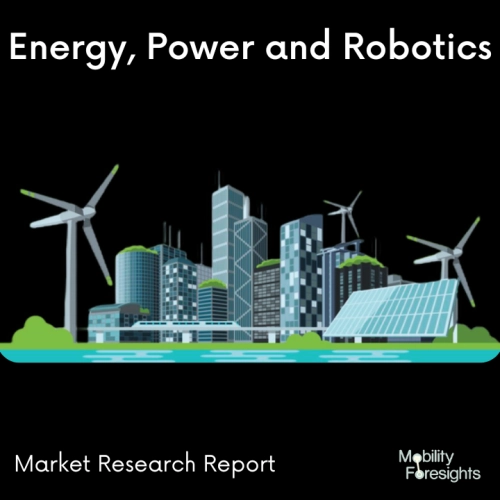
- Get in Touch with Us
Last Updated: Apr 25, 2025 | Study Period: 2023-2030
Lightning protection systems are used to prevent or reduce the damage caused by lightning strikes to buildings. They safeguard a building's interior electrical components, aiding in the prevention of fires and electrocution.
An exterior lightning protection system (LPS) and surge protection measures (SPMs) are included in the lightning and surge protection for wind turbine systems to safeguard electrical and electronic equipment. It is advisable to split the wind turbine into lightning protection zones (LPZs) in order to prepare protective measures.
The purpose of an external lightning protection system (LPS) is to discharge lightning current from the site of a direct lightning hit to the ground, including strikes to wind turbine towers.
The Global Wind Turbine Lightning protection system market accounted for $XX Billion in 2022 and is anticipated to reach $XX Billion by 2030, registering a CAGR of XX% from 2023 to 2030.
Lightning No Match for Wind Turbine Blade Protection System.Wind turbines are excellent targets for lightning since they are hundreds of feet above the earth, similar to tall trees, structures, and telephone poles. They will be hit just because of their height.
For traditional wind turbine blades, lightning protection technologies are available. However, protection was required for blades built of a novel material class called thermoplastic resin composites, which were welded using a ground-breaking thermal (heat-based) method created by researchers at the National Renewable Energy Laboratory (NREL).
Plastic bottles and other thermoplastic materials may be recycled more readily than the thermoset materials that are currently utilised to manufacture wind turbine blades. The production time and cost of blades are decreased since thermoplastics cure at ambient temperature as opposed to thermoset materials, which require heat to complete the curing process.
These advantages are possible and are even increased by NREL's thermoplastic thermal welding technology for blades, which replaces the adhesives currently used to assemble blades. The drawbacks of extra weight and possible cracking are eliminated when welding is used in place of adhesives.
1 | Market Segmentation |
2 | Scope of the report |
3 | Abbreviations |
4 | Research Methodology |
5 | Executive Summary |
6 | Introduction |
7 | Insights from Industry stakeholders |
8 | Cost breakdown of Product by sub-components and average profit margin |
9 | Disruptive innovation in the Industry |
10 | Technology trends in the Industry |
11 | Consumer trends in the industry |
12 | Recent Production Milestones |
13 | Component Manufacturing in US, EU and China |
14 | COVID-19 impact on overall market |
15 | COVID-19 impact on Production of components |
16 | COVID-19 impact on Point of sale |
17 | Market Segmentation, Dynamics and Forecast by Geography, 2023-2030 |
18 | Market Segmentation, Dynamics and Forecast by Product Type, 2023-2030 |
19 | Market Segmentation, Dynamics and Forecast by Application, 2023-2030 |
20 | Market Segmentation, Dynamics and Forecast by End use, 2023-2030 |
21 | Product installation rate by OEM, 2023 |
22 | Incline/Decline in Average B-2-B selling price in past 5 years |
23 | Competition from substitute products |
24 | Gross margin and average profitability of suppliers |
25 | New product development in past 12 months |
26 | M&A in past 12 months |
27 | Growth strategy of leading players |
28 | Market share of vendors, 2023 |
29 | Company Profiles |
30 | Unmet needs and opportunity for new suppliers |
31 | Conclusion |
32 | Appendix |