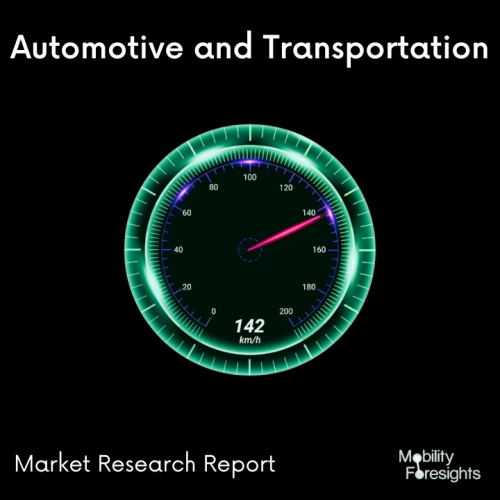
- Get in Touch with Us
Last Updated: Apr 25, 2025 | Study Period: 2024-2030
Plastic fuel tanks are gaining favor due to their significantly lighter weight compared to traditional metal tanks. This weight reduction contributes to enhanced vehicle fuel efficiency, a particularly compelling factor in light of rising fuel costs and the heightened environmental awareness among consumers.
The electric vehicle sector, which relies on lightweight and durable fuel tanks to support battery packs, is driving the demand for plastic fuel tanks. As electric vehicles continue to gain traction, the demand for these tanks is anticipated to surge.
Governments across the globe are imposing increasingly rigorous emission standards for vehicles. This regulatory landscape is propelling the adoption of technologies that can mitigate vehicle emissions, with lightweight fuel tanks being a noteworthy component in this context.
Ongoing advancements in plastic technology have led to the emergence of high-performance plastics ideally suited for fuel tank applications. These innovative plastics exhibit exceptional strength, durability, and corrosion resistance.
Emerging markets like India and China are witnessing a rapid upswing in vehicle sales. This surge in demand for vehicles is consequently fueling the need for automotive components, including plastic fuel tanks.
In an internal combustion engine, a vehicle's fuel tank is an integral part of the fuel system. A tank is a container used to hold motor fuel such as gasoline, diesel, and gas. Fuel tanks nowadays are built of a variety of sophisticated materials, including ferroalloys, aluminium alloys, and polymers.
Stamping of sheet metal and welding of top and lower sections are used to make steel gasoline tanks. Steel gasoline tanks are made of high-viscosity steel with a high ultimate strength. A gasoline tank deforms owing to its viscosity when exposed to external forces, yet it remains leak-proof. Steel gasoline tanks have a significant corrodibility, which is its major drawback.
Water entry into a gasoline tank is quite likely since it can enter as condensate or mixed with fuel and sink to the bottom. Stamping and welding are used to make aluminium gasoline tanks.
They are less corrosive and weigh less than steel fuel tanks. Aluminium fuel tanks have the following drawbacks over steel tanks: potential gasoline leaks due to weld failure during operation; poor deformation capacity (impact resistance); existence of stress risers in a material after a short-term strain greater than its strength; and expensive cost.
Leading global manufacturers are in the midst of transitioning to plastic fuel tanks. Rotational moulding or extrusion are used to make polyethylene and polypropylene fuel tanks.
In comparison to steel and aluminium gasoline tanks, plastic tanks are not corrodible, are resistant to scratches and chipping, are lighter, do not require welding, and are less expensive. Existing plastic fuel tank manufacturing processes allow for the fabrication of components with complicated geometry, efficient use of tank mounting space, and maximum tank volume.
To know more about Global Automotive Fuel Tank Market, read our report
SI No | Timeline | Company | Developments |
1 | December 2021 | Plastic Omnium | Plastic Omnium has been partnered with Total Energies in order to design and develop new plastic materials which are made from recycled polypropylene that can be applied to the automotive industry. |
The following requirements of operational needs should be met by modern plastic fuel tanks which includes vehicles operating temperature range of minus 60 °C to plus 80 °C; local and short duration heating up to 110 °C (high temperature near areas of more intense sunlight, exhaust system, points of contact with the wire bundles); leak proofness at an excessive pressure of up to 0.02 MPa.
Although plastic-tank applications have experienced some reversals as a result of the stricter permeation standards, some experts believe their usage will gain momentum by the end of the decade as new plastics technology is converted to commercially feasible operations.
The major drivers projected to drive market expansion in the future years are rising demand for lightweight cars for fuel economy, increased vehicle manufacturing, and growing urbanization.
One of the key reasons driving market expansion is the rising demand for and sales of commercial vehicles as a consequence of the rise in the e-commerce sector, which has resulted in the growth of the logistics and construction industries. However, issues such as increasing electric car adoption and demand, as well as rising base metal costs, such as aluminium, may stymie industry development.
The tightening of pollution and fuel efficiency standards has turned automobile manufacturers' attention to alternative fuel vehicles such as compressed natural gas (CNG), liquefied natural gas (LNG), and fuel cell vehicles.
According to the 2012 efficiency requirements, the US passenger car fleet must attain an average fuel economy of 49.1 miles per gallon (mpg) by 2025, or 54.5 mpg when CO2 emissions are included in, with different credits for extra climate benefits added in.
The Global Automotive Plastic Fuel Tank Market can be segmented into the following categories for further analysis.
SI No | Timeline | Company | Developments |
1 | May 2021 | BMW | BMW has launched the small series of BMW i Hydrogen based on the current X5. The fuel cells consist of plastic and light metal castings and serves as an airtight and watertight seal for stack housing. |
2 | January 2021 | TI Fluid Systems | TI Fluid Systems has announced that it will launch a new generation of plastic fuel tank design for Volkswagen China. |
3 | Q1-2021 | Yachiyo | For the usage of Compact vehicle type Yachiyo has launched the LEV II/PZEV type plastic fuel tank. |
4 | Q1-2021 | Yachiyo | Yachiyo has developed a compliance of LEV II Plastic fuel tank mainly developed for Minivan. |
Plastic fuel tanks and systems are intended to provide the automobile industry with environmentally responsible, cost-effective, lightweight, and safe alternatives. The goal of this work is to design and numerically examine the impact strength and develop a modular prototype using high density polyethylene plastic, which is a strong and lightweight material, allowing manufacturers to significantly reduce the overall weight of their vehicles and make them more fuel efficient.
Plastic gasoline tanks also provide enhanced safety in the case of a collision. Unlike metal fuel tanks, many may bend and flatten instead of ripping, rupturing, and leaking gasoline, securely eliminating fuel leaks.
Plastic fuel tanks are composed of high-density polyethylene (HDPE), a durable and lightweight material that allows manufacturers to significantly lower the total weight of their cars while also increasing fuel efficiency. Plastic gasoline tanks also provide greater safety in the case of a collision.
In contrast to metal fuel tanks, many may bend and flatten rather of ripping, rupturing, and spilling gasoline, thereby eliminating fuel leakage as a source of a fire or explosion.
Plastic may be moulded to fit around certain components. Furthermore, plastic gasoline tanks are corrosion resistant, but steel tanks require stainless steel to offer a comparable level of corrosion resistance, which also increases the cost. Multilayer plastic tanks are now more capable than earlier monolayer tanks of meeting car emissions regulations set by the EPA and CARB.
Despite the limits of life cycle design that were shown in this demonstration, the project team learned a lot about the ecological contours of steel and HDPE fuel tank systems. Furthermore, the assessments of feat, cost, and policy concerns pertaining to fuel tank design were beneficial to all team members.
The global automotive plastic fuel tank market is expected to grow steadily in the coming years, driven by the increasing demand for lightweight and fuel-efficient vehicles, the growing popularity of electric vehicles, stringent emission regulations, and advances in plastic technology.
New and advanced plastic materials are being developed, which offer superior properties such as higher strength, lower weight, and better durability. These advanced plastic materials are expected to be used in the development of next-generation automotive plastic fuel tanks.
Governments around the world are implementing increasingly stringent emission regulations for vehicles. This is driving the adoption of technologies that can help to reduce vehicle emissions, including plastic fuel tanks.
TI Automotive, a global automotive supplier, announced that it is developing a new plastic fuel tank recycling process. The new process is expected to be able to recycle up to 95% of plastic fuel tanks. This would help to reduce the environmental impact of the automotive industry.
New and advanced plastic materials are being developed, which offer superior properties such as higher strength, lower weight, and better durability. These advanced plastic materials are expected to be used in the development of next-generation automotive plastic fuel tanks.
Smart devices such as sensors and actuators are being integrated into automotive plastic fuel tanks. These smart technologies can help to improve the safety and efficiency of fuel tanks. For example, sensors can be used to monitor the fuel level and temperature, and actuators can be used to control the flow of fuel.
The automotive industry is increasingly focused on sustainability. This is leading to a demand for more sustainable automotive components, including plastic fuel tanks. Manufacturers are developing new plastic fuel tanks that are made from recycled materials and that are more recyclable at the end of their life.
Inergy Automotive Systems, a leading supplier of automotive fuel tanks and other automotive components, has launched a new lightweight plastic fuel tank for electric vehicles. The new fuel tank is made of a new type of plastic that is stronger and lighter than traditional plastic materials. It is also more resistant to chemicals and corrosion.
Kautex, a German automotive supplier, has launched a new plastic fuel tank with an integrated fuel delivery system. The new fuel tank is designed to reduce the weight and complexity of fuel systems. It also helps to improve the fuel efficiency of vehicles.
YAPP Launches New Plastic Fuel Tank with Built-in Fuel Filter: YAPP, a Chinese automotive supplier, has launched a new plastic fuel tank with a built-in fuel filter. The new fuel tank helps to improve the quality of fuel and extend the life of the fuel filter.
TI Automotive, a global automotive supplier, has launched a new plastic fuel tank with an integrated fuel sensor. The new fuel tank helps to improve the accuracy of fuel level measurements and provides real-time data on fuel consumption.
SI No | Timeline | Company | Sales |
1 | Q3-2021 | TI Fluid Systems | The revenue of TI Fluid Systems at the end of the third quarter was â¬2.17 billion and in the previous year, the revenue was â¬1.95 billion. |
2 | Q2-2021 | Unipres | At the end of the second quarter in September, the net sales of Unipres were ¥119.3 billion and in 2020 the net sales were ¥88,000 million. |
3 | Q3-2021 | Plastic Omnium | At the end of the third quarter, the revenue of Plastic Omnium was â¬1.6 billion and in the previous year, the revenue was â¬1.92 billion. |
4 | Q3-2021 | Magna | The sales of Magna at the end of the third quarter were $7.91 billion and in 2020 the sales were $9.12 billion. |
Plastic tanks can fulfil packing limitations with complicated forms, and design engineers have more wiggle room in automobile design and style without having to worry about fitting the gas tank.
The plastic tank could almost be fashioned to suit whatever gaps the design leaves. Other connections to and within the plastic tank need of casket mechanical joints. Plastic, on the other hand, expands when exposed to organic liquids and vapour on a continuous basis.
Cadillac, on the other hand, says that while its plastic tanks allow for more design flexibility and enhanced safety, they do not save weight over steel tanks.
Textron Kautex has been part of the major ecological development of plastic-based fuel tanks. It has most recently produced the NGFS® technology, also known as âtwin sheet â, technology which helps reduce emissions and weight while potentially increasing volume depending on tank design.
It also serves as the basis for our lightweight hybrid fuel tank. NGFS® is produced by lowering two sheets of multi-layered parison through the blow moulder extruders. The "twin sheet" design allows easy access for components to be integrated directly into the plastic shell, thus eliminating the need for cutting and welding and reducing emissions.
The two half shells, with their associated components in place, are then moulded together before being removed from the bold moulder. These more complex fuel tank applications require closed fuel systems with a higher internal pressure which causes massive deformations on un-reinforced plastic tanks.
Fuel Total System is into the product innovation of the latest technology-based plastic fuel tanks. The construction technology used by the organisation is of the highest standards wherein, The high-density polyethylene fuel tanks are created through a multi-layered, blow moulding technology to ensure safety and efficiency.
Blow moulding is a manufacturing process that allows hollow plastic parts to be joined together seamlessly. They use the mass reduction technology that enables us to construct highly advanced uniformed fuel tanks. Itâs an effective process that maintains the integrity of the design for safe and effective driving.
The 6-layer, Co-Extrusion Blow Moulding process for the Fuel Tank results in low permeation to minimize fuel hydrocarbons. This produces a Fuel Tank that is environmentally friendly and meets the highest federal government requirements.
1 | Market Segmentation |
2 | Scope of the report |
3 | Research Methodology |
4 | Executive Summary |
5 | Introduction |
6 | Average B2B Price of Automotive Plastic Fuel Tank, By Region |
7 | Cost breakdown of Product by sub-components and average profit margin |
8 | Technology trends in the industry |
9 | Overview on Different Material Used in Global Automotive Plastic Fuel Tank Market |
10 | Key investment opportunities in the Automotive Plastic Fuel Tank Market |
11 | Analysis of the Automotive Plastic Fuel Tank Market by specific chemistry |
12 | Market Segmentation, Dynamics and Forecast by Geography, 2024-2030 |
13 | Market Segmentation, Dynamics and Forecast by Vehicle Type, 2024-2030 |
14 | Market Segmentation, Dynamics and Forecast by Capacity, 2024-2030 |
15 | Market Segmentation, Dynamics and Forecast by Material, 2024-2030 |
16 | Product installation rate by OEM, 2023 |
17 | Competition from substitute products |
18 | Gross margin and average profitability of suppliers |
19 | New product development in past 12 months |
20 | M&A in past 12 months |
21 | Growth strategy of leading players |
22 | Market share of vendors, 2023 |
23 | Company Profiles |
24 | Unmet needs and opportunity for new suppliers |
25 | Conclusion |