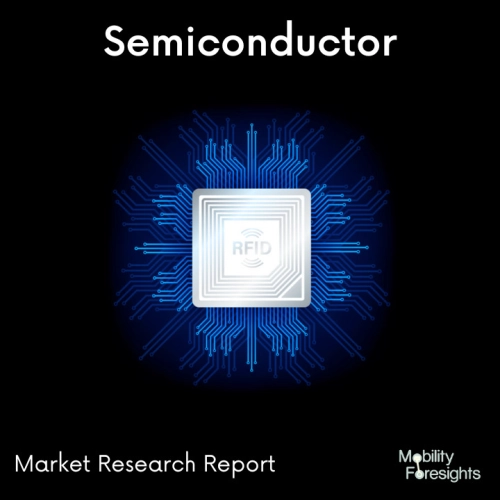
- Get in Touch with Us
Last Updated: Apr 25, 2025 | Study Period: 2024-2030
In addition to air bubbles, breakage, and other flaws, X-ray inspection systems identify all impurities whose density considerably differs from that of the product being inspected.
The goods you sell are transported uniformly through the X-ray beam on a conveyor belt by our X-ray equipment made specifically for examining food.
The radiation is converted into an electrical signal by the detector that is mounted above the conveyor belt. The specialized analytical software turns this into a digital X-ray image, which it then checks for impurities and manufacturing flaws. Integrated separation systems provide the effective removal of tainted or flawed goods.
The Global Wafer X-ray Inspection System market accounted for $XX Billion in 2023 and is anticipated to reach $XX Billion by 2030, registering a CAGR of XX% from 2024 to 2030.
The SEAMARK ZM X5600 is a compact, accurate microfocus Wafer X-ray Inspection System that can be used in R&D facilities, labs, quality inspection rooms, etc. It is the top option for a tiny part of the Wafer X-ray Inspection System.
I/C chip A piece of non-destructive testing equipment designed specifically for assessing potential internal IC chip flaws is the Wafer X-ray Inspection System.
It is one of the greatest methods for finding IC chip flaws. The internal X-ray tube of the X-ray detection device is primarily responsible for emitting X-rays that irradiate the IC chip and allow for imaging.
The digital tablet receives the visual signal after the X-rays have passed through the object and then sends it to the computer. Following software processing, a real-time image will be displayed on the screen.
X-ray testing is within the nondestructive category. The enhanced BGA inspection function X5600 industrial Wafer X-ray Inspection System can quickly select and mark a single solder ball, or select the solder balls to be inspected using a matrix box; it can manually or automatically identify BGA solder balls and complete the inspection. automatically find flaws. Automatic size, area, broken wire, bridging, etc.
detection is possible with the X5600.Modular image algorithm. Customized software algorithms based on product features and request to achieve fully automatic defect inspection algorithms, including Y/N, crack, broken wire, offset size, and quantity, etc.
Sl no | Topic |
1 | Market Segmentation |
2 | Scope of the report |
3 | Abbreviations |
4 | Research Methodology |
5 | Executive Summary |
6 | Introduction |
7 | Insights from Industry stakeholders |
8 | Cost breakdown of Product by sub-components and average profit margin |
9 | Disruptive innovation in the Industry |
10 | Technology trends in the Industry |
11 | Consumer trends in the industry |
12 | Recent Production Milestones |
13 | Component Manufacturing in US, EU and China |
14 | COVID-19 impact on overall market |
15 | COVID-19 impact on Production of components |
16 | COVID-19 impact on Point of sale |
17 | Market Segmentation, Dynamics and Forecast by Geography, 2024-2030 |
18 | Market Segmentation, Dynamics and Forecast by Product Type, 2024-2030 |
19 | Market Segmentation, Dynamics and Forecast by Application, 2024-2030 |
20 | Market Segmentation, Dynamics and Forecast by End use, 2024-2030 |
21 | Product installation rate by OEM, 2023 |
22 | Incline/Decline in Average B-2-B selling price in past 5 years |
23 | Competition from substitute products |
24 | Gross margin and average profitability of suppliers |
25 | New product development in past 12 months |
26 | M&A in past 12 months |
27 | Growth strategy of leading players |
28 | Market share of vendors, 2023 |
29 | Company Profiles |
30 | Unmet needs and opportunity for new suppliers |
31 | Conclusion |
32 | Appendix |