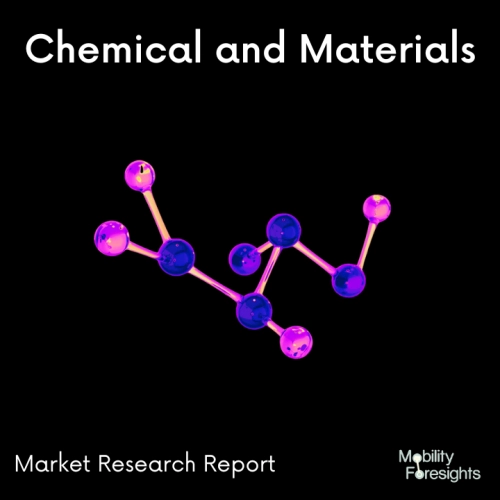
- Get in Touch with Us
Last Updated: Jul 17, 2025 | Study Period: 2024-2030
The US steel market is poised for modest growth over the next six years, driven by several key factors. Increased focus on infrastructure spending in the US, particularly for transportation projects, is expected to boost demand for steel products like rebar. Additionally, a growing manufacturing sector could create further demand for steel used in machinery and equipment.However, the US steel industry also faces challenges. Trade tensions, particularly with China, continue to be a concern. A flood of cheap steel imports could put downward pressure on prices and hurt domestic producers.
Environmental policies are another factor to watch. The push for sustainable practices could lead to increased production costs for steelmakers, as they invest in cleaner technologies. A potential carbon border tax could also impact the competitiveness of US steel in the global market.On the positive side, there's a growing emphasis on using American-made steel in construction projects. Government incentives and advocacy from industry groups could bolster domestic demand. Technological advancements in steel production are also worth noting. Research into lighter, stronger, and more corrosion-resistant steel alloys could open up new markets and applications.
Overall, the US steel market in 2024-2030 is likely to see a tug-of-war between growth drivers and potential roadblocks. The outcome will depend on various factors, including government policies, global trade dynamics, and technological innovation in the steel industry itself. US is the third largest steel producer in the world, with nearly 5.4% share in the world crude steel production, as well as one of the leading steel consumers.
The industry has benefitted from soaring steel demand in the automotive, construction and oil & gas sectors. Additionally, the cost effective and highly efficient steel making technologies have worked as a catalyst and uplifted the US steel demand in the market. Steel is primarily produced using one of two methods: Blast Furnace or Electric Arc Furnace. The blast furnace is the first step in producing steel from iron oxides. The first blast furnaces appeared in the 14th century and produced one ton per day.
The first electric arc furnaces (EAFs) appeared in the late 19th Century. The use of EAFs has expanded and now accounts for nearly 2/3 of steel production in the United States.The EAF is different from the blast furnace as it produces steel by using an electrical current to melt scrap steel and/or direct reduced iron. The EAF uses scrap steel and electricity to produce molten steel.
To know more about Europe Steel Market, read our report
The American steel industry operates with the lowest energy consumption per ton of steel in the world. The American steel industry has reduced its CO2 emissions per ton of steel shipped by 37 percent since 1990.
Steel is a versatile and widely-used alloy primarily composed of iron and varying amounts of carbon, along with other elements such as manganese, chromium, and nickel. It is renowned for its strength, durability, and adaptability, making it an indispensable material across numerous industries including construction, automotive, aerospace, and manufacturing.
There are several types of steel, each with distinct properties and applications. Carbon steel, the most common type, is prized for its strength and affordability, while stainless steel offers corrosion resistance and aesthetic appeal, making it ideal for architectural and food processing applications. Alloy steels contain additional elements to enhance specific properties such as hardness, toughness, or heat resistance, catering to specialized needs in engineering and manufacturing.
The benefits of steel are manifold. Its exceptional strength-to-weight ratio makes it ideal for building robust structures while minimizing material usage, enhancing cost-effectiveness and sustainability. Steel's durability ensures longevity and resilience against harsh environmental conditions, reducing maintenance costs over time. Additionally, its recyclability makes it a sustainable choice, contributing to circular economy principles by minimizing waste and conserving resources.
Despite its myriad advantages, steel production and usage pose certain risks and challenges. Environmental concerns arise from the energy-intensive nature of steel manufacturing, which contributes to carbon emissions and other pollutants. Moreover, the extraction and processing of raw materials like iron ore entail environmental impacts such as habitat destruction and water pollution. In terms of usage, steel structures may be susceptible to corrosion and degradation over time, necessitating maintenance and protective measures to ensure longevity.
Furthermore, fluctuations in raw material prices and market demand can pose financial risks to steel producers and consumers alike. Geopolitical factors, trade disputes, and regulatory changes also introduce uncertainty into the industry landscape, affecting supply chains and pricing dynamics. Additionally, technological advancements and evolving customer preferences necessitate ongoing innovation and adaptation within the steel sector to remain competitive and meet changing market demands. Overall, while steel offers unparalleled advantages in various applications, addressing its associated risks and challenges requires a holistic approach encompassing technological innovation, sustainable practices, and strategic planning.
To know more about India Steel Market, read our report.
By bringing pig iron production to Gary Works, United States Steel Corporation has claimed that it is advancing its metallics strategy. Up to 500,000 tones of pig iron will be produced annually thanks to the roughly $60 million investment, which will also supply a vital raw material input for its electric arc furnaces (EAF). Once finished, the Gary pig iron output is anticipated to provide approximately half of Big River Steel's other ore-based metallics requirements, generate run-rate enterprise EBITDA benefits of over $30 million, and have an internal rate of return of more than 30%.
Low-cost iron ore is a significant competitive advantage for U. S. Steel. A major competitive differentiation for the expanding fleet of electric arc furnaces is the ability to control this crucial input in the steelmaking process. In addition to improving Big River Steel's cost structure, the choice to self-fund pig iron production rather than contract it out is anticipated to generate value to Gary Works by increasing blast furnace efficiencies without diminishing Gary Works' raw steel output.
Construction is anticipated to start in the first half of the year, and the permitting process is already under way.As Massachusetts-based Boston Metal announced a $120 million investment from the second-largest steelmaker in the world, ArcelorMittal, along with cooperation from software behemoth Microsoft, the production of "green steel" came one step closer to becoming a reality.With the additional funding, Boston Metal will help Brazil's commercial manufacturing get off the ground and increase output at a prototype plant in Woburn, close to Boston. The business transforms iron ore into steel using renewable energy.
In Huntsville, Alabama, SCOA Subsidiary Steel Summit Holdings (SSH), Toyota Tsusho America, Inc. (TAI), and Southern Mobility Products unveiled Madison Metal Processing (MMP), a pioneering joint venture. Hot-rolled steel, cold-rolled steel, exposed and coated steel products, as well as blanking and warehousing steel goods, will be MMP's areas of expertise. This plant aims to process up to 5,000 tones of steel per month for Mazda Toyota Manufacturing, U.S.A., Inc. (MTMUS) as an automotive-blanking steel processing center. Because Huntsville, also known as "Rocket City," has a long history in the space sector, MTMUS's first two auto production lines are named "Apollo" and "Discovery."
For nearly 40 years, Sumitomo Corporation Group has provided flat roll goods exclusively to Mazda's manufacturing facilities in Japan, China, Thailand, and Mexico through our regional service centers. Together with Xcel Energy and EVRAZ North America, the largest solar energy company in the world, Light source bp, celebrated the dedication of its 300 megawatt Bighorn Solar project today.Light source bp, a 50:50 joint venture between bp and Light source, presented the solar project that would support more than 1,000 employment at EVRAZ's Pueblo steel mill, the first steel mill in the world to be powered primarily by solar energy, and help cut emissions.
With more than 750,000 solar panels covering virtually all of the plant's annual electricity needs, it is the largest on-site solar installation in the US that is exclusively focused on a single customer. As a result, the mill will be able to create some of the greenest steel and steel products on the planet. The company already reuses scrap metal to create new steel products, including some of the most environmentally friendly rail in the entire world.
The U.S. steel industry produced a projected 91 billion U.S. dollars in 2020, a 12 percent slump from the 2019 production value which was over 100 billion, with about 51 companies operating in the raw steel production market in the country. One of the largest steel producers in the United States is the North-Carolina-based Nucor Corporation.
In the 2020 financial year, the steel producer recorded some 20 billion in revenue. In a global comparison of crude steel producers, Nucor was ranked fourteenth in 2020, producing around 25.49 million metric tons of crude steel. Other companies developing new technologies and lightweight steels as per the industry requirement to gain the demand in forecasting period 2022-2027 and reaching green steel production.
Cleveland-Cliffs Inc., originally Cliffs Natural Resources, is an organization with headquarters in Cleveland, Ohio, that focuses on the mining, beneficiation, and palletization of iron ore as well as steel production, including stamping and tooling. It is North America's biggest producer of flat-rolled steel.
For the second year in a row, General Motors awarded AK Steel the title of GM Supplier of the Year for Non Fabricated Steel. At the annual Ford World Excellence Awards, AK Steel also received a Smart Pillar Award from Ford for being a top-performing global supplier.
The company's products are utilized in landing gear, shaft collars, safety wires, power generation goods, intervertebral disc arthroplasty, engine valves, and welding's. Carpenter Technology Corporation develops, manufactures, and distributes stainless steels and corrosion-resistant alloys.
American steel manufacturer Steel Dynamics, Inc., also referred to as "SDI," is situated in Fort Wayne, Indiana.The corporation ranks as the third largest manufacturer of carbon steel products in the United States, with a steel production capacity of 13 million tonnes. In terms of profit margins and operating margin per tone, it is one of the most profitable American steel producers.
Key suppliers of steel products in U.S. suppliers of Steel Stock and Formed steel shapes are:
S No | Titles |
1 | Market Segmentation |
2 | Scope of the Report |
3 | Research Methodology |
4 | Executive Summary |
5 | Introduction |
6 | Average B-2-B Selling Price in Past 5 Years |
7 | Insights from Industry Stakeholders |
8 | Cost Breakdown of Product Components and Average Profit Margin |
9 | Disruptive Innovation in the Industry |
10 | Technological Innovations in US Steel Market 2025-2031 |
11 | Steel Production Technologies |
12 | Material Science and Steel Development |
13 | Sustainability in Steelmaking |
14 | Surface Treatments and Coatings |
15 | Testing and Quality Control |
16 | Regulations and Standards |
17 | Future Outlook and Technological Trends |
18 | New Product Development in the Past 12 Months |
19 | Market Size, Dynamics, and Forecast by Geography (2025-2031) |
20 | Market Size, Dynamics, and Forecast by Product Type (2025-2031) |
21 | Market Size, Dynamics, and Forecast by Application (2025-2031) |
22 | Market Size, Dynamics, and Forecast by Technology (2025-2031) |
23 | Competitive Landscape and Market Share Analysis |
24 | Growth Strategy of Leading Players |
25 | Market Share of Vendors (2024) |
26 | Company Profiles |
27 | Unmet Needs and Opportunities for New Suppliers |
28 | Conclusion |