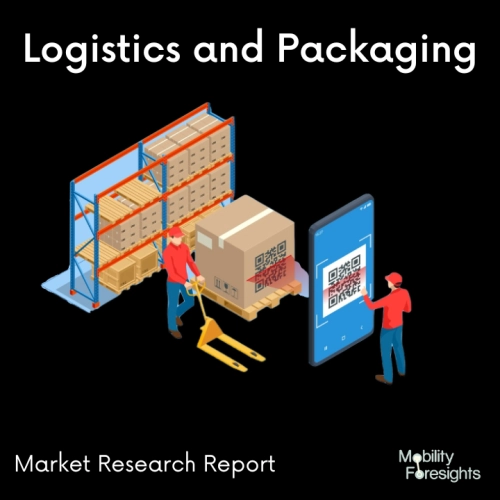
- Get in Touch with Us
Last Updated: Apr 25, 2025 | Study Period: 2023-2030
An automated guided vehicle (AGV) is an automated, unmanned ground vehicle capable of navigating autonomously in a predetermined pathway. AGVs are used in many industries, such as manufacturing, warehousing, and logistics, to move goods and materials from one place to another.
AGVs are commonly used in environments where human operators are not allowed to enter, such as hazardous or restricted areas. AGVs are also used in applications where consistent and precise movement is needed, such as automated assembly lines.
AGVs are typically equipped with sensors and cameras that allow them to detect their surroundings and navigate in a predetermined path. They can also be programmed to recognize and respond to obstacles, such as people or other objects, that they encounter while moving.
AGVs are also equipped with several different types of communication systems, such as radio frequency, infrared, or laser, that allow them to communicate with other vehicles and the control system.
AGVs can be single-forked or double-forked. Single-forked AGVs are designed to move a single load, while double-forked AGVs are designed to carry two loads at once. AGVs are powered by either electric motors or diesel engines, and many can reach speeds of up to 15 mph.
AGVs are becoming increasingly popular in the manufacturing and warehousing industries, as they are able to reduce the labor and costs associated with manual material handling. Additionally, they can help increase throughput and reduce errors, as they are able to consistently and precisely move goods with minimal human intervention.
To know more about Global Automated Guided Vehicle Market, read our report
The Global forked automated guided vehicle market accounted for $XX Billion in 2022 and is anticipated to reach $XX Billion by 2030, registering a CAGR of XX% from 2023 to 2030.
A variety of standard Automated Guided Vehicle models are available from MAXAGV. The FX and CX ranges of MAXAGV are fork-type automated guided vehicles and load carriers, respectively.
In addition to the conventional models, they also provide heavy load Automated Guided Vehicles (AGVs) and manual forklift trucks (FLTs) that have been converted into AGVs, as well as custom designs for the task at hand. When it comes to transporting cargoes to conveyors or warehouse marshalling with deep stacking lanes, FX Forked AGV can work as floor-to-floor or floor-to-racking.
A wide range of unit loads, including various pallets, roll cages, containers, paper reels, industrial stillages, and deep stacking shuttle cars, can be transported by the automated guided vehicle.
The forked automated guided vehicle from Wuwer takes up and releases cargo as it travels between the loading and unloading locations. Specifically designed retractable prongs on our gadget allow it to pick up and place the box directly onto the trolley (horizontal movement) and then lower it to the unloading site's floor (vertical movement) once it has been transported.
Because charging stations are situated near loading and unloading areas, we make the best use of the AGVs operating hours.When moving around and carrying out tasks, such picking up or dropping down supplies, an automated guided vehicle (AGV) responds to a set of preprogrammed commands, cues, or signals.
Due to their efficiency, AGVs are a crucial part of supply chain automation.In situations where a business is having trouble finding and keeping competent employees, AGV's predictability is extremely important.
The great precision is still quite significant. The precision of an AGV depends directly on how accurately it is positioned, which is often decided by its navigation system. With a positioning accuracy of about one centimetre, their AGVs are more than adequate for the majority of intralogistics and industrial applications.AGVs are far less likely than their manually operated counterparts to be engaged in hazardous circumstances or accidents.
Sl no | Topic |
1 | Market Segmentation |
2 | Scope of the report |
3 | Abbreviations |
4 | Research Methodology |
5 | Executive Summary |
6 | Introdauction |
7 | Insights from Industry stakeholders |
8 | Cost breakdown of Product by sub-components and average profit margin |
9 | Disruptive innovation in theIndustry |
10 | Technology trends in the Industry |
11 | Consumer trends in the industry |
12 | Recent Production Milestones |
13 | Component Manufacturing in US, EU and China |
14 | COVID-19 impact on overall market |
15 | COVID-19 impact on Production of components |
16 | COVID-19 impact on Point of sale |
17 | Market Segmentation, Dynamics and Forecast by Geography, 2023-2030 |
18 | Market Segmentation, Dynamics and Forecast by Product Type, 2023-2030 |
19 | Market Segmentation, Dynamics and Forecast by Application, 2023-2030 |
20 | Market Segmentation, Dynamics and Forecast by End use, 2023-2030 |
21 | Product installation rate by OEM, 2023 |
22 | Incline/Decline in Average B-2-B selling price in past 5 years |
23 | Competition from substitute products |
24 | Gross margin and average profitability of suppliers |
25 | New product development in past 12 months |
26 | M&A in past 12 months |
27 | Growth strategy of leading players |
28 | Market share of vendors, 2023 |
29 | Company Profiles |
30 | Unmet needs and opportunity for new suppliers |
31 | Conclusion |
32 | Appendix |