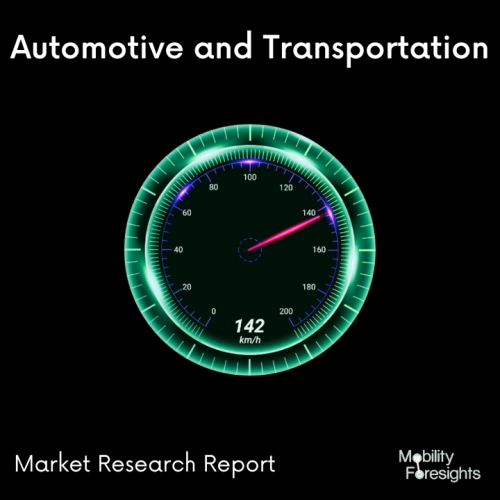
- Get in Touch with Us
Last Updated: Apr 25, 2025 | Study Period: 2024-2030
The electric vehicle inverter market is booming, driven by the increasing adoption of electric vehicles (EVs) worldwide. Inverters are a critical component of EVs, converting the direct current (DC) electricity from the battery pack into alternating current (AC) electricity to power the electric motor.
As EVs become more sophisticated and powerful, the demand for high-performance inverters is increasing. Inverters are also becoming more complex, as they need to integrate with other powertrain components, such as the motor and transmission. As EVs with longer ranges and faster charging capabilities become more popular, the need for inverters that can handle more power is growing.
As the EV market continues to grow, the demand for inverters is expected to grow as well. Inverter manufacturers are investing heavily in research and development to develop new and improved inverters that meet the demands of the next generation of EVs. Tesla, BYD, and Hyundai are the major OEMs that have insourced EV Inverters.
An electric car motor requires AC power, which is produced by an inverter, which transforms DC electricity. The frequency of the alternating current can be changed by the inverter to alter the motor's rotational speed. Coal-fired energy can be converted into electricity by an EV motor with efficiency.
To enable the electric motor to turn the wheels, the inverter transforms the direct current (DC) from the battery into the alternating current (AC) needed. In an all-electric car or a hybrid plug-in vehicle, the charger accomplishes the same duty by converting AC voltage into DC voltage in order to charge the battery.
In order to match line power, output is typically 120 or 240 volts at 60-cycle alternating current. Inverters are frequently a viable option for applications that call for the main engine to run at a job site, such as powering hydraulic systems or air compressors, because they can handle greater and longer-lasting loads.
Simply said, an inverter transforms DC (battery) power into AC power, which is subsequently sent to connected equipment. When AC utility power is available, an inverter/charger performs the same function, with the exception that it is coupled to an AC power source to continually charge the attached batteries.
The first harmonic of the inverter switching frequency for electric vehicles, which is 10 kHz, can be heard at 20 kHz. Current ripple refers to high frequency current variations on the electrical side.As fossil fuel powered engines get closer to prohibition, many OEMs are looking up to vehicle electrification as a saviour.
Battery powered electric vehicles will not become mainstream unless battery costs come down to <$100/kWh and fast charging infrastructure becomes a commonplace. Now, that leaves manufacturers with a bridge gap or a âhybridâ solution.
A 48V Mild-hybrid/Plug-in hybrid architecture can result in 10%-16% increase in fuel economy at an added cost of 6%-12% of vehicle. In any case, hybridization warrants a DC-DC converter as well as an inverter in a vehicle.
More than 2.9M plug-in vehicles were sold in China in 2023 with BYD and Tesla Model 3 leading the pack. The ability of A00 and A0 segment vehicles to be sold with minimal subsidy help will affect the overall electric vehicle inverter market positively as the market shifts away from subsidies to direct supply-demand pricing.
The range of a battery-electric vehicle is related to the efficiency of the main inverter. The dynamics of the electric vehicle inverter market is shifting away from subsidies as theyâll be phased out by the end of 2023, except for certain technologies and related infrastructure such as battery swapping. The focus in this region will remain to be BEVs with multiple high-performance BEVs gathering attention and market share such as Nio and Xpeng
Tesla Model 3 was the most sold EV. Nio ES6 was a luxury segment EV in the top 10 sold EVs in China. There were A00 segment vehicles with small battery packs in the top 10 such as SGMW Mini and Chery Eq. The sales of the A00 and A0 segment were predominantly from Tier 3 cities and beyond. Europe also saw a major increase in plugged in vehicle sales.The BEV-PHEV split was almost equal with BEVs edging by a small margin.
Wide bandgap (WBG) semiconductors: Companies like Cree, Infineon, and ROHM introduced new silicon carbide (SiC) and gallium nitride (GaN) MOSFETs and modules for inverters, offering higher efficiency, smaller size, and lighter weight.
Integrated inverters:Several players, including NXP, STMicroelectronics, and TI, launched integrated inverter solutions combining motor controller, inverter, and other functionalities into a single chip, simplifying design and reducing cost.
Wireless charging inverters:Manufacturers like Aptiv and HEVIZI unveiled new inverter designs optimized for wireless charging applications, paving the way for faster and more convenient charging experiences.
Integrated Inverters: Introduced the Aurix microcontroller family with integrated inverter control capabilities, simplifying design and reducing component count. Launched the STPOWER STEVAL-IPMxxA series of integrated power modules, combining motor driver and inverter functions for efficient and cost-effective solutions.
800V inverter platforms:Major players like ABB, Bosch, and Continental showcased 800V inverter platforms enabling faster charging speeds and potentially reducing battery size and cost.
Bidirectional inverters: Several manufacturers introduced bidirectional inverter designs that allow vehicles to feed energy back into the grid, supporting vehicle-to-grid (V2G) applications.
GaN-based invertersdeliver efficiency improvements of more than 70% compared to current inverters using traditional IGBT semiconductors that currently are the workhorses in EV and hybrid vehicle power control.
Borgwarner - Marelli, This partnership focuses on developing and supplyingintegrated electric axle systems, which include inverters. It combines BorgWarner's expertise in electrification with Marelli's motor and power electronics capabilities. This collaboration strengthens their offerings and positions them to compete effectively in the growing market for integrated EV drivetrain solutions.
Nidec - Stellantis, Nidec will supplyelectric motors and invertersfor upcoming Stellantis electric vehicles. This multi-year agreement leverages Nidec's global manufacturing footprint and Stellantis' wide vehicle portfolio. This partnership ensures a stable supply chain and access to advanced technology for both companies.
Continental - Geely,This joint venture focuses on developing and manufacturingelectric drive systems, including inverters, specifically for the Chinese market. It combines Continental's technology with Geely's local market knowledge and distribution channels. This strategic move allows them to cater to the specific needs of the rapidly growing Chinese EV market.
Electric vehicles are becoming more powerful and efficient, and this is driving the demand for high-performance EV inverters. High-performance EV inverters are more efficient and can handle higher power levels, which is essential for electric vehicles with high-performance motors and batteries.
Manufacturers are developing new EV inverter technologies to improve the performance, efficiency, and reliability of electric vehicles. For example, some companies are developing EV inverters with integrated power electronics, which can help to reduce the size and weight of electric vehicles.
The demand for EV inverters for commercial vehicles is also growing rapidly. This is due to the increasing electrification of commercial vehicles, such as buses, trucks, and delivery vans.
The transition from silicon insulated gate bipolar transistors (Si-IGBT) to silicon carbide (SiC) metal oxide semiconductor field-effect transistors is a significant development trend for inverters (MOSFET). SiC technology clearly shows its advantages in the low power range, which is the predominant operating regime for daily driving.
Key design challenges to extend range and lower costs still exist as electric vehicles gain popularity. Here, the electric powertrain's high efficiency is a key focus.
The highly integrated electric drive units (EDUs), which include an inverter, electric motor, transmission, and heat exchanger, are clearly on the rise and offer benefits in terms of package, weight, and power density.
The transition from silicon insulated gate bipolar transistors (Si-IGBT) to silicon carbide (SiC) metal oxide semiconductor field-effect transistors is a significant development trend for inverters (MOSFET). SiC technology clearly shows its advantages in the low power range, which is the predominant operating regime for daily driving.
Even more optimizations can be achieved with clever control techniques like variable switching frequency and discontinuous modulation. Higher switching speeds that result in high voltage gradients, on the other hand, present more isolation and electromagnetic interference problems.
additionally, there are technologies like two-level SiC with advanced gate drivers or soft switching technology, current source inverters with dual blocking devices, three-level gallium nitride (GaN) technology implementation on DC-DC converters, and traction inverters.
Power Electronics: The development of electric car inverters has benefited greatly from the science of power electronics.The switching speed and efficiency of inverters have increased thanks to developments in semiconductor technology, including insulated-gate bipolar transistors (IGBTs) and silicon carbide (SiC) MOSFETs. These developments have reduced power losses, allowing for higher power densities and increased system efficiency in general.
High-frequency switching techniques have been included into inverters for electric vehicles. Reduced system space and weight result from the use of lighter and smaller passive components like inductors and capacitors at higher switching frequencies.High-frequency switching also reduces electromagnetic interference (EMI) and enhances the vehicle's general electromagnetic compatibility (EMC).
Heat Management: Reliable operation of electric car inverters depends on effective heat management. The improvement of cooling systems has been the subject of technological advancements, such as liquid cooling or sophisticated air cooling methods. These developments increase the efficiency and dependability of the system by helping to disperse the heat produced by the inverter and guarantee ideal operating temperatures.
Technology improvements have made it possible to combine several powertrain parts, such as the inverter, motor controller, and other power electronics, into a small, lightweight package.This integration enhances overall efficiency, simplifies wiring and linkages, and reduces system complexity.
Semiconductors with a Wide Bandgap: Wide bandgap semiconductors, such gallium nitride and silicon carbide, have showed promise in enhancing the efficiency of inverters used in electric vehicles. In comparison to conventional silicon-based semiconductors, these materials offer larger breakdown voltages, faster switching rates, and lower conduction losses.
Higher inverter efficiency, power density, and operating temperatures are made possible by wide bandgap semiconductors.sophisticated control algorithms The performance and efficiency of inverters for electric vehicles have been significantly improved because to the development of sophisticated control algorithms. With the help of these algorithms, the switching frequency, voltage, and current of the inverter may be precisely controlled to increase motor performance, regenerative braking effectiveness, and general vehicle dynamics.
Grid Integration and Vehicle-to-Grid (V2G) Capabilities: As electric vehicles proliferate, technological advancements have concentrated on allowing grid integration and V2G capabilities.
Electric car inverters with bidirectional power flow characteristics enable vehicles to transfer energy from one vehicle to another or from one building to another, providing grid stabilization.Electric vehicle inverters employ a number of technologies to make them easier to use and perform better.
Sl no | Topic |
1 | Market Segmentation |
2 | Executive Summary |
3 | Avg B2B price of Inverters, By Region |
4 | 5 Key Predictions for EV Inverter Market |
5 | Insights From Industry Stakeholders |
6 | Breakdown of upcoming EVs by powertrain |
7 | EV Product Plan Of OEM’s (Top 10 OEMS) –2024-2030 and expected volumes |
8 | Latest Innovation/New Product Launch In EV Inverter Market |
9 | Key Criteria For EV Inverter vendor selection By OEMs |
10 | Cost breakdown of EV inverter-2023 |
11 | Rise in development of 400V & 800V Architecture and impact on EV inverter market |
12 | Usage of Gallium Nitride and Silicon Carbide in EV inverter |
13 | Global EV traction motor market overview and correlation with EV Inverter Market |
14 | Comparison of inverters available in the market by major suppliers |
15 | Growing popularity of Integrated DC-DC converter and inverter |
16 | Upcoming EVs by region and outsourced inverter volume per annum |
17 | Rise in average battery capacity and impact on EV Inverter Market |
18 | Market Size, Dynamics And Forecast By Geography, 2024-2030 |
19 | Market Size, Dynamics And Forecast By Electric Vehicle Type, 2024-2030 |
20 | Market Size, Dynamics And Forecast By Inverter Power, 2024-2030 |
21 | Market Size, Dynamics And Forecast By Vehicle type, 2024-2030 |
22 | Gross Margin On EV Inverter And Breakup By Sub Components |
23 | Competitive Landscape of EV Inverter Market |
24 | OE-Supplier Alignment in EV Inverter Market |
25 | Market share of EV Inverter Market-2023 |
26 | Recent Mergers and Acquisitions |
27 | Company Profiles |
28 | Unmet needs and Market Opportunity for suppliers |
29 | Conclusion |