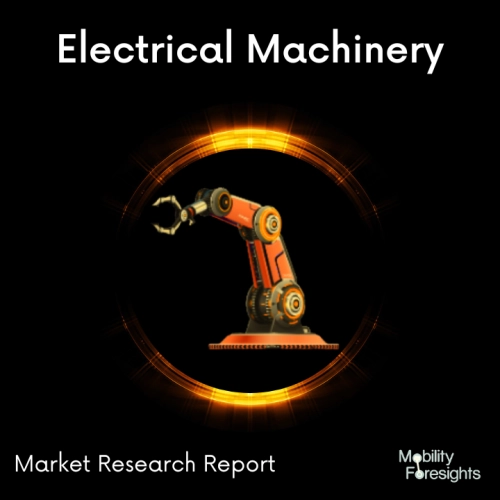
- Get in Touch with Us
Last Updated: Apr 25, 2025 | Study Period: 2024-2030
The most widespread application of wire EDM is in the production of moulds and dies, particularly for blanking punches and extrusion dies.
EDM is most frequently used to produce metal tools and components, while it can be utilised for everything from prototypes to large production runs.
Electric spark erosion is used to remove metal during the controlled metal-removal process known as electrical discharge machining (EDM).
In this procedure, the workpiece is sliced (eroded) using an electric spark as the cutting tool to create the finished item in the desired shape.
Wire EDM is a type of electrical discharge machining (EDM) that physically runs an electrode through the workpiece. A CNC system carefully monitors the wire.Wire EDM eliminates metal, much like any other machining tool, except it does so electrically by spark erosion.
The aerospace, automotive, and electronics industries, where manufacturing volumes are often modest, are the ones that employ the EDM process the most frequently. It is also most commonly used by the mold-making, tooling, and die industries.
Brass, copper, and copper-tungsten are also frequently used as EDM tool materials. With the use of graphite electrodes and a power supply of 30 A at a frequency of roughly 3000 kHz, the least amount of tool wear is possible in EDM. On reduce actual tool wear, a steel coating is applied to graphite electrode tools.
The Global Wire EDM Machine market accounted for $XX Billion in 2023 and is anticipated to reach $XX Billion by 2030, registering a CAGR of XX% from 2024 to 2030.
The Spark Track platform is entirely compatible with Turbo Tech, a new standard technology that is quicker than the speed technology now used on wire-cutting EDM machines.
Turbo Tech is available for all wire types (brass, speed, and quality), is fully integrated in Uniqua or AC Cut 2 interfaces, and provides a great speed-accuracy compromise in both favourable and unfavourable flushing settings.
It is not only state-of-the-art, but also a sustainable technology because of the quicker final machining time and the accompanying decreased wire usage.
EDM machines allow clients to determine their priorities whenever they want and get the most out of their machines while also extending production time.
It makes the operator's life easier by adjusting to his style of working, providing the option to change the on-board programmes, and allowing for flexible control of the workshop thanks to its straightforward workflow and short learning curve.
It is simple to use for both experienced users and operators who are familiar to ISO programming because integrated help and tutorials are always available.
Sl no | Topic |
1 | Market Segmentation |
2 | Scope of the report |
3 | Abbreviations |
4 | Research Methodology |
5 | Executive Summary |
6 | Introduction |
7 | Insights from Industry stakeholders |
8 | Cost breakdown of Product by sub-components and average profit margin |
9 | Disruptive innovation in the Industry |
10 | Technology trends in the Industry |
11 | Consumer trends in the industry |
12 | Recent Production Milestones |
13 | Component Manufacturing in US, EU and China |
14 | COVID-19 impact on overall market |
15 | COVID-19 impact on Production of components |
16 | COVID-19 impact on Point of sale |
17 | Market Segmentation, Dynamics and Forecast by Geography, 2024-2030 |
18 | Market Segmentation, Dynamics and Forecast by Product Type, 2024-2030 |
19 | Market Segmentation, Dynamics and Forecast by Application, 2024-2030 |
20 | Market Segmentation, Dynamics and Forecast by End use, 2024-2030 |
21 | Product installation rate by OEM, 2023 |
22 | Incline/Decline in Average B-2-B selling price in past 5 years |
23 | Competition from substitute products |
24 | Gross margin and average profitability of suppliers |
25 | New product development in past 12 months |
26 | M&A in past 12 months |
27 | Growth strategy of leading players |
28 | Market share of vendors, 2023 |
29 | Company Profiles |
30 | Unmet needs and opportunity for new suppliers |
31 | Conclusion |
32 | Appendix |