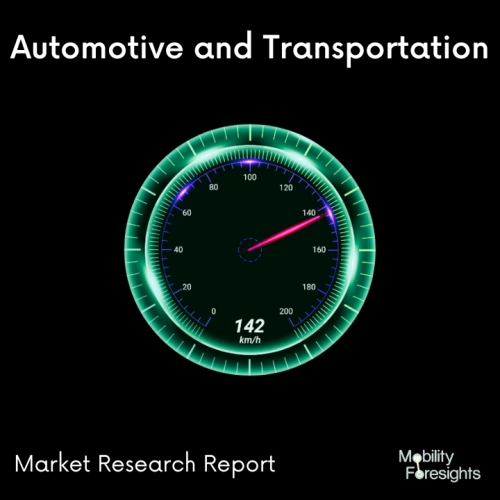
- Get in Touch with Us
Last Updated: Jul 09, 2025 | Study Period: 2025-2031
An electric drivetrain of an HEV or EV consists of a wide variety of electronics such as high-voltage batteries and motors. They are connected by high-voltage wiring harnesses for power transfer.
A wiring harness is an organized set of wires, terminals and connectors that run through the vehicle and relay information and electric power, thereby connecting a variety of components. Power and information travel through this delicate network.
The wiring harness in the vehicle is one of the heaviest and most expensive individual parts of a car (after the engine and transmission). In addition, the vast range of variants of today's vehicle models requires a tailor-made cable system for almost every possible configuration as there is considerable change in various systems from vehicle to vehicle
Electric vehicles require additional expensive high-voltage lines for AC-DC charging, high-voltage batteries and, traction as well as special wiring for the high-voltage battery and the battery management system. GM is bringing about a wireless battery management system in their new electric vehicle platform Ultium.
To know more about Global Automotive Wiring Harness Market, read our report
The changes in vehicle electronics will also result in a variety of changes in cable and cable channels:
In future data-driven business models which is gaining traction right now across manufacturers, some functions may only be temporarily enabled via OTA software updates.
In the case of electric vehicles, this can also include the motor performance. For car manufacturers to be able to implement such functions, the cabling must be designed for the maximum possible performance, even if this is rarely required at all due to the uncertainty of usage and also preparing for shifts in business models at any time.
Since the most recent electrical connectivity enables an increasing number of signals from on-board sensors, other vehicles, road-based infrastructure, and satellites to be streamed into a high-performance computer, the next-generation wire harness will enable more powerful electrical systems to operate vehicles. The wire harness will then be used by the computer to transmit signals to the brake, steering, and other control systems.
All of this is developing into a technical infrastructure for electrification and autonomous driving, which is an appealing vision but one that is not without its challenges. Undoubtedly, wire harnesses are developing quickly to deal with the issues presented by electrification and autonomous driving.
In addition to energy recovery and some other auxiliary technology, the bigger battery is the car's important design idea, so proper body layout, sufficient interior space, and apt safety features also put forward a higher design requirement. The soft, high bending radius of the wiring harness on the compact installation space is particularly important.
The thin-walled wire is a good choice for improving the softness of the wiring harness and reducing the space occupied by the wiring harness. However, compared with the thick insulation wall wire, its wear resistance, temperature and pressure resistance will achieve a higher performance claim.
Performance check for electric wire harness
Harness passes through many areas where it requires protection against heat, dust, moisture etc. Wire harness protection prevents damage caused by wire vibration damage, abrasions and incidental contact with other pieces of heat-producing equipment.
Thermal management tubes and sleeves are designed to operate under high temperatures and provide fire resistance under extreme conditions. The tubes and sleeves must be difficult to ignite, and they must self-extinguish promptly. The most common types of cable and wire protection arebraided sleeving,corrugated loom,heat shrink,vinyl tubing, andconduit.
A typical wiring harness drawing has cable lengths, component view, grommet, connector specifications and inline connectors.
Up until this point, the Leoni simulation process had difficulty keeping up with the number of iterations required to determine the ideal location for our harnesses. Design Space Exploration, the main component of this new strategy, employs an optimization algorithm to repeatedly approach the best harness design in a pre-specified space.
They have accelerated their procedures to be completed in less than 24 hours thanks to this new strategy, giving them more time to align with clients on data quality.
The use of a simulation toolchain is already integrated into routine business operations. It covers a broad range of tasks, including electrical wire dimensioning for harnesses, designing mechanical components and their structures, placing and cooling electronics PCBs properly, and designing injection tooling to ensure proper moulding procedures.
Additionally, they have begun the dynamical simulation of certain important harness routing, such as door and trunk opening, driveline and axle connection, etc. The objective is to guarantee the proper performance and eliminate any chance of clinch, break, etc. by ensuring the suitable positioning and qualities, such as harness length.
A precise grasp of the various cables to model serves as the foundation for the cable simulation. In order to extract all cable parameters based on laser measurement and with high accuracy, such as bending qualities, LEONI has invested in a characterisation device called Mesomics.
The cable simulation models that will be used in projects can be tailored using these parameters, which are integrated into the database.
Engineers will route the harnesses according to guidelines and their own experience in a project using the 3D mechanical design and environment to simulate tensions and bending radius.
An derived fatigue index from the simulation is shown as a traffic light to draw attention to unsafe circumstances. Up until a suitable routing is reached, changes to the fixation points, length, etc., will be evaluated iteratively.
To know more about Global EV Connector Market, read our report
The global electric vehicle (EV) wiring harness market can be segmented in a number of ways, including
The global electric vehicle (EV) wiring harness market is expected to grow from USD 4.8 billion in 2023 to USD 12.5 billion by 2030, at a CAGR of XX%.
The increasing adoption of EVs is the primary factor driving the growth of the global EV wiring harness market. EVs are becoming increasingly popular due to their environmental benefits, lower operating costs, and government support. As the number of EVs on the road increases, the demand for EV wiring harnesses is also expected to increase.
SI No | Company/Region | Developments |
1 | Aptiv | Aptiv has launched a new high-voltage EV wiring harness solution that is designed to support the next generation of electric vehicles. The new solution is lighter, more compact, and more durable than previous generations of EV wiring harnesses |
2 | Fujikura | Fujikura has launched a new lightweight EV wiring harness that is designed to reduce the weight of electric vehicles and improve their range. The new wiring harness is made with new materials and manufacturing processes that make it lighter and more durable than previous generations of EV wiring harnesses. |
3 | Yazaki | Yazaki has launched a new EV wiring harness with integrated sensors. The new wiring harness includes sensors that can collect data on the vehicle's performance and operating conditions. This data can be used to improve the efficiency and reliability of the vehicle |
4 | Sumitomo Electric Wiring Systems | Sumitomo Electric Wiring Systems has launched a new EV wiring harness with integrated communication modules. The new wiring harness includes communication modules that allow the vehicle to communicate with other vehicles and infrastructure. This can be used to improve safety and efficiency. |
Delphi Technologies has launched a new EV wiring harness with integrated sensors that can collect data on the vehicle's performance and operating conditions. This data can be used to improve the efficiency and reliability of the vehicle.
The California firm partnered with WeWire for its first vehicle model, the Lucid Air, in the wire harness industry. Wewire's engineers were able to create prototypes of the necessary parts in a record-breaking six weeks.
Here, the ability of WeWire to create specialized and, more importantly, lightweight plastic mounts, was key. Thus, the Lucid Air is the first electric vehicle to be fully outfitted with mounts made of plastic that was created in-house by WeWire.
A factory for car wiring harnesses will be built in Guatemala by Yazaki North America Inc., a manufacturer of automotive components. The new facility will be built in Guatemala's San Marcos Department's municipality of Ayutla.
The majority of automakers, including several in the developing electric mobility industry, are supplied by Yazaki. Additionally, the company is extending its business portfolio in telematics and energy systems.
Each SINBON automotive wiring harness has undergone a complete breakover and high voltage test. The 3,200 V breakdown voltage is suitable for EV battery pack power transmission. To increase productivity, wire is cut and treated semi-automatically. SINBON uses high-precision quad points crimping for the crimping process.
1 | Market Segmentation |
2 | Scope of the report |
3 | Research Methodology |
4 | Executive Summary |
5 | Automotive Wiring Harness Suppliers Manufacturing Footprint |
6 | Wiring Harness Content per Vehicle, By Vehicle Type |
7 | Components of a Automotive Wiring Harness System |
8 | Technological Improvements & Key Trends in Automotive Wiring Harness |
9 | Major Drivers of Global Automotive Wiring Harness Market |
10 | New Product Development In Automotive Wiring Harness Market |
11 | Automotive Sales In Global, 2025-2031 |
12 | Top Selling EV Passenger Vehicles in Global Market |
13 | Popular Electric 2 & 3 Wheeler Vehicles In Global Market |
14 | Market Size And Forecast – By Vehicle Type – 2025-2031 |
15 | Market Size And Forecast – By Application – 2025-2031 |
16 | Market Size And Forecast – By Component – 2025-2031 |
17 | Market Size And Forecast – By Geography– 2025-2031 |
18 | Competitive Landscape |
19 | Market Share Of Major Players |
20 | Growth Strategy Of Leading Players |
21 | Mergers And Acquisitions |
22 | Company Profiles |
23 | Unmet Needs & Opportunity for New Vendors |
24 | Conclusion |