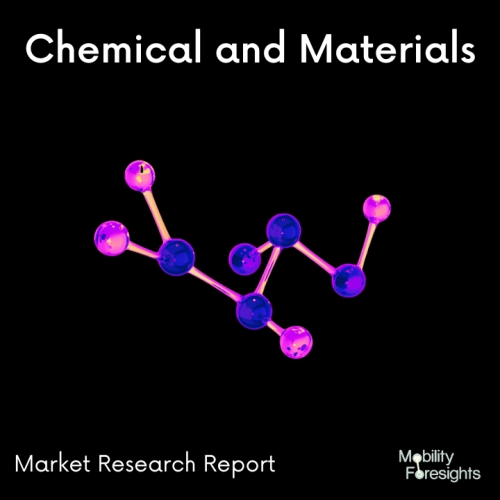
- Get in Touch with Us
Last Updated: Apr 25, 2025 | Study Period: 2024-2030
Oils for cutting water soluble the term "soluble oils" is more frequently used to describe these cutting oils. This is a misnomer though, as they don't actually dissolve in water but instead combine to make an emulsion.
These mineral oil-based concentrates known as emulsifiable oils have emulsifiers that enable them to combine with water to create a milky white emulsion.
Additionally, they include biocide to help eliminate bad odors, rust and corrosion inhibitors, and additives to enhance their lubricating qualities.
Water emulsifiable oils have several benefits, including good cooling, low viscosity and therefore acceptable wetting abilities, non-flammability and non-toxicity, ease of cleaning from small chips and wear particles using ordinary filters, and comparatively low startup and disposal costs.
There are a few drawbacks as well, such as poor lubricity, bad odor, misting, etc. But since they combine the lubricating benefits of oil with the cooling benefits of water and can be utilized in a variety of machining and grinding activities, these lubricants are the most widely used cutting fluids in use today.
The Global Water Soluble Cutting oil market accounted for $XX Billion in 2023 and is anticipated to reach $XX Billion by 2030, registering a CAGR of XX% from 2024 to 2030.
With Daphne Alphacool CS, a water-soluble cutting oil from Idemitsu, the workplace has been helped to improve thanks to a unique surfactant that has been given strong heat resistance properties.
This oil effectively and drastically reduces mist and volatile components. In addition, compared to traditional water-soluble cutting oils, it minimizes shop floor odor and stickiness in and around the machine.
It is appropriate for high speed and high-pressure machining centers because of its outstanding defoaming property.
It is practical for machining all product kinds since it is compatible with both metal and non-metal, and because it is also compatible with rubber, it is a safer cutting oil for machine parts such as coolant hose and electrical wires.
The kind and shape of work materials have diversified, leading to considerable internationalization in the machining sectors in recent years. Higher processing efficiency is therefore necessary to improve cost competitiveness.
Active efforts are made to raise the cutting speed and feed rate, resulting in cutting temperatures that are higher than before, to achieve high efficiency. As a result, cutting oils that are water soluble and have strong cooling properties are the most common.
Sl no | Topic |
1 | Market Segmentation |
2 | Scope of the report |
3 | Abbreviations |
4 | Research Methodology |
5 | Executive Summary |
6 | Introduction |
7 | Insights from Industry stakeholders |
8 | Cost breakdown of Product by sub-components and average profit margin |
9 | Disruptive innovation in the Industry |
10 | Technology trends in the Industry |
11 | Consumer trends in the industry |
12 | Recent Production Milestones |
13 | Component Manufacturing in US, EU and China |
14 | COVID-19 impact on overall market |
15 | COVID-19 impact on Production of components |
16 | COVID-19 impact on Point of sale |
17 | Market Segmentation, Dynamics and Forecast by Geography, 2024-2030 |
18 | Market Segmentation, Dynamics and Forecast by Product Type, 2024-2030 |
19 | Market Segmentation, Dynamics and Forecast by Application, 2024-2030 |
20 | Market Segmentation, Dynamics and Forecast by End use, 2024-2030 |
21 | Product installation rate by OEM, 2023 |
22 | Incline/Decline in Average B-2-B selling price in past 5 years |
23 | Competition from substitute products |
24 | Gross margin and average profitability of suppliers |
25 | New product development in past 12 months |
26 | M&A in past 12 months |
27 | Growth strategy of leading players |
28 | Market share of vendors, 2023 |
29 | Company Profiles |
30 | Unmet needs and opportunity for new suppliers |
31 | Conclusion |
32 | Appendix |