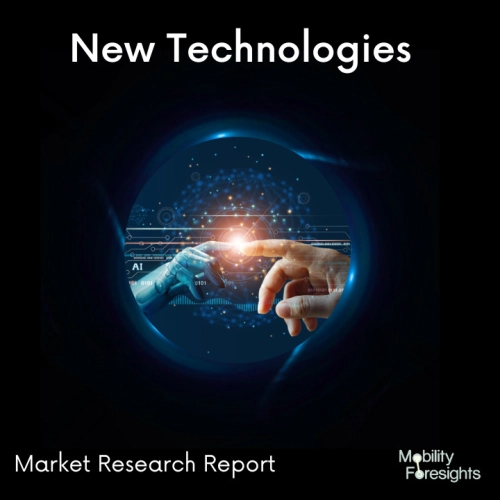
- Get in Touch with Us
Last Updated: Apr 25, 2025 | Study Period: 2024-2030
The reason why water-based ink has a softer feel than, say, plastisol ink is simple. Plastisol, unsurprisingly, is made of plastic and solidifies when heated. It is placed on top of the garment's fabric. Water-based ink, on the other hand, permeates into the cloth rather than resting on top.
Now let's talk about breathability and durability. The good news is that water-based inks receive an A1 rating in both categories. As previously stated, water-based inks seep into the fabric of the sustainable clothing, allowing many of the gaps between the fibers to remain open, whereas plastisol inks and the infamous sweat patches do not.
In terms of durability, without sounding like a broken record, because of the link made between the design and the fabric, the print should theoretically last as long as the garment.
Next, while water-based dyes are generally more environmentally benign, it is crucial to note that they do include plastic in the form of acrylics and other binders. While they do not include PVC, they do rely on solvents that evaporate. Yes, water is the principal solvent, however formaldehyde and alcohol are frequently used as co-solvents.
To summarize, I am glad that shirts are screen printed with water-based dye, but recognise that it is not a 100% eco-friendly approach, which is why I thought it important to disclose its drawbacks alongside its advantages.
Staining is frequently a finishing step that may make or break a project's look. Unfortunately, there is no silver bullet that will ensure a positive outcome. However, the more alternatives there are, the higher chances of receiving excellent outcomes. This is why I always have water-based colors available.
A water-based dye can provide an appearance that is distinct from an oil stain. Large pigment particles are simply suspended in a solvent in oil stains. The pigments essentially sit on the surface of the wood to give it color when the stain is applied. This might make it difficult to get a rich, natural color without revealing the shape of the wood.
Water-based colors function differently.The dye particles are so minute that they dissolve in solution, much like sugar in water. This permits the dye particles to be carried deep into the wood fibers by the water. The end effect is more clear and natural. should have a really deep, penetrating color that yet shows the form of the wood.
The exquisite form of woods like curly or birdseye maple may truly pop with a dye. A dye's penetrating quality makes it an excellent choice when a deep, dark color is desired.
There are dyes designed for use with various solvents, including water, alcohol, and oil-soluble variants. Water-based dyes, on the other hand, are by far the easiest to use due to their slower drying time.
A water-based dye can be mixed from either a powder or a liquid concentration (as seen in the photo above). The dyes are available in a variety of colors, including wood tones and pure colors. Two or more can be combined to produce almost any color in the rainbow.
Always use accurate quantities and keep note of the recipe when mixing a powdered color. This manner, if required, may quickly match the same color again. It's easier for me to simply measure by volume, but may also weigh the powder.
Although the dye box directions include a suggested concentration, this is only a rough suggestion. The basic dye color can be brightened or darkened by adjusting the dye and water ratio. Experimentation may be required to achieve the desired color. You'll see that a little dye goes a long way.
In hot water, the color powder will dissolve more easily. If some of the powder does not dissolve, sift it off before applying the color to the wood.
Applying a water-based dye is slightly different from applying an oil stain, but it is just as simple.
The Global Water Based Dyes Market accounted for $XX Billion in 2023 and is anticipated to reach $XX Billion by 2030, registering a CAGR of XX% from 2024 to 2030.
Archroma, a global pioneer in color and specialty chemicals for sustainable solutions, has introduced Appretan NTR, a groundbreaking water-based textile coating binder made from renewable natural components.
Archroma is presenting another new invention based on natural components, after the well-publicized EarthColors, a variety of colors synthesized from materials such as almond husks or saw palmetto leaves - bio-waste from the agricultural and herbal sectors.
Appretan NTR, a water-based textile coating binder created for applications such as tea bags, coffee filters, or capsules, uses a natural, renewable raw material that is abundantly available near the Appretan NTR manufacturing location in Lamotte, France.
The firm is dedicated to producing goods that adhere to The Archroma Way: safe, efficient, and enhanced. The strategy stems from Archroma's firm belief that it is feasible to make the textile business more sustainable.Appretan NTR has no biocides or alkylphenol ethoxylates (APEO) and emits no formaldehyde.
When compared to the industry standard technique, it has been engineered to obtain the best qualities with no additional curing step at high temperatures, saving substantial energy for textile companies and the environment.
Appretan NTR was originally designed for the chemical bonding of nonwovens for technical textiles and coating. It has outstanding film forming characteristics and a particularly hydrophobic behavior.
Furthermore, because of the unique chemistry of this binder, it is resistant to water, mild solvents, oil, and fat, and it increases dry and wet tensile strength. NTR Appretan
Appretan NTR has also been adapted for companies that operate in the highly regulated, developing business of hot liquid filtration, utilizing Archroma's best-in-class expertise of food contact standards.
Appretan NTR conforms with worldwide food contact regulations such as FDA 176-170, BfR XXXVI and BfR XXXVI/1, certifying the end-product's acceptability even under extreme circumstances such as immersion in boiling water.
Sl no | Topic |
1 | Market Segmentation |
2 | Scope of the report |
3 | Abbreviations |
4 | Research Methodology |
5 | Executive Summary |
6 | Introduction |
7 | Insights from Industry stakeholders |
8 | Cost breakdown of Product by sub-components and average profit margin |
9 | Disruptive innovation in the Industry |
10 | Technology trends in the Industry |
11 | Consumer trends in the industry |
12 | Recent Production Milestones |
13 | Component Manufacturing in US, EU and China |
14 | COVID-19 impact on overall market |
15 | COVID-19 impact on Production of components |
16 | COVID-19 impact on Point of sale |
17 | Market Segmentation, Dynamics and Forecast by Geography, 2024-2030 |
18 | Market Segmentation, Dynamics and Forecast by Product Type, 2024-2030 |
19 | Market Segmentation, Dynamics and Forecast by Application, 2024-2030 |
20 | Market Segmentation, Dynamics and Forecast by End use, 2024-2030 |
21 | Product installation rate by OEM, 2023 |
22 | Incline/Decline in Average B-2-B selling price in past 5 years |
23 | Competition from substitute products |
24 | Gross margin and average profitability of suppliers |
25 | New product development in past 12 months |
26 | M&A in past 12 months |
27 | Growth strategy of leading players |
28 | Market share of vendors, 2023 |
29 | Company Profiles |
30 | Unmet needs and opportunity for new suppliers |
31 | Conclusion |
32 | Appendix |