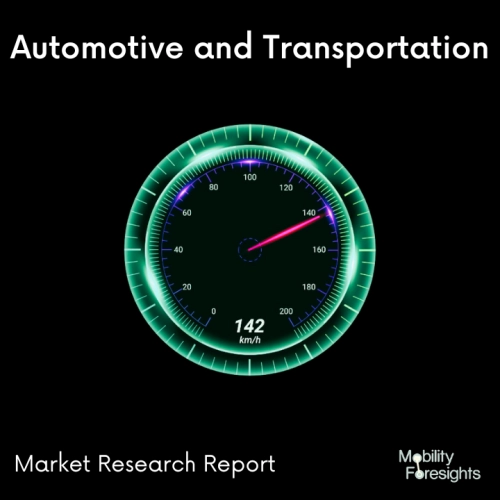
- Get in Touch with Us
Last Updated: Apr 25, 2025 | Study Period: 2024-2030
INTRODUCTION TOEUROPE EV TRACTION MOTOR MARKET
The system that causes the propulsion of a vehicle in which that driving force or tractive force is obtained from various devices such as electric motors, steam engine drives, diesel engine dives, etc. is known as traction system.
Traction systems may be broadly classified into two types. They are electric traction systems, which use electrical energy, and non-electric traction systems, which do not use electrical energy for the propulsion of vehicles.
In most cases, no one traction system meets the requirements of an ideal traction system, because each traction system has its own strengths and flaws in terms of application sectors. Ideal traction system should have the capability of developing high tractive effort in order to have rapid acceleration and also the speed control of the traction motors should be easy.
The selection of the most efficient and cost-effective electric machine is a major difficulty. Permanent magnet synchronous machines (PMSMs) and switching reluctance machines (SRMs) are constantly improving for EV and HEV applications, whereas induction machines (IMs) are regarded as mature. The standards for designing induction machines haven't changed in decades.
In EV/HEVs, electric motor drives are the most essential component. In a series hybrid vehicle, the electric motor drive is usually the only source of torque. The electric motor is the torque source in parallel and seriesâparallel hybrid cars, providing peak torque (power) to fulfil vehicle performance requirements such as acceleration.
To know more about Global EV Traction Motor Market, read our report
S No | Overview of Development | Development Detailing | Region of Development | Possible Future Outcomes |
1 | Lucid Motors â EV Motor Manufacturing giant to enter Europe | Lucid Motors plans to begin delivering its cars in Germany next year, as the new Country Manager Roberto Russo, confirmed to elective. Also in 2022, the Air sedan is to arrive in other European countries too. | EU | The Company would focus on mobilizing EVs in the EU alongside possible new editions of motor productions in place. |
2 | EU Public policy push towards EV Motors | European Union formally proposed a phaseout of the internal combustion engine by 2035 alongside replacement with EV Traction based motors | EU | This policy would help in better electrification prospects and adoption of EVs |
3 | Protean In Wheel EV Motors to the commercialization | Protean has made an attempt to attaching the EV Motors into Wheel based alignment | EU | This can lead to the establishment of new EV Production factories. |
Europe is getting involved in enhanced technologies of traction systems alongside other component based technological implementations being kept in place at all times within the EV Segment of manufacturing and operations in the EU nations. Europe thereby has been taking on a focused approach on developing a better adoption technology to enhance EV Adoption throughout its union nations.
In recent days, Brushless motors with one slot coil pitch windings, transverse flux motors, careless disc type motors, and PM aided synchronous reluctance motors are all examples of modern permanent magnet (PM) motor technologies being brought into integration in the Europe Market. Liquid-cooled traction motors and inverters are gaining popularity because they reduce the size of electromechanical drive systems.
The overarching driver for new motors and power interfaces is coming from the electrification of vehicles. While this encompasses related areas such as public transportation, railways and other applications, the lionâs share of development and volume deployment is coming from consumer markets for EVs.
There has been a profusion of diverse motor designs and specifications due to the worldwide competitive climate and growing demand for consumer focused EVs. Large primary traction drive single-motor applications with hairpin windings are among the numerous uses (most common application) and Currently, the market is focused on large primary traction motors with evolutionary trends moving toward multiple drive motors and integrated drivetrains.
The Europe EV Traction motor Market can be segmented into following categories for further analysis.
Drive systems for hybrid electric car drive motors must be as efficient as industrial motors in manufacturing plants and commercial buildings. The size and weight of the engine is maybe more essential. For these reasons, a permanent magnet motor with high performance magnets is likely to be the first motor type considered for vehicle drives.
The mostly used internal permanent magnet (IPM) motor has been the popular choice for electric traction drive systems for some years. However, with fast rising magnet costs and the prospect of a future shortage of rare-earth (RE) metals, IPM motors may not be economically or technically viable in the future. An IPM motor is a hybrid that uses both reluctance torque and magnetic torque to improve efficiency and torque.
These motors are created by adding a small number of magnets inside the barriers of a synchronous reluctance machine. They have excellent torque, efficiency, and low torque ripple.
However, PM motors inherently have short constant power range due to its rather limited field weakening capability, resulting from the presence of the PM field, which can only be weakened through production of a stator field component, which opposes the rotor magnetic field.
These technological implementations are based upon the use of additional field windings to extend the speed range of permanent magnet motors. The key is to control the field current in such a way that the air-gap field provided by PMs can be weakened during high-speed operations. Due to the presence of both PMs and the field windings, these motors are so-called PM hybrid motors. The PM hybrid motor can achieve a speed ratio of around four.
When the commutation angle advance is varied, SDT Drive Technology has developed a wide range of high-performance brushless motor drives and a method of control embodied in electronic component architecture and software code (Phase Advance Control) that allows high-speed operation above the base speed that is achievable with constant DC bus voltage.
There has been constant technology battery adoption and automated control system implementation within the EV battery market of Europe. The major stakeholders are involved in implementing new strategies of technology to have a better and safer ride for the customers.
ABB Europe has started and majored its focus into Electric based traction motors to be brought into action throughout the EV Mobility considering its latest Policy implantation and foundational changes of mobility solutions towards electric based propulsion. This has made ABB enter into the technologically advanced development of traction motors for EVs in the Europe,
ABBâs e-mobility motors for heavy working machines are optimized for each machineâs work cycle and specific customer preferences. These motors are making headway fast in applications such as mining, construction, material handling, agriculture, airport vehicles, etc.
It has an operational power level from 90 kW up to 750 kW with Liquid cooling with up to 65°C coolant temperature. It is available under rate technologies of Induction, SynRM and Permanent magnet-based propulsion.
The Siemens Europe Mobility Solution has deployed the SIMOTICS electric motors are synonymous with quality, innovation, and the highest efficiency. The technology of Severe Duty motors with their rugged Gray cast iron housing are the first choice for all important applications in normal industrial settings as well as under harsh ambient conditions.
They operate reliably in a temperature range from -50 °C to +60 °C. Degrees of protection up to IP66 and a coating system up to C5 (offshore duty) permit operation in humid, dusty, or vibrating environments as well as in aggressive atmospheres.
Sl no | Topic |
1 | Market Segmentation |
2 | Scope of the report |
3 | Abbreviations |
4 | Research Methodology |
5 | Executive Summary |
6 | Introduction |
7 | Insights from Industry stakeholders |
8 | Cost breakdown of Product by sub-components and average profit margin |
9 | Disruptive innovation in the Industry |
10 | Technology trends in the Industry |
11 | Consumer trends in the industry |
12 | Recent Production Milestones |
13 | Component Manufacturing in US, EU and China |
14 | COVID-19 impact on overall market |
15 | COVID-19 impact on Production of components |
16 | COVID-19 impact on Point of sale |
17 | Market Segmentation, Dynamics and Forecast by Geography, 2024-2030 |
18 | Market Segmentation, Dynamics and Forecast by Product Type, 2024-2030 |
19 | Market Segmentation, Dynamics and Forecast by Application, 2024-2030 |
20 | Market Segmentation, Dynamics and Forecast by End use, 2024-2030 |
21 | Product installation rate by OEM, 2023 |
22 | Incline/Decline in Average B-2-B selling price in past 5 years |
23 | Competition from substitute products |
24 | Gross margin and average profitability of suppliers |
25 | New product development in past 12 months |
26 | M&A in past 12 months |
27 | Growth strategy of leading players |
28 | Market share of vendors, 2023 |
29 | Company Profiles |
30 | Unmet needs and opportunity for new suppliers |
31 | Conclusion |
32 | Appendix |