comparison to rivals in the key international equipment market, including Japanese equipment, they plan to steadily increase the market share for semiconductor grinding equipment.
The EVG Series of high-precision vertical grinding machines for the development of ultra-smooth surfaces has been introduced by Wheeling, Pennsylvania's Engis Corp, a supplier of superabrasive lapping, grinding, honing, and polishing equipment.
Advanced materials can be ground with the machines to a high degree of precision in flatness and surface quality, considerably lowering or even eliminating the need for subsequent lapping and allowing for a straight transition from grinding to final polish.
Applications include the grinding or back-thinning of semiconductor wafers, including those made of silicon carbide (SiC), gallium arsenide (GaAs), sapphire, silicon, gallium nitride (GaN), aluminium nitride (AIN), and indium phosphide (InP), as well as substrates for advanced semiconductor packaging, including MEMS (ceramic, polyimide).
The most cutting-edge model offers automated thickness options, including multi-point contact probing for multiple wafer grinding and a choice of contact or non-contact continuous in-process measuring for single-wafer machining.
The new machines come in three variants (EVG-200, EVG-250, and EVG-300), each of which has a programmable logic controller, a work table that can rotate at a maximum speed of 400 rpm, and wheels that can spin at a maximum speed of 2000 rpm.
For the EVG-300, dimensions range from 1050 x 1050 x 2020 to 800 x 800 x 1900 for the EVG-200. A range of chuck options, simple access to the work area, and ergonomic design were all taken into consideration when creating each one.
Sl no | Topic |
1 | Market Segmentation |
2 | Scope of the report |
3 | Abbreviations |
4 | Research Methodology |
5 | Executive Summary |
6 | Introduction |
7 | Insights from Industry stakeholders |
8 | Cost breakdown of Product by sub-components and average profit margin |
9 | Disruptive innovation in the Industry |
10 | Technology trends in the Industry |
11 | Consumer trends in the industry |
12 | Recent Production Milestones |
13 | Component Manufacturing in US, EU and China |
14 | COVID-19 impact on overall market |
15 | COVID-19 impact on Production of components |
16 | COVID-19 impact on Point of sale |
17 | Market Segmentation, Dynamics and Forecast by Geography, 2024-2030 |
18 | Market Segmentation, Dynamics and Forecast by Product Type, 2024-2030 |
19 | Market Segmentation, Dynamics and Forecast by Application, 2024-2030 |
20 | Market Segmentation, Dynamics and Forecast by End use, 2024-2030 |
21 | Product installation rate by OEM, 2023 |
22 | Incline/Decline in Average B-2-B selling price in past 5 years |
23 | Competition from substitute products |
24 | Gross margin and average profitability of suppliers |
25 | New product development in past 12 months |
26 | M&A in past 12 months |
27 | Growth strategy of leading players |
28 | Market share of vendors, 2023 |
29 | Company Profiles |
30 | Unmet needs and opportunity for new suppliers |
31 | Conclusion |
32 | Appendix |