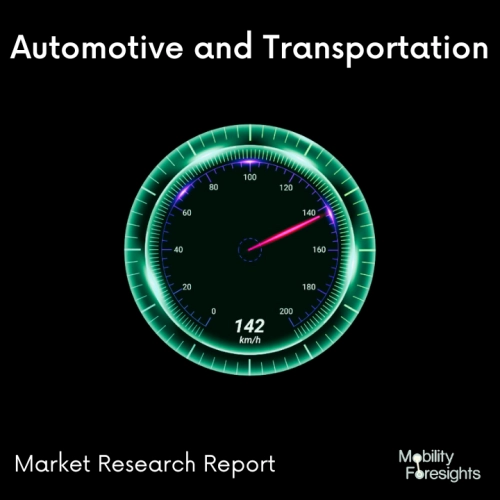
- Get in Touch with Us
Last Updated: Apr 25, 2025 | Study Period: 2024-2030
The Hydrogen and Fuel Cell Technologies Office (HFTO) is working on onboard car hydrogen storage systems that will enable for a driving range of over 300 miles while fulfilling cost, safety, and performance criteria.
Hydrogen storage is a critical enabler of the growth of hydrogen and fuel cell technologies in applications such as fixed power, portable power, and mobility.
Hydrogen has the highest energy density per mass of any fuel; yet, because of its low ambient temperature density, it has a low energy density per unit volume, necessitating the development of new storage technologies with the potential for higher energy density.
Hydrogen can be technically held as a gas or a liquid. High-pressure tanks (350â700 bar [5,000â10,000 psi] tank pressure) are often required for storing hydrogen as a gas. Because the boiling point of hydrogen at one atmospheric pressure is 252.8°C, storing it as a liquid necessitates cryogenic temperatures. Hydrogen can also be stored on solid surfaces (through adsorption) or inside solids (by absorption).
High density hydrogen storage is a difficulty for fixed and portable applications, and it continues to be a major barrier for vehicle applications. The current storage methods usually need large-volume devices that store hydrogen in gaseous form. This is less of a problem in industrial applications, where the volume of compressed gas tanks is less important.
To know more about Global Hydrogen Fuel Cell Vehicle Market, read our report
S No | Overview of Development | Development Detailing | Region of Development | Possible Future Outcomes |
1 | Faurecia to supply CFRP tanks and hydrogen storage systems for Stellantis light commercial vehicles | Stellantis (Amsterdam, Netherlands), the multinational automotive manufacturer formed by the 2021 merger of Fiat Chrysler Automobiles and French company Groupe PSA, and composite hydrogen storage tank technology leader Faurecia (Nanterre, France) have collaborated to equip Stellantisâ new zero-emission family of light commercial vehicles with hydrogen storage systems, as well as fuel cell stacks through Symbio, Faureciaâs joint venture with Michelin. | Global Scale | This would enhance better Technologies and production |
However, fuel-cell automobiles require enough hydrogen to provide a driving experience of further than 300 miles, and also the ability to recharge the vehicle quickly and economically.
While there are numerous light-duty hydrogen fuel cell electric vehicles (FCEVs) on the market with this range, these vehicles will depend on compressed gas inbuilt storage via large-volume, elevated nanocomposite containers. Large storage volumes may be less of an issue for larger vehicles but ensuring adequate hydrogen storage across all light-duty platforms stays a worry.
Hydrogen-powered vehicles are similar to electric vehicles. They have electric motors that move the wheels in the same way as an electric automobile does, but the distinction is in the batteries.
Electric power is stored in a typical battery in an electric car, however in a hydrogen automobile, the electricity is arranged in the form of hydrogen and transformed into electricity. Currently, the cost of automotive storage tanks is too expensive, limiting the utilisation of these vehicles. A 5-kg tank for a car costs roughly USD 4,000-4,500, which is a significant cost boost to the overall cost of the vehicle.
Hydrogen-powered automobiles are more popular in nations such as South Korea and Japan, where their individual governments have provided subsidies for these vehicles as well as financing for the required infrastructure.
Furthermore, in the United States, the state of California offers incentives for the usage of fuel-cell-powered automobiles. Although hydrogen-powered vehicles may be a green solution in the current world, experts think that hydrogen must be created from a noble gas source, resulting in the usage of fossil fuels, whilst electric cars depend on battery power and are thus greener than hydrogen cars.
The Global Automotive Hydrogen Storage Tank Market can be segmented into following categories for further analysis.
The global hydrogen storage tank market accounted for $XX Billion in 2023 and is anticipated to reach $XX Billion by 2030, registering a CAGR of XX% from 2024 to 2030.
Hydrogen-powered vehicles are similar to electric vehicles. They have electric motors that move the wheels in the same way as an electric automobile does, but the distinction is in the batteries.
Electric power is stored in a typical battery in an electric car, however in a hydrogen automobile, the electricity is arranged in the form of hydrogen and transformed into electricity. Currently, the cost of automotive storage tanks is too expensive, limiting the utilisation of these vehicles.
Hydrogen-powered automobiles are more popular in nations such as South Korea and Japan, where their individual governments have provided subsidies for these vehicles as well as financing for the required infrastructure.
Furthermore, in the United States, the state of California offers incentives for the usage of fuel-cell-powered automobiles. Although hydrogen-powered vehicles may be a green solution in the current world, experts think that hydrogen must be created from a noble gas source, resulting in the usage of fossil fuels, whilst electric cars depend on battery power and are thus greener than hydrogen cars.
Linde, a leading industrial gas company, and BMW Group, a leading automaker, have announced a partnership to develop and produce hydrogen storage tanks for fuel cell electric vehicles (FCEVs). The partnership is aimed at developing new hydrogen storage tank technologies that are more efficient, cost-effective, and safer.
Air Liquide, another leading industrial gas company, has announced a â¬150 million investment in hydrogen storage tank production. The investment will be used to expand Air Liquide's existing hydrogen storage tank production capacity and to develop new hydrogen storage tank technologies.
Hydrogen contains roughly three times the energy content of gasoline in terms of massâ120 MJ/kg for hydrogen against 44 MJ/kg for gasoline. However, on a volume basis, the situation is flipped; liquid hydrogen has a density of 8 MJ/L, whereas gasoline has a density of 32 MJ/L, as seen in the picture contrasting power density of fuels based on lower heating values.
To achieve the driving range requirements for the whole spectrum of light-duty vehicle platforms, onboard hydrogen storage capacity of 5â13 kg hydrogen will be required.
Car manufacturers often install two or three gas storage facilities with an overall capacity of around 150 litres between front and rear suspension. Since they are filled to a pressure of up to 875 bar, these tanks must fulfil extremely stringent safety standards.
This closely correlates to the pressure at the bottom of the water in the Mariana Trench in the Pacific Ocean, which, at around 11,000 metres, is the worldâs deepest point. Until date, the tanks have been less than one metre long and comprised an inner plastic container, the liner, that must be gastight in order to hold hydrogen.
These are wrapped in kilometres of strands, which are made up of hundreds upon thousands of carbon filaments that are only a few thousandths of a millimetre thick and provide the tank with its strength. Carbon fibers are a critical component in the manufacture of storage tanks, accounting for around one-third of the expenditures.
The new prototype should be a tenth of the cost of manufacturing and save up to 15% in weight without sacrificing safety.
Hydrogen contains roughly three times the energy content of gasoline in terms of massâ120 MJ/kg for hydrogen against 44 MJ/kg for gasoline. However, on a volume basis, the situation is flipped; liquid hydrogen has a density of 8 MJ/L, whereas gasoline has a density of 32 MJ/L, as seen in the picture contrasting power density of fuels based on lower heating values.
To achieve the driving range requirements for the whole spectrum of light-duty vehicle platforms, onboard hydrogen storage capacity of 5â13 kg hydrogen will be required.
Car manufacturers often install two or three gas storage facilities with an overall capacity of around 150 litres between front and rear suspension. Since they are filled to a pressure of up to 875 bar, these tanks must fulfil extremely stringent safety standards.
This closely correlates to the pressure at the bottom of the water in the Mariana Trench in the Pacific Ocean, which, at around 11,000 metres, is the world's deepest point. Until date, the tanks have been less than one metre long and comprised an inner plastic container, the liner, that must be gastight in order to hold hydrogen.
These are wrapped in kilometres of strands, which are made up of hundreds upon thousands of carbon filaments that are only a few thousandths of a millimetre thick and provide the tank with its strength. Carbon fibers are a critical component in the manufacture of storage tanks, accounting for around one-third of the expenditures.
The new prototype should be a tenth of the cost of manufacturing and save up to 15% in weight without sacrificing safety.
Every hydrogen tank must also demonstrate its ability to endure external mechanical loads, such as those experienced in a rear-end accident. No gas may escape from the storage tanks in these instances as well.
Another advantage of this fuel is that hydrogen may be extensively compressed to conserve space, resulting in one kilogramme of gas containing about three times the energy of one kilogramme of crude oil. Hydrogen-powered automobiles on the market now have ranges of roughly 500 kilometres.
Worthington Industries is involved in innovation of latest technological integrations within the hydrogen storage tank requirements in the market. Type III hydrogen composite tanks have an aluminium liner that is entirely covered in epoxy resin-coated, aerospace-grade carbon fibre.
The pressures in hydrogen cylinders vary from 4,500 to 10,000 psi (310 to 690 bar). The liner is responsible for transferring heat to the pressure relief devices (PRDs). In heat, the lining does not easily degrade. As the resin burns away, the liner retains the composite fibers in place. During an impact event, the hard metal lining supports the composite and avoids or reduces composite bending and breaking.
Luxfer Cylinders is part of the Luxfer Group which is also preforming varied levels of innovations in the market towards better development of cylinder technologies and storage requirements. G-Stor Pro cylinders, which have been rigorously tested to meet applicable worldwide design requirements and regulations, are utilized in a wide range of applications across the world, including transit buses, light, medium, and heavy-duty trucks, garbage vehicles, and bulk gas transportation modules.
The G-Stor Pro cylinders are the greatest, lightest-weight Type 3 alternate fuels cylinders on the market. Since they are 66 percent lightweight than Type 1 all-steel cylinders and up to seven percent lighter than other composite cylinders in the NGV industry, the Luxfer cylinders provide fleet operators with significantly improved fuel economy, increased range, and a significant decrease in vehicular maintenance fees due to lessened wear on vehicles.
Sl no | Topic |
1 | Market Segmentation |
2 | Scope of the report |
3 | Abbreviations |
4 | Research Methodology |
5 | Executive Summary |
6 | Introduction |
7 | Insights from Industry stakeholders |
8 | Cost breakdown of Product by sub-components and average profit margin |
9 | Disruptive innovation in the Industry |
10 | Technology trends in the Industry |
11 | Consumer trends in the industry |
12 | Recent Production Milestones |
13 | Component Manufacturing in US, EU and China |
14 | COVID-19 impact on overall market |
15 | COVID-19 impact on Production of components |
16 | COVID-19 impact on Point of sale |
17 | Market Segmentation, Dynamics and Forecast by Geography, 2024-2030 |
18 | Market Segmentation, Dynamics and Forecast by Product Type, 2024-2030 |
19 | Market Segmentation, Dynamics and Forecast by Application, 2024-2030 |
20 | Market Segmentation, Dynamics and Forecast by End use, 2024-2030 |
21 | Product installation rate by OEM, 2024 |
22 | Incline/Decline in Average B-2-B selling price in past 5 years |
23 | Competition from substitute products |
24 | Gross margin and average profitability of suppliers |
25 | New product development in past 12 months |
26 | M&A in past 12 months |
27 | Growth strategy of leading players |
28 | Market share of vendors, 2024 |
29 | Company Profiles |
30 | Unmet needs and opportunity for new suppliers |
31 | Conclusion |
32 | Appendix |